Share



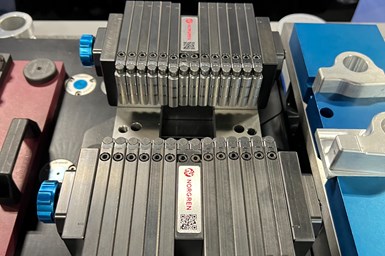
Jergens’ quick-change and modular workholding devices simplify setup procedures to improve uptime and productivity, and the company has even started manufacturing tombstones to help with lights-out automation. In the other direction, a recent collaboration with Norgren uses a Jergens vise and Norgren’s Adaptix fingers for simple, quick, modular workholding.
Not far from a sign that reads “No Livestock in Center Aisle,” visitors to Eastec 2023 could find advanced robotics, intuitive control panels, powerful vision systems and other new and impressive machining technology from over 450 exhibitors in the Eastern States Exhibition area in West Springfield, Massachusetts. Rather than a focus on big-ticket machine tools, this year’s Eastec exhibitors (and 9,500-person crowd) seemed more interested in the tools to manage perennial staffing shortages, as well as technologies to better leverage operators and machinists currently on the shop floor. Solutions took many forms — and attendees took notice.
Cutting Through Process Complexity
Eric Ostini, GF Machining’s head of Business Development, is well aware of the staffing issues plaguing the US machining industry. As a representative of a company with a thriving Swiss headquarters, he is also aware that newcomers to the industry in Europe typically have more machining education. This goes double for EDM machines, which Ostini says rarely feature in tech schools. To overcome this knowledge gap, Ostini says GF introduced this technology to Eastec Student Summit participants — and that it is debuting a new control for the US market.
The control on the company’s upcoming Cut F EDMs is two years old, but Eastec was one of the first times the company has been able to show it off to a wide U.S. audience. The new control includes features that automatically adjust spark power and frequency to maximize wire life and productivity. This automation simplifies the operator’s role, decreases training times and freeing up the operator to focus on other vital tasks as part of running the connected machine. Ostini also says GF is developing ways to make maintenance more regular and repetitive (and thus, easier to work with), as well as meet ever tightening training times: While in years past the company preferred five-day training programs, Ostini says that customers now require three-day or even one-day training periods to limit downtime.
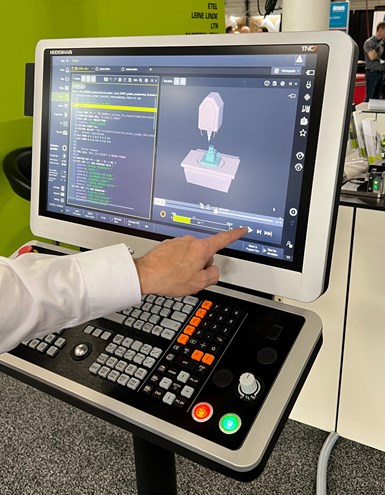
Heidenhain’s Linux-based TNC 7 controls feature both traditional and graphical programming. Michael Ammon, TNC applications engineer at Heidenhain, says this combination makes it both familiar to long-time machinists and intuitive for newcomers to machining.
Heidenhain is also positioning its controls as an intuitive method for performing increasingly complicated jobs on the shop floor. The TNC 7 control sports a 20-inch touchscreen as well as a more traditional keyboard, and when selecting a line of code, a visual representation appears onscreen to demonstrate the action that code performs. The software also includes a “sketch” module that enables users to graphically design a contouring operation and export it into Klartext programs. Onboard simulation software uses digital twins of the machine and part while also including dynamic collision monitoring to ensure programs are free of errors leading to crashes.
Heidenhain also promoted its MillPWR DRO at the show. This device adds NC capability to bed and knee mills, with representatives at the booth noting its suitability for educational use — and for the odd R&D application.
Fanuc’s CRX robots can “flow” to locate parts in workholding devices. Without this ability, the part would drop from the workholding device with even the slightest misalignment.
For production applications, FANUC demonstrated the most recent version of icon-based programming for its CRX robots. This form of programming is an easier-to-use alternative to traditional programming, with additional functions regularly added as discrete icons. Force modules enable a “push to escape” function for both safety and process security in the event of unexpected obstacles. The robot can also make minor adjustments to fit parts within chucks, and uses IR-guided vision and a dot matrix on the outside of machines to locate the robot.
Vision and Touch
Beyond robotics, vision systems made up a large share of notable metrology offerings at EASTEC — though technology providers also showed off ways in which other types of metrology devices assist their users.
Starrett displayed multi-sensor vision systems as well as traditional and digital versions of its horizontal comparator. CW Moran, Starrett metrology marketing manager, mentions that the digital comparator received much attention at the show, as it is a vision metrology system that functions like an optical comparator, enabling long-time users to take a step into vision technology. The company is also experiencing a surge in demand for its special precision gages. Andrew Morin, manager of Starrett’s special gages division and material test division, says a dedicated engineering team at Starrett designs and manufactures these gages to customer requirements, making them compatible with everything “from potato chips to rocket ships.” The special gages achieve a constant spring rate, ensuring consistent gaging measurements between operators.
Mitutoyo’s Crysto CMM can perform 3D scanning at 1.7-micron accuracy. The CMM’s combination of speed and accuracy is partly due to its construction, with a milled granite Y-axis and air bearings directly attached to the machine.
Mitutoyo is also advancing its technology in multiple directions, offering both advanced vision systems and CMMs. The company’s Quick Vision systems use robotic microscopes with up to 25x lenses, and even the entry-level system has a repeatability of 3 microns (the high-end system boasts sub-micron repeatability). A new “Apex” model uses a strobe light and, unlike other vision systems, can take measurements on most parts without stopping. Company representatives position the Quick Vision systems as especially suitable for measuring sutures and medical parts, while also noting their usefulness for gears, circuit boards, clean room parts and other no-touch parts. Like the company’s Crysto CMM systems, these machines can connect to a wide variety of analysis software to streamline the inspection process.
While the Quick Vision systems are faster than CMMs, the Crysto systems use a 3D scanning path to operate faster than CMMs using point-to-point scanning. MICAT planner software can also take already defined features in a 3D model and import them into the inspection plan, cutting programming time and streamlining inspection personnel’s duties. Beyond cutting programming and operation times, Crysto systems also use the same scales as Mitutoyo’s calipers, eliminating the need for a homing process.
Rego-Fix’s press-fit system may have been the company’s biggest draw at the show, but its ReCool system, which can retrofit spindles to work with through-coolant, also provides a large increase in tool life and process security increases.
Making Monitoring Matter
Companies releasing devices under the Industry 4.0 umbrella tend to speak of how they improve productivity and maximize worker productivity. Richard Hefner, president of FactoryWiz, says that it is true most machine monitoring technology leads to an initial boost in productivity. He then compares this boost to the Hawthorne effect: Because machinists know they are being monitored, they work harder, whether the software helps or not. The real test on whether these early boons taper off comes from how managers use this information. In bad cases, managers lay the blame for unexpected day-to-day downtime with operators and machinists rather than processes, increasing stress among shop floor personnel and failing to find the root cause of production setbacks.
Hefner positions FactoryWiz’s upcoming release as a potential antidote to these troubles with machine monitoring. The software includes individualized dashboards for each user depending on which machines they use, and information can be shared across departments to improve whole shop floor visibility. A Sticky Note feature takes setup and handoff information for different shifts and collates it for future reference (and data traceability), while a new Swarm feature enables operators to ask for help from peers — with the software tracking which operators and machinists come to the aid of their coworkers. When combined with data views that favor whole-department OEE to individual-machine OEE, Hefner believes the Swarm feature will nudge employees toward a more collaborative structure, increasing morale, buy-in to machine monitoring and the end-goal of the technologies across Eastec: productivity.
Related Content
6 Machine Shop Essentials to Stay Competitive
If you want to streamline production and be competitive in the industry, you will need far more than a standard three-axis CNC mill or two-axis CNC lathe and a few measuring tools.
Read MoreHelp Operators Understand Sizing Adjustments
Even when CNCs are equipped with automatic post-process gaging systems, there are always a few important adjustments that must be done manually. Don’t take operators understanding these adjustments for granted.
Read MoreBallbar Testing Benefits Low-Volume Manufacturing
Thanks to ballbar testing with a Renishaw QC20-W, the Autodesk Technology Centers now have more confidence in their machine tools.
Read MoreOrthopedic Event Discusses Manufacturing Strategies
At the seminar, representatives from multiple companies discussed strategies for making orthopedic devices accurately and efficiently.
Read MoreRead Next
Automation and Flexibility Counter Inflation at BI-MU 2022
Automation headlined BI-MU 2022, while flexibility underscored exhibitors’ products. These twin benefits may be shops’ greatest assets against inflation.
Read MoreDigital Solutions Dominate TIMTOS
At TIMTOS, many OEMs highlighted solutions designed to overcome challenges that may sound familiar to U.S. manufacturers.
Read MoreIMTS Takeaways From the Modern Machine Shop Editorial Team
The first in-person IMTS in four years left the MMS editorial staff with a lot to digest. Here are a few of our takeaways from the show floor.
Read More