Discovering New Machining Technology at Mazak
A recent event at the company’s North American campus attended by more than 2,000 manufacturing professionals highlighted a wealth of new CNC machining technology.
Share



For me, it’s nice that Mazak’s North America Manufacturing headquarters is just south of Cincinnati in Florence, Kentucky. It’s a short drive. Last month, 2,000 others, many of whom hail from cities farther way, joined me in attending the company’s Discover 2019 event, which took place in part to celebrate the company’s 100th anniversary.
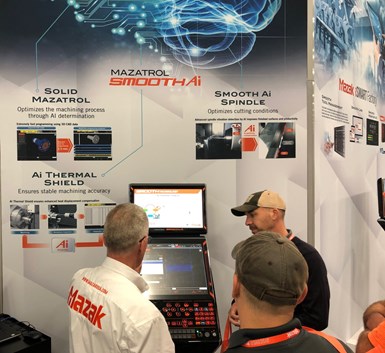
The Discover event featured the North American introduction of Mazak’s Smooth AI CNC, which offers a number of artificial intelligence and machine learning capabilities.
The five-day event spread over the first two weeks of November and featured more than 30 live machine tool demonstrations. Equipment included the company’s lines of VMCs, HMCs, five-axis machines, turning centers and turn-mills, and hybrid machines that combine machining capability with processes such as additive manufacturing and friction stir welding.
The event also offered presentations from the likes of Oak Ridge National Laboratory, University of Cincinnati, Lockheed Martin, GE Aviation, Cisco Systems and FANUC America, and enabled attendees to tour the manufacturing and machine tool assembly areas. Dan Janka, president of Mazak Corp., says the Discover event is the largest privately held manufacturing technology and education event in North America.
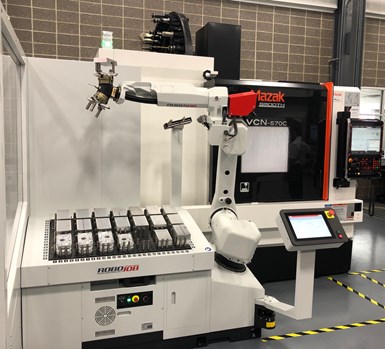
The company’s Smooth CNC technology includes functions for robot cell control with teaching assistant.
Mazak’s Smooth artificial intelligence control and software technology was prominent at the event, which featured the North American introduction of its Smooth AI CNC. This control features an enhanced graphical user interface, an optional second monitor and operation panel to support new Smooth technology solutions. These include Spindle Health Monitoring system, Smooth AI Spindle, AI Thermal Shield, Smooth CAM AI, Smooth Project Manager, Solid Mazatrol and Mazatrol Twins. It also includes functions for robot cell control and teaching assistant.
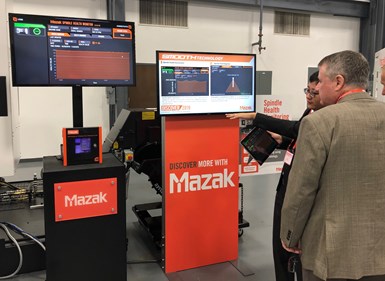
Mazak’s AI-based Spindle Health System has been developed to eliminate unexpected downtime due to damaged spindles or spindle bearings. It does this by predicting how long a spindle’s life will be so shops can better plan for downtime for repair or replacement.
Mazak also introduced its new Mixed Reality Training concept at the event, which combines virtual reality (VR) and augmented reality (AR) to reduce the risks associated with training new operators on actual machines and streamline service and maintenance.
Attendees could also see Mazak’s iSmart Factory concept in use in its manufacturing areas. A key component of this is its SmartBox, which is said to enable complete digital integration of Mazak’s manufacturing cells and systems to facilitate data sharing for process control and analytics. In fact, the company says the iSmart Factory concept has increased utilization for monitored machines in its Florence manufacturing operations by double-digit percentages. This has reduced operator overtime by 100 hours per month and brought 400 hours per month of previously outsourced work back in house. The company manufactures more than 100 machine models in nine product lines at this facility.
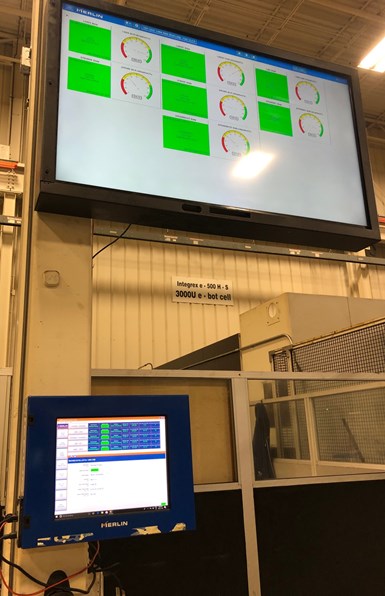
Mazak applies its own iSmart Factory concept in its Florence manufacturing facilities, which has increased utilization for monitored machines.
Mazak also announced a few additions to its Florence campus during the event. One is a new Mazatec Smart Manufacturing System that will include five of the company’s HCN-model HMCs and one Integrex turn-mill. The 235-pallet cell with raw material and finished parts stackers and loading stations is designed to accommodate a range of part and pallet sizes. It features the company’s iSmart factory concept employing the MTConnect interoperability protocol and its SmartBox IIoT machine-monitoring technology to track utilization and overall equipment effectiveness. Two people will tend the six-machine cell, which replaces an eight-machine cell and is said to offer 20% faster cycle times. It is scheduled for completion in March 2020.
Scheduled for completion in 2020, the Mazatec Smart Manufacturing System will include five of the company’s HCN-model HMCs and one Integrex turn-mill. The 235-pallet cell with raw material and finished parts stackers and loading stations is designed to accommodate a range of part and pallet sizes.
Mazak is also expanding its spindle rebuild center with a $3.5 million, 26,000-square-foot addition to its south building. The company says it will stock 2,000 rebuilt spindles there for immediate delivery and offer OEM spindle rebuild services with a three- to five-day turnaround time. It also has added a new fiber laser welder to its fabrication area that performs oscillating “wobble” welding, in which no filler material is added. This minimizes or, in some cases, eliminates manual weld grinding.
A new fiber laser welder in Mazak’s fabrication area performs a welding process in which no filler material is added to minimize or eliminate manual weld grinding.
Related Content
How this Job Shop Grew Capacity Without Expanding Footprint
This shop relies on digital solutions to grow their manufacturing business. With this approach, W.A. Pfeiffer has achieved seamless end-to-end connectivity, shorter lead times and increased throughput.
Read MoreFour Questions (& Answers) About Data-Driven Process Improvement at CNC Job Shops
How can shops can make informed decisions using data-driven feedback to improve shopfloor efficiency and profitability? And how will these technologies differ between high- and low-volume production?
Read MoreReinventing a Precision Shop With a Data-Driven Mindset
When this machine shop lost 90% of its business within three months, a reinvention was in order. Here's how it survived after quickly falling on hard times.
Read MoreCan Connecting ERP to Machine Tool Monitoring Address the Workforce Challenge?
It can if RFID tags are added. Here is how this startup sees a local Internet of Things aiding CNC machine shops.
Read MoreRead Next
Precision CNC Supercharger Rotor Machining Means More Power
By developing a more accurate machining process for mating helical rotors, this company’s superchargers can more efficiently force air into an engine for higher horsepower gains.
Read MoreUsing AI to Predict CNC Machine Spindle Issues Before They Are Issues
A machine tool builder is using artificial intelligence technology to predict when a spindle problem might occur, so shops can better prepare for and schedule necessary maintenance.
Read MoreHow Mazak's Multitasking Machine Uses Welding for Additive Manufacturing
Mazak’s VC-500A/5X AM HWD multitasking machine incorporates a “hot wire” additive manufacturing technology that applies sealing coatings or produces near-net shape part features while the workpiece has been mounted for machining.
Read More