Share



Metal 3D printing has had years of success in the moldmaking sector, where new design possibilities for mold tools have supported better performance in the injection molding process. Two main processes, laser powder bed fusion (LPBF) and directed energy deposition (DED), have proven useful for integrating together what would otherwise be separate pieces of tooling; for producing more complex mold cores and cavities; and for the incorporation of conformal cooling channels that precisely mirror the tool’s geometry for more efficient cooling.
However, these 3D printing processes also have drawbacks when applied to moldmaking. While they are usually faster to obtain a tool machined from scratch, LPBF or DED is almost always more expensive than a conventional tool. And once printed, the tooling will still need some amount of machining to fully finish it. Metal 3D printed molds are justified not by the cost savings in producing them, but by what comes later: reduced injection molding cycle times, better part quality, perhaps reduced maintenance over the tool’s life. If these benefits are enough, the upfront investment in the mold tooling makes sense.
But is there a scenario where 3D printed metal molds don’t need to be highly complex, and can compete instead on time and cost? A new metal 3D printing process called TrueShape aims to make this possible. Created by startup company Mantle, TrueShape is designed to make metal 3D printed mold tooling not only more affordable than it has been in the past, but also cost-competitive with conventional processes like machining and EDM. The key? Limit the postprocessing typically needed on metal 3D printed parts through “preprocessing.”
Reducing the Time from Print to Part
The 3D printing processes typically applied to mold tooling utilize loose metal powder that is either sintered in a bed or applied through a nozzle. The powdered feedstock poses a number of personnel and environmental risks, but also results in the rough surface finish that necessitates further processing before the tool can be used to form plastic parts in an injection molding press.
Instead of a loose powder, the feedstock for TrueShape is a paste consisting of powdered metal held together with a small amount of liquid. Rather than fusing that material in process, TrueShape builds the the mold (or other metal component) by extruding the paste to form a “green” or “brown” part which is then sintered to its final form in a separate step. And, unlike most other metal 3D printing processes, the resulting parts typically require no further machining or finishing once they emerge from the sintering furnace. The full process including 3D printing and sintering can deliver a final part in about two days.
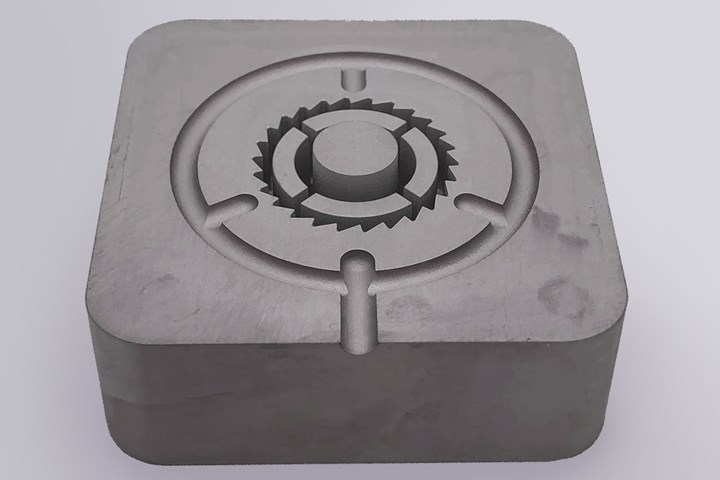
This mold for a medical device manufacturer was made in a week with the TrueShape process, and required no surface finishing before being used for production injection molding. Photo Credit: Mantle
The trick to avoiding postprocessing after the print is the ability to preprocess the part during the build. Mantle’s 3D printer incorporates a high-speed milling spindle along with the extrusion head to facilitate this. Milling can take place after every layer, at the end of the build or only on certain features. A drying step to remove excess liquid on every layer means that there is very little binder left in the material when this shaping happens, which results in limited and predictable shrinkage during sintering and preserves the benefits of milling.
Molds and More
Mantle emerged from stealth mode in February 2021, but its technology is already being used by moldmakers and OEMs. TrueShape has been applied to produce mold tooling for medical prototypes, dishwasher parts and more, often delivering tooling that requires no additional machining according to the company.
But mold tooling likely won’t be the only application for this technique. While TrueShape has been optimized for moldmaking first, the process could also build end-use metal parts including spare components or production runs.
See additional tool photos and learn learn how this method could deliver on AM’s promise for mold tooling and other metal parts at AdditiveManufacturing.Media.
Related Content
Cimatron's Updated CAD/CAM Software Streamlines Mold Design
Eastec 2023: Cimatron V16 includes a clean new user interface and increased automation for faster mold design, electrode creation and NC programming.
Read MoreLyndex-Nikken Collets Enable Accurate Small-Diameter Cutting
The MMC Mini-Mini collet chuck is well suited for high-speed machining applications where clearance is needed, such as die mold, aerospace and medical parts.
Read MoreHow to Achieve Unmatched Accuracy in Very Large Workpieces
Dynamic Tool Corp. purchases two bridge-style double-column CNCs to increase the cutting envelope and maintain 5-micron cutting accuracy in the long term.
Read MoreFor This Machine Shop, Licensing Is the Answer to the Inventor’s Dilemma
Machine shops are natural inventors, but not necessarily suited to supporting and marketing a product. This Minnesota shop with an invention related to micromolding will share it through licensing.
Read MoreRead Next
How Do Binder Jetting and Multi-Laser Powder Bed Fusion Match Up?
Both metal 3D printing processes are ready for production, but which wins out for speed and cost? Research from The Barnes Global Advisors offers a case study.
Read MoreUse Your Machinists to Make Dies
By systemizing die making into repeatable steps, Dies Plus, a division of Otto Engineering, is using its machinists to effectively make dies. This solution relies on a paperless color-coding system to convey the tolerances machinists need to hit in order for tool and die makers to do the final fitting.
Read MoreCan This Metal 3D Printing System Make Production Additive Manufacturing Common in Machine Shops?
A new metal AM system for batches of end-use parts was designed to permit productivity and machine pricing comparable to a CNC machine tool.
Read More