Managing Cutting Tool Data in the Cloud
Shops are moving to data-driven manufacturing step by step. One of these steps is to access and manage cutting tool data with cloud-based, vendor-neutral databases and applications such as MachiningCloud. A review of this development shows what implementing Industry 4.0 might look like.
Share




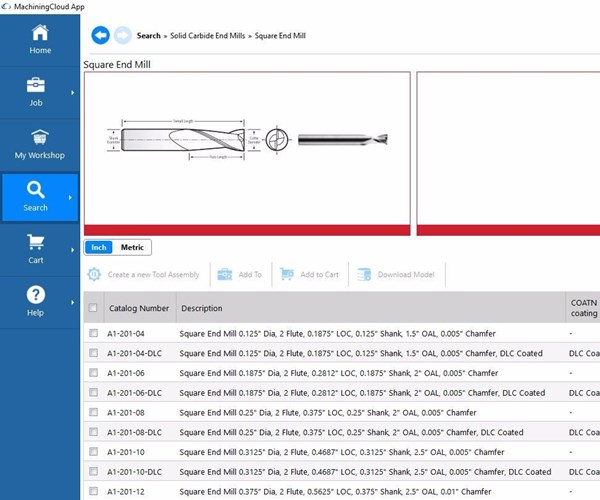
MachiningCloud forms partnerships with cutting tool manufacturers to publish data about their products. This page displays results of a search on products from RobbJack, a recent addition to manufacturers participating in this development.
Currently, there is a lot of talk about Industry 4.0, the Industrial Internet of Things (IIoT), data-driven manufacturing and digitalization. All of these terms include the underlying concept that information in a digital format can streamline, unify and enhance manufacturing operations when that data is shared across a computer network. How are machine shops and manufacturing plants implementing this concept? One example that is taking shape is MachiningCloud’s software application for searching and downloading cutting tool data.
MachiningCloud can be described as an independent provider of product data from suppliers of cutting tools and related products. The company hosts this data in the cloud, that is, on remote computer databases accessible by Internet-enabled computer networks. After creating an account, a subscriber can log on via a connected desktop or tablet to access the database and use the software functions. The hosted data is stored in standardized formats that enable it to be downloaded through the MachiningCloud app for import into CAM programming systems, CNC program verification/simulation systems, tool management and other shop software applications.
Primarily, the standards dictating the formats for digital representation of this cutting tool data are ISO 13399 (Cutting Tool Data Representation and Exchange) and GTC (Generic Tool Catalog). GTC, which is a complement to the ISO standard, provides a vendor-neutral classification of cutting tools and specifies data file structures. GTC tells vendors how to “package” their digital catalog information in a uniform way so that end-users and third-party application developers can access and present information from the vendors’ catalogs more predictably. MachiningCloud also follows MTConnect, the industry standard developed to facilitate the exchange of process information from CNC machine tools. Moreover, the company offers a service by which data from cutting tool manufacturers that is not yet compliant with ISO 13399 or GTC can be published and made available to MachiningCloud app users, who can access the data and convert it to the format required by their own applications.
An important aspect of the company’s cloud-based database is that the cutting tool product data available from the manufacturer includes 2D drawings and 3D geometric models of individual tooling items as well as cutting tool assemblies. This is in addition to the cutting speeds and feeds recommended by the manufacturer. Another important aspect of MachiningCloud is that it offers subscribers various software utilities for creating tooling lists, managing and routing jobs, checking tool pricing and availability, submitting purchase orders, and so on. These utilities enable the user to leverage digital cutting tool data to help streamline work flow throughout a shopfloor operation.
However, many subscribers initially will be attracted by the ability to access one industry-wide database of cutting tool products. For NC programmers, for example, this is a time-saving alternative to searching paper or online catalogs of cutting tool products from individual cutting tool vendors. Tooling items can be downloaded to create a tooling library and to populate the data fields required by CAM software to generate CNC tool paths. Because tooling vendors can upload frequent updates to the MachiningCloud database, programmers have greater assurance that the data is the latest and most complete.
Another benefit is the ability to download 3D geometric models and cutting parameters into CAD/CAM software for CNC machine simulation, verification and optimization. These software functions provide more accurate and reliable results when based on accurate and complete models of cutting tools and complete assemblies. Obtaining these 3D models from vendors or constructing them in-house can otherwise cause delays and inaccuracies that might diminish the value of using the simulation or verification capabilities of CNC programming systems.
Perhaps the most notable takeaway from this look at MachiningCloud as an example of Industry 4.0 and equivalent concepts is that the networked flow of coherent, pertinent data leads to better decisions about machining processes. In this case, by accessing cutting tool manufacturers’ product knowledge and information in a standardized, digital format, CNC programmers can ultimately provide toolpath files that improve machining results on the shop floor.
Related Content
Protecting Your Automation Investments
Shops need to look at their people, processes and technology to get the most of out their automation systems.
Read MoreLeveraging Data to Drive Manufacturing Innovation
Global manufacturer Fictiv is rapidly expanding its use of data and artificial intelligence to help manufacturers wade through process variables and production strategies. With the release of a new AI platform for material selection, Fictive CEO Dave Evans talks about how the company is leveraging data to unlock creative problem solving for manufacturers.
Read MoreReinventing a Precision Shop With a Data-Driven Mindset
When this machine shop lost 90% of its business within three months, a reinvention was in order. Here's how it survived after quickly falling on hard times.
Read MoreShop Quotes Smarter, Works Harder with Machine Monitoring
Temco first installed MT-LINKi to optimize quoting. Now, the software helps the shop optimize its machines — and machine purchases.
Read MoreRead Next
Registration Now Open for the Precision Machining Technology Show (PMTS) 2025
The precision machining industry’s premier event returns to Cleveland, OH, April 1-3.
Read MoreBuilding Out a Foundation for Student Machinists
Autodesk and Haas have teamed up to produce an introductory course for students that covers the basics of CAD, CAM and CNC while providing them with a portfolio part.
Read MoreSetting Up the Building Blocks for a Digital Factory
Woodward Inc. spent over a year developing an API to connect machines to its digital factory. Caron Engineering’s MiConnect has cut most of this process while also granting the shop greater access to machine information.
Read More