Robotic Cell Improves Quote, Wins Shop an Aerospace Job
By adding a FANUC-controlled automation cell, Kemco Aerospace Manufacturing improved the cost-competitiveness of its quote and won a major aerospace job.
Share


Takumi USA
Featured Content
View More




Hwacheon Machinery America, Inc.
Featured Content
View More
.png;maxWidth=45)
DMG MORI - Cincinnati
Featured Content
View More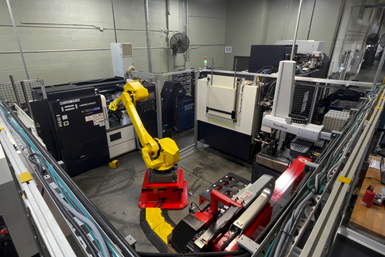
Bidding on a job against an incumbent manufacturer meant Kemco needed to find a technological edge — in this case, automation where the competition used a hand-load system. Photo Credit: FANUC America
Kemco Aerospace Manufacturing, true to its name, specializes in metallic structures and assemblies for the aerospace industry. Its machining equipment largely consists of large- and small-bed five-axis machines, but the company also has capabilities for waterjet, assembly and welding.
Recently, Kemco had the opportunity to bid on a job to annually manufacture 30,000 units of a single component. The company was competing with an incumbent manufacturer, and knew its quote needed to be as competitive as possible to win the job. Kemco decided its best path was investing in automation.
Automating for Success
“We were pretty confident the existing opportunity was being fulfilled through a hand-load system where you had a lot of bodies moving parts between machine tools,” says Dan Ladenberger, president and owner of Kemco Aerospace Manufacturing. “We knew that in order to meet the quality and the efficiency requirements necessary for delivering a successful quote, we needed to bring automation to the forefront.”
“One thing that was really helpful for us when we were integrating is that the FANUC controls in the machining centers have a seamless handshake when it comes to integrating to the FANUC robot,” Prior says.
Kemco brought in Industrial Tool, Inc. (ITI), a FANUC America-Authorized System Integrator (ASI) with over 30 years of experience automating large machining lines using FANUC robotics. ITI worked with Kemco to determine the scope of the automation solution, including the cycle times necessary to produce the required number of finished parts over an eight-hour shift.
“Kemco wanted a truly unattended automated robotic system that not only machined the parts, but also measured every part,” says Paul Prior, sales engineer for ITI. “No part could be put on the outfeed conveyor that was actually a bad part. The robot would take that part and put it on a quarantine rack for human inspection.”
Creating the Cell
As part of the automated robotic cell, machine tool distributor Maruka USA brought in three Hwacheon machines. The lathe and two mills were equipped with FANUC 0i-F controls, which integrated well into Kemco’s already FANUC-heavy operations.
“Because of the nature of the material being machined, we chose to use two Hwacheon 1050B vertical machining centers with both box way and gear-headed spindles because of their rigidity and stability in cut,” says Vern Winn, technical sales engineer for Maruka USA. “For the fine boring and threading work, we chose to use a Hwacheon Hi-Tech 230B because of its ability to maintain accuracy and hold tolerance through unattended runtime.”
The final cell concept has an infeed conveyor and an outfeed conveyor. A FANUC M-710iC robot uses a 3D vision system to pick up the to-be-machined part on the infeed conveyor and place it in the first vertical three-axis mill.
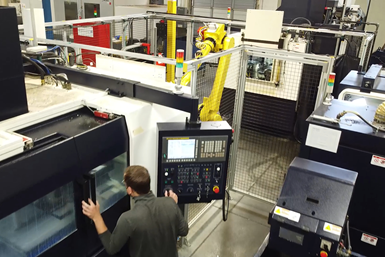
The automation cell still requires operators to check in on parts from time to time, especially if a tool breaks or wears down during machining. Photo Credit: FANUC America
“We use 3D vision over the infeed strictly for orientating the part because the part is round and has no clocking features other than a convex shape,” says Steve Carstens, mechanical design engineer for ITI.
Because there is no radial clocking, the robot is required to locate in the machine fixture, which has no locating features. To solve this problem, the 3D vision maps the part’s curve and guides the robot to pick up the part.
“We really rely upon the accuracy of the FANUC robot to pick that part up,” Prior says. “Without the robot being accurate enough to position that part within a half of a degree repeatedly day in and day out, we would not be able to accurately make a part.”
The robot removes the part when finished and places it in the second vertical machining center. After the second machining step, the robot then moves the part to a lathe, which performs critical threading and deburring.
Successful Connection
“One thing that was really helpful for us when we were integrating is that the FANUC controls in the machining centers have a seamless handshake when it comes to integrating the FANUC robot,” Prior says. “The same signal says ‘I’m ready to have a part removed,’ and ‘I’m ready to have a part loaded’ in the machines. That FANUC signal, that FANUC handshake, makes it easier for us as an integrator to connect all the dots.”
After manufacturing is completed, the robot runs the part through an automatic blow-off station and a CMM, which collects quality data to ensure the part is to spec. If not, the part is automatically rejected. Also, if a tool breaks or wears down during the machining, the part is quarantined, which allows the automated cell to run unattended for eight-hour shifts at a time, 24-hours a day.
“By utilizing FANUC’s Tool Life Management,” Winn says, “we are able to exchange a fresh tool without interrupting the cycle, which is important to keep cell uptime.”
This project enabled Kemco to offer a cost-competitive quote while leaving itself an adequate margin for consistently producing the high-quality parts. Ultimately, it won the contract.
“We would not have been able to win this work, in our belief, without the efficiencies and the quality environment that this cell brought to the table,” Ladenberger says.
Related Content
DN Solutions Responds to Labor Shortages, Reshoring, the Automotive Industry and More
At its first in-person DIMF since 2019, DN Solutions showcased a range of new technologies, from automation to machine tools to software. President WJ Kim explains how these products are responses to changes within the company and the manufacturing industry as a whole.
Read MoreFinding the Right Tools for a Turning Shop
Xcelicut is a startup shop that has grown thanks to the right machines, cutting tools, grants and other resources.
Read MoreAddressing the Manufacturing Labor Shortage Needs to Start Here
Student-run businesses focused on technical training for the trades are taking root across the U.S. Can we — should we — leverage their regional successes into a nationwide platform?
Read MoreHow to Pass the Job Interview as an Employer
Job interviews are a two-way street. Follow these tips to make a good impression on your potential future workforce.
Read MoreRead Next
CNC Shop Employees Benefit from Robotic Automation
To better use machine operators’ time and improve overall productivity, Dimension Machine Co., invested in two Okuma Genos lathes with a FANUC M-710iC/50 robot from Gosiger Automation.
Read MoreRobots Get a Ride with CNC Machine-tending AGVs
Mobile machine tenders prove that “automation-ready” is a state of mind.
Read MoreModern Machine Shops Must Invest in Technology and Training
Investing in new technology, training and automation is a necessity for keeping up with the changing nature of manufacturing, according to Tony Staub, founder of Staub Precision Machine Inc.
Read More