Share



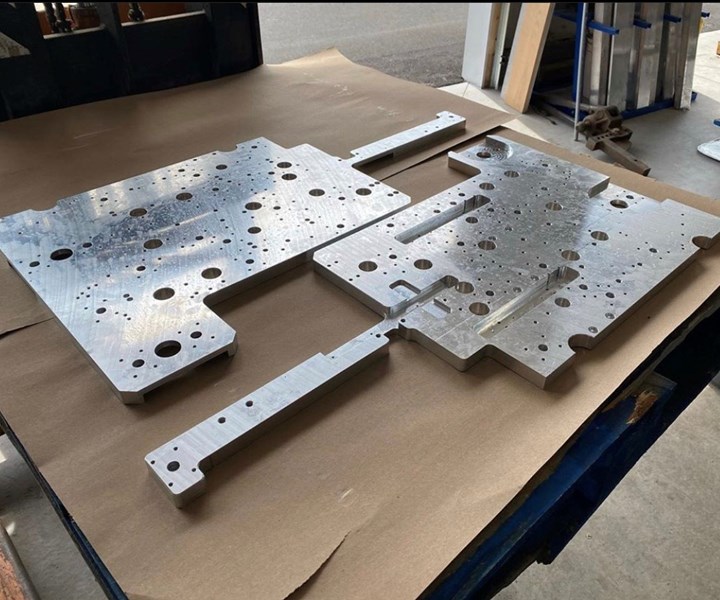
Brad Thomas machined these two aluminum plates for Oak River Technology, a company that builds custom automation equipment. He ranks them in the top three most complex plate jobs he’s produced since starting Marvel Machining, a one-man shop.
When Brad Thomas posted a picture of the parts on Marvel Machining’s Instagram page, he added the caption, “Not going to miss these at all.” One look at them and it’s easy to see why he felt that way. The parts, which were part of a job for Oak River Technology, a company that builds custom automation equipment, are two large aluminum plates. They have a long, narrow section hanging off one side, and they’re completely covered in holes and pockets of various sizes. And because Marvel Machining is a one-man shop, Thomas was responsible for all aspects of producing this part, from quoting and ordering material to programming and machining.

Brad Thomas started Marvel Machining in 2013, running a programmable three-axis machining center in a two-car garage at night. When work picked up in 2018, he invested in a Haas VF-2 SS and built a shop on his property to house it.
Thomas started Marvel Machining in 2013, running a Bridgeport EZ Trak programmable three-axis machining center in a two-car garage at night while working for another company during the day. He did this for a few years, then let it go for a bit before starting it back up in 2018. “I had a couple customers contact me and things kind of started to pick up,” he says. At this point he decided to invest in a CNC machine, a Haas VF-2 SS, and build an 1,800 square foot shop on his property in Zimmerman, Minnesota. Although he’s technically a one-man shop, he says his wife and children assist with packaging, shipping and anything else they can do to help.
“This would probably be in the top three most complex plate parts I’ve made at Marvel Machining.”
Marvel mostly does job shop work — very low quantities of functional parts for a wide variety of industries, from aerospace to medical to custom race cars. Thomas says that lately, he’s been seeing more large, complex plates like the ones he posted on Instagram. He’s been able to turn these types of parts around quickly, so his customer has been giving him more plates to machine. They’re in his wheelhouse — he worked for four years at a company that did a lot of large plates. “It’s something that I’m used to doing,” he says. But this doesn’t mean the parts are easy for him to machine. They can be time consuming and pose a number of challenges. And this part was especially challenging. “This would probably be in the top three most complex plate parts I’ve made at Marvel Machining,” he says.
Programming Challenges
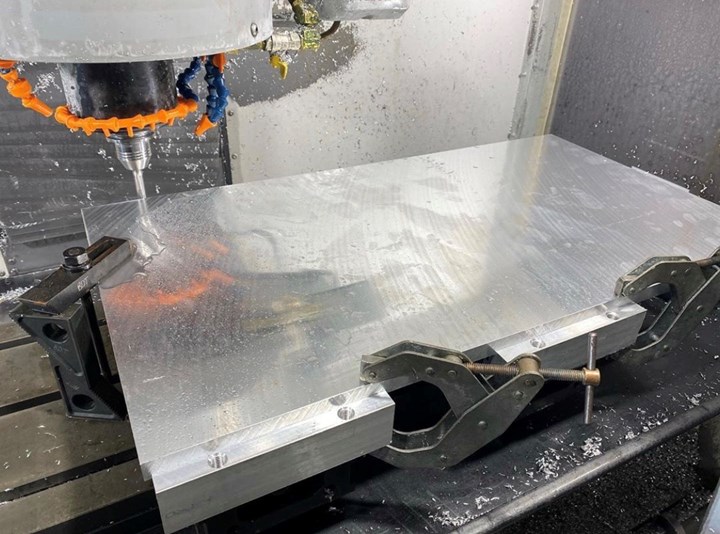
The parts started off as aluminum plates from which Thomas removed a significant amount of material to produce the final product. With parts this large, he doesn’t order extra material, so the pressure was on to get it right the first time — there was no room in his timeline to order extra material and re-machine the parts.
The first challenge when dealing with a complex part such as this is programming. Thomas counted 215 tapped holes with seven different tap sizes, along with 15 to 20 miscellaneous other holes and features that serve as mounts for a number of components on the final product, including rollers, sensors and bearings. He estimates that if he had manually programmed the part, it would have taken him three to four hours. With his CAMWorks software, he was able to complete the task in less than 45 minutes.
Perhaps the most important aid to him in CAMWorks is its automatic feature recognition. The software has the ability to identify all the holes on a part, separate them and organize them. And because CAMWorks is integrated into SolidWorks, the CAM system also automatically recognizes tapped holes in SolidWorks native files. Given the more than 200 holes in this part, automatic feature recognition saved a significant amount of time.
Thomas has also built up a database within CAMWorks that helps him quickly program complex parts. This database contains information such as chamfer sizes and countersinks for holes, as well as taps and other tools, and speeds and feed rates.
When a programmer first starts using CAMWorks, he says, it contains some predetermined settings, but they’re often basic and incomplete. For example, the program knows to assign a tool to a certain feature, but the speeds and feed rates aren’t included or aren’t optimized for the machine or setup. But as programmers use the software, they can save information about certain features, so the software automatically applies that information the next time it recognizes that feature. Thomas has been using CAMWorks for 10 years, and he has compiled a database that’s customized to the way he likes to program. For example, when he’s programming taps smaller than ¼ inch, the software knows to pull a ¼-inch spot drill, which produces the correct chamfer diameter. However, for taps larger than ¼ inch, the software automatically knows to pull a ¼" chamfer tool and give the hole a 0.015-inch chamfer before tapping the hole. In addition to tools, the database can store information on workpiece material and cutting parameters. “The majority of what I use is aluminum, so I’ve got all that figured out so I never change a speed or feed,” he explains. “And then if I change my material to stainless, I have parameters in there that’ll tell it if you’re using this end mill in stainless, run it at this speed and feed.” Even after 10 years of programming, he’s still adding new information to the database. “Every now and then, I’ll come across a part that I program a little differently,” he says, “and then you go in there and generate the tool paths and I’ll save that operation, so if it comes up again in the future, I can reference that operation.”
Machining Challenges
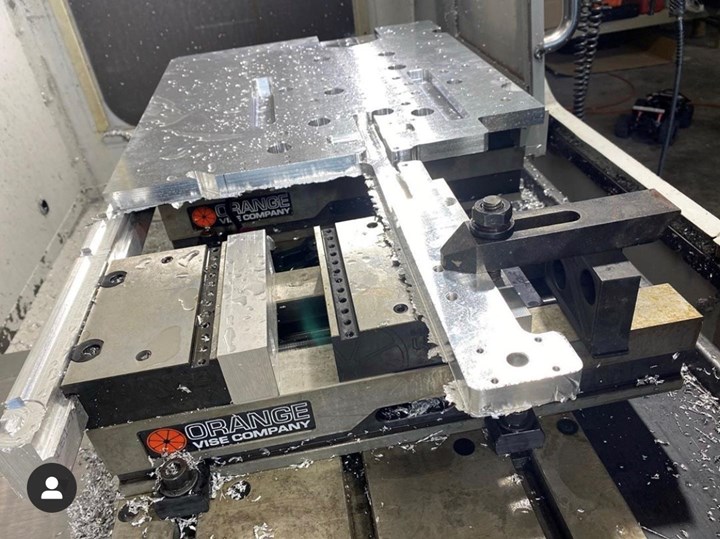
Because the plates were larger than the machine’s work envelope, Thomas had to move them around several times. His workholding system, which consists of vises from Orange Vise Company and CarveSmart dovetail jaws, enables him to efficiently move parts around.
With the part programmed, Thomas had to figure out how to machine it. He says that workholding can be a challenge for large plates like these. “A lot of people would look at it and get nervous about things moving and shifting, and not being able to clamp it right,” he says. This was complicated by the fact that the part was larger than his machine’s work envelope. The final size of the part was ¾ by 18 by 34 inches, while the Haas VMC’s work envelope is 16 by 30 inches. Because the envelope was two inches short in the Y axis and four inches short in the X axis, Thomas had to shift the part several times in the machine. He started in the left corner and machined as much as he could before shifting the part to the left and machining the rest of the right side. Then he rotated the part 180 degrees to finish the two inches the machine couldn’t reach in the Y axis and machined the holes.
Workholding that’s flexible and easy to adjust makes it easier to machine a part that needs to be shifted multiple times. Thomas uses vises from Orange Vise Company. He likes the versatility of the company’s reversible master jaws, which have integrated CarveSmart dovetail jaws that can be changed out quickly. The Orange vises also don’t have the two bolts that hold traditional jaws in place, making it easy to adjust the jaw to any length to support a part, which is especially beneficial for larger plates. “I can extend a longer vise jaw off the side of the vise and easily adjust it for clearance or clamping and not be confined to two bolts,” he explains. “I can easily shift the jaw over 0.125 inches, or any increment, or easily span jaws across multiple vises.” Users can also mount indexable grippers or SerraJaws onto the vises, which provide strong low-profile clamping.
The workholding setup includes outside jaws and center support jaws, on which the plate sits flat. The plate sits high enough above the vises that the machine doesn’t hit the workholding system when drilling holes through the plate. The vises also have holes so users can add toe clamps for extra stability.
This ability to easily adjust the vises was also helpful as he machined one of the part’s trickiest features. One side of the part has a feature that sticks out about 12" from the main body of the part and ranges in width from 0.5" to 2.5". When Thomas first started cutting out this feature, the part wasn’t clamped down well enough. He noticed some chatter, and when the end mill came around the corner, it grabbed the part and shifted it about ⅛". “Luckily, it was a roughing operation, so I still had plenty of material to do a finish pass,” he says.
Once the part was straightened out, he had to come up with a new process. He built a pin fixture that went into the end hole and clamped it down, which kept the far-right side of the part in place while he cut around the rest of it. Then he machined the feature in sections — first he cut out half of the part, then he re-adjusted the vise to clamp onto that side for support while he cut the other side.
Thomas says that the cycle time for one part was between six and eight hours and required 23 tools — which is just under his machine’s maximum of 25 tools. Because the part was so complex, he made sure to check the number of tools it required while he was quoting, a step he doesn’t usually take. “Once you get over your tool limit, you’ve kind of got to think ahead on what tools you can use and eliminate and reload,” he explains.
The parts didn’t require any CMM inspection, but Thomas did some basic inspection on the machine. “I try to do a lot of in-process inspection, especially on a plate like this,” he says. “With the time put into it, I’d hate to get to the end and inspect it to find out a hole is off or missing or not the right size, so I try to step through my tools and verify that everything is where it needs to be.” Having to scrap a part would have been especially difficult in this situation — he doesn’t order extra material for large plates like these, and his schedule didn’t allow time to order more. “I was pushing my due dates pretty close. I kind of pushed it off because I got swamped by some of the COVID stuff.” He explains that when the pandemic hit, he was swamped with work making components for N95 assembly machines. “All the parts were three to five day quick-turn parts. They needed them as fast as possible,” he says. “I was working seven days a week trying to keep up.” He also teamed up with another company, A+ Machining, to donate 75 parts to the University of Minnesota Medical School, which was developing a new rapid-deploy ventilator called the Coventor. Fortunately, despite the additional pressure from the tight timelines, Thomas was able to machine the parts correctly and get them to his customer on time.
Related Content
Workholding Fixtures Save Over 4,500 Hours of Labor Annually
All World Machinery Supply designs each fixture to minimize the number of operations, resulting in reduced handling and idle spindle time.
Read MoreShop Doubles Sales with High-Mix, Low-Volume Automation
Robots with adaptive grippers have opened entire shifts of capacity to high-mix, low-volume shop Précinov, doubling its sales.
Read MoreMachining Vektek Hydraulic Swing Clamp Bodies Using Royal Products Collet Fixtures
A study in repeatable and flexible workholding by one OEM for another.
Read MoreChuck Jaws Achieve 77% Weight Reduction Through 3D Printing
Alpha Precision Group (APG) has developed an innovative workholding design for faster spindle speeds through sinter-based additive manufacturing.
Read MoreRead Next
Aerospace Machine Shop Opts for CAM Simulation Over Dry Runs
NCSIMUL Machine software has taken Marton Precision’s G-code program verification from a 16 hour manual process to a mere two hours.
Read MoreFive-Axis Conversational Programming from a Solid Model
This CNC feature imports a 3D solid model from which operators can perform conversational-type programming even for five-sided machining applications.
Read MoreSometimes the Trickiest Part of CNC Machining Is Holding the Part
Finding a way to fixture contoured marine propellors proved to be this shop’s biggest challenge in developing an effective automated machining cell.
Read More