An Exercise in Part Production
When you put together a team of engineers, programmers and machine tool builders to develop a plan for making a part, you’ll realize the true role of imagination and creativity in the manufacturing process.
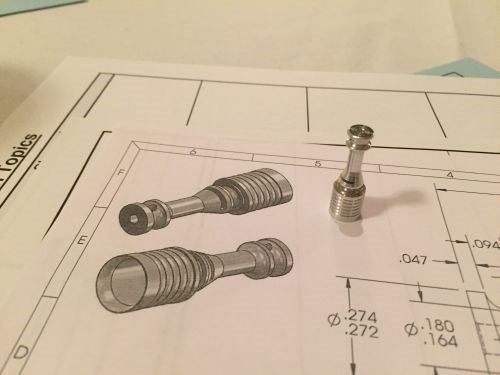
One of the most popular conference tracks at the PMPA National Technical Conference were sessions in which prints—and often part samples—with certain key parameters were provided to groups for roundtable discussions of the best way to machine the part.
When visiting a shop, I am particularly interested in the process behind determining the best way to machine a part from the prints provided by the customer. So many things must be taken into consideration—in fact, nothing can be left to chance. In order to meet the customer’s requirements, and to reach the lowest cost per part in order to win the bid, here are the top 12 considerations I’ve noted, although there are certainly more depending on the part in question:
- Best machine tool/process
- Risks/benefits of each process
- Geometry/features of the part
- How to machine with fewest setups/lowest cycle times
- The best approach to workholding/fixturing
- Best type of stock to use
- How much cross-drilling and backworking, etc., will be required?
- Best means of conducting measurement/inspection
- Chip generation (types, amounts, etc.)
- What is the purpose of the part?
- How will deburring be accomplished?
- What type of surface finish is required?
I was able to witness an especially intense example of this exercise at the recent Precision Machined Products Association (PMPA) National Technical Conference in Grand Rapids, Michigan, April 9-12 (go here for my review in Production Machining magazine). In addition to the presentations made during the three-day event—Rotary Transfer, Speeds and Feeds, CNC Programming, Additive Manufacturing, Exotic Materials, etc.—I sat in on a group discussion among operators, engineers and programmers as they worked from a blueprint to identify the optimal machines, tooling and processes for manufacturing the part in question. Three of the sessions were structured in this way.
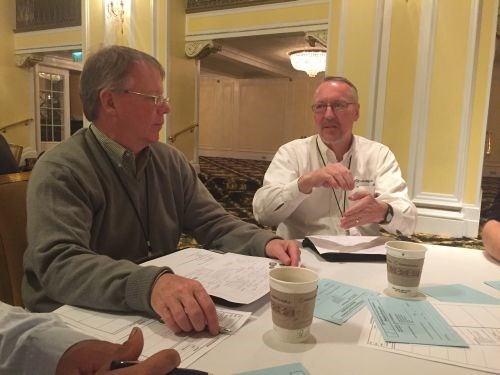
Each team, generally consisting of five to six members, discussed the plan and the related part to begin developing a machining approach. Everything from part geometry, to material, to machining methods and tooling were examined, including deburring and surface finishing.
It was fascinating to observe the thought process behind deciding how you get from a hunk of metal to a detailed, often geometrically complex finished part with the lowest cycle times, the fewest setups, and a process where each step logically leads to the next. I’ve sat down with individual shop owners (see this article from a recent issue) as they’ve explained the logic behind their decisions, but to witness a group discussion in which everyone discussed their personal experiences—both victories and failures—and the tricks they’ve learned along the way for making deburring part of a machining step, or developing fixturing that made setups easier to accomplish gave me new respect for all the thought and planning that goes into machining parts from raw materials.
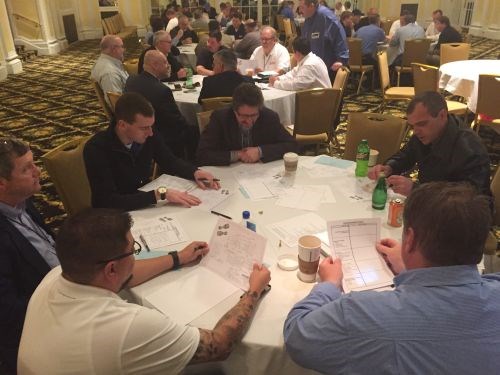
The audience was a mix of engineers, programmers and machine tool builders. Their different perspectives and experiences made for lively conversations.
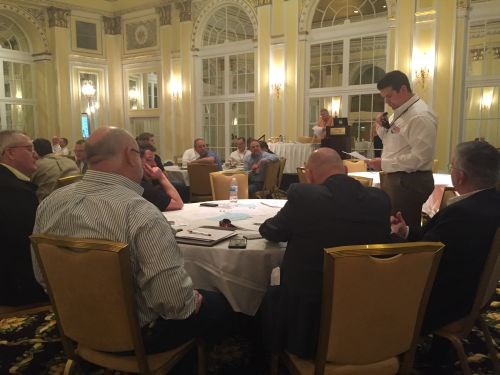
At the conclusion of the discussion period, a representative of each table addressed the hall, describing the group’s machining path, including the reasoning behind the decisions they’d made. Once their presentations had been made a member of the company that provided the part and print—in this case, Don Corwin of Buell Automatics—revealed the backstory, including the part’s history, intended usage, and current manufacturing status.
Read Next
A History of Precision: The Invention and Evolution of Swiss-Style Machining
In the late 1800s, a new technology — Swiss-type machines — emerged to serve Switzerland’s growing watchmaking industry. Today, Swiss-machined parts are ubiquitous, and there’s a good reason for that: No other machining technology can produce tiny, complex components more efficiently or at higher quality.
Read MoreIMTS Elevate Workshop: Make Your Shop a Top Shop
This ½-day program offers attendees insight into the results from this year's Modern Machine Shop Top Shops annual benchmarking survey.
Read MoreThe Automation Event for CNC Machine Shops
Get sensible, real-world automation solutions during this half-day workshop co-located with IMTS 2024.
Read More