Wireless Couplers Work Wonders for Workholding
Possibilities range from individual control of chuck jaws and tombstone fixtures to more reliable robots.
Share




What if the same lathe chuck could center round, square or irregularly shaped stock without changing jaws? What if HMC tombstone clamps could be powered (and monitored) individually, without the complexity of hydraulic or pneumatic connections?
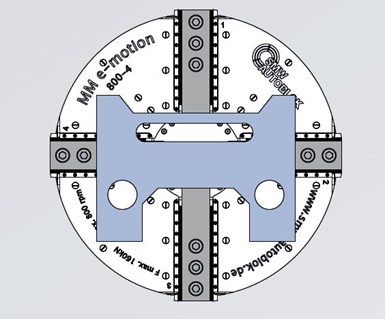
Different wall thicknesses, special geometrical forms and both ID and OD clamping are all ideal for chucks with individual jaw control. Images courtesy of SMW-Autoblok.
These are among the primary selling points of new chucks and tombstones from SMW-Electronics, a recently established business unit of workholding specialist SMW-Autoblok. This workholding is defined by its use of inductive couplers: wireless power and data linkages that provide control at the level of the individual chuck jaw or clamping device. “I can take a standard jaw set and cover a huge spectrum of parts that, in the past, would require all these special components to hold,” says Larry Robbins, president of SMW Autoblok’s U.S. division.
Torque, temperature, position and various other metrics can also be tracked via these connections, he adds. The technology also holds promise beyond machine tool workholding. Fully sealed against contaminants, inductive couplers could replace cables, plug connectors or other physical links in a virtually any automation system. “Where it’s really going to be industry-changing is robot end effectors,” Robbins says, explaining that eliminating wires removes a potential failure point in the connection from arm to gripper (or other tooling).
In any application, the linkages look essentially the same: Data and power transmit across a slight air gap (<=2.5 mm) between two parallel, disc-like couplers, one in the stationary element (the machine table or robot arm) and one in the moving element (the rotating chuck or gripper). The means of this transmission, electromagnetic induction, is the same essential principle underlying wireless charging devices, toothbrushes and other established products.
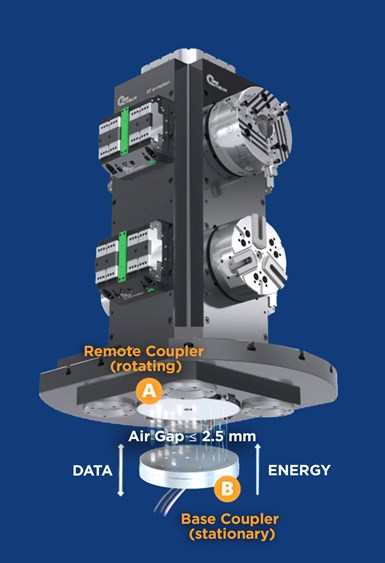
However, making this promising technology practical for masses of CNC machine shops has required more than just SMW-Autoblok’s long history in metal-cutting applications, Robbins says. To interface with the various CNCs on the market, the company has been collaborating closely with Doosan, Makino, Mazak and DMG Mori, among other machine tool builders. Based on progress so far, Robbins says he expects essentially “plug-and-play” integration to be available for some of the newest machine tools by the end of this year.
Whatever the timeline for widespread adoption, the potential is undeniably vast, beginning with the design freedom to pair each moving clamp or chuck jaw with its own electromotor. On the shop floor, the chucks (the company’s “MM e-Motion” brand) provide freedom to accommodate a variety of rectangular, asymmetrical or otherwise non-standard workpiece shapes on a lathe or turn-mill without so much as jaw change, let alone a specialized gripping profile or the use of shims or other auxiliary devices. Per-jaw stroke and force adjustments — which can be made without unclamping — help simplify machining of parts with different wall thicknesses, or those that are easily deformed.
Add a measuring sensor, and the chucks can become essentially self-centering, Robbins says. “Let’s say within a batch of 100,000 forgings, you’ve got seven millimeters of variation. As long as that’s within the physical limits of the chuck, you can adjust each part to bring it on-center individually. You can take a batch of parts that would have been rejected, and make them all good parts.”
Another significant benefit is the lack of hydraulic or pneumatic connections. This characteristic makes inductive couplers particularly useful for tombstone HMC fixturing (“RT e-Motion”). In addition to simplifying physical connection points, inductive coupling saves energy, Robbins says. Air compressors can be “expensive to run” and that hydraulic fluid is something a manufacturer will “own for life.” Allowing the fixture stations themselves to pull power also compounds the savings because energy is never wasted on unmoving clamps.
Whether with chucks or tombstones, capability to transmit data as well as power can enable programmers to clamp with an eye toward process improvement. As a hypothetical example, Robbins cites an effort to find a “perfect sweet spot” for clamping a prototype transmission gear. “In the past, you record all these little parameters on a piece of paper or in your CNC control and hope the next batch is just as good,” he explains. Instead, a probe measurement might reveal the need for an offset adjustment to maintain accuracy or repeatability, which might be initiated automatically by the CNC.
As for questions about the safety of this wireless technology in industrial settings, Robbins says redundant systems make these electrically-powered chucks and tombstones as reliable as their pneumatic, hydraulic and manually operated counterparts. “If I lose electrical power, what happens? Nothing,” he says. “If one (interface) fails, another takes over.”
Related Content
Reinventing a Precision Shop With a Data-Driven Mindset
When this machine shop lost 90% of its business within three months, a reinvention was in order. Here's how it survived after quickly falling on hard times.
Read More5 Stages of a Closed-Loop CNC Machining Cell
Controlling variability in a closed-loop manufacturing process requires inspection data collected before, during and immediately after machining — and a means to act on that data in real time. Here’s one system that accomplishes this.
Read MoreLeveraging Data to Drive Manufacturing Innovation
Global manufacturer Fictiv is rapidly expanding its use of data and artificial intelligence to help manufacturers wade through process variables and production strategies. With the release of a new AI platform for material selection, Fictive CEO Dave Evans talks about how the company is leveraging data to unlock creative problem solving for manufacturers.
Read MoreMachine Monitoring Boosts Aerospace Manufacturer's Utilization
Once it had a bird’s eye view of various data points across its shops, this aerospace manufacturer raised its utilization by 27% in nine months.
Read MoreRead Next
Is Wireless Data Collection a Cultural Choice?
Untethered digital inspection tools are easier to justify for those who are willing to hold themselves accountable and improve for improvement’s sake.
Read MoreWires Make the World Wireless
Leveraging 5G requires infrastructure grounded in physical wiring and thinking grounded in practical application.
Read MoreBuilding Out a Foundation for Student Machinists
Autodesk and Haas have teamed up to produce an introductory course for students that covers the basics of CAD, CAM and CNC while providing them with a portfolio part.
Read More