Share




This article originally appeared on our sister site, Additive Manufacturing Media. Check it out for more AM content.
Here is a truism that manufacturers working close to additive manufacturing understand: The best opportunities for AM involve parts designed with additive in mind. But what if this principle extends farther than part design? To make a product additively is not just to replace some conventional operation with 3D printing. In the way it combines material creation and part creation in one, and in the way it consolidates assemblies into single intricate components, additive manufacturing represents a new way to produce and a new way to organize production. The best opportunities for AM therefore likely involve facilities — even enterprises — that were also designed with additive in mind.
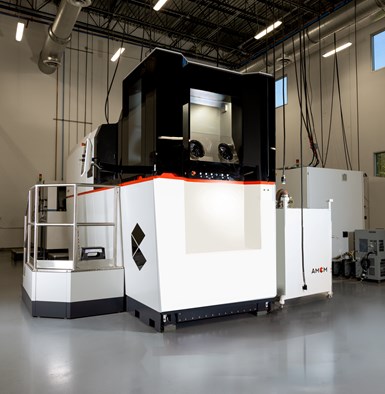
Sintavia expects to employ larger and larger machines. This recently installed four-laser AMCM M 4K from EOS 3D prints parts up to 1 meter high. (The machine at Sintavia was actually EOS's 1,000th machine installed in North America.) Photo: Sintavia.
Sintavia, the Florida-based additive manufacturer serving the aerospace sector, illustrates this point. In 2019, the company completed construction on a Fort Lauderdale-area facility focused on additive production. The 55,000-square-foot site in Hollywood, Florida, currently has 25 industrial 3D printers for metal parts. In fact, the focus is even more specific: Launched from an aircraft engine MRO business in 2015, Sintavia performs laser and electron beam powder bed fusion (PBF) of aircraft and rocket engine components. PBF for aerospace is the company’s sole aim. Brian Neff is the company’s CEO and founder, and he says the fact that the company had no legacy in conventional aerospace part production has been an aid to its success.
“It’s not like we had to burn our boats in traditional manufacturing to commit to additive and make it work,” he says. “We never had those boats to begin with.”
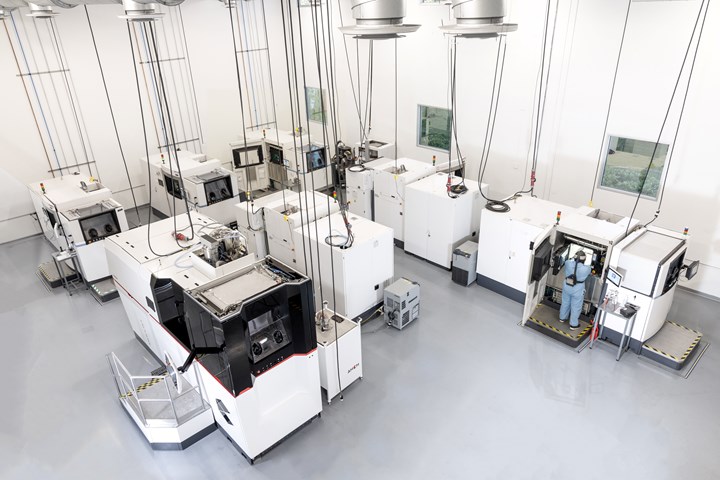
Production operations are quiet, clean and calm, with minimal direct human involvement. Here is the additive production area that includes the new large-format machine. Photo: Sintavia.
I recently visited the new Hollywood site. I had planned to visit early in 2020, but the onset of covid derailed that trip. To an extent, I am glad. The year delay meant I saw the facility more broken-in and more full of equipment, its work well underway. I have toured many production facilities; in comparing what I have come to expect in production facilities to this one built for AM, here are the distinctions I see. That is, here are some of the ways a facility conceived for AM looks and functions differently:
1. The Quiet
Every portion of the Hollywood facility, save for one, is quiet, clean and calm — little different from the environment or noise level in an office area. The one exception is telling, because it provides the comparison: The CNC machine shop at Sintavia still offers the environment of an advanced CNC machine shop.
I stress “advanced” because machining facilities have become quieter, cleaner and more orderly. Sintavia’s shop fits this category. But still: There is coolant vapor in the air. There are compressors, motors and metal cutting making noise. We in manufacturing accept, and we are accustomed to the fact, that even modern manufacturing comes with a din. But throughout the Sintavia facility’s powder bed fusion operations for metal AM, there is little to no din.
2. Production Oversight Rather Than Direct Production Staffing
The Florida facility is organized for unattended production. The 3D printing build for any given production part is a long cycle — more than a day in duration, often more than a week. That build generally consolidates what might have been many separate part-making, transport and assembly steps if the comparable part or subassembly had been made conventionally. As a result, additive manufacturing is high-value-adding production with little direct human involvement throughout the course of that value being added. Look into any of the rooms in the Sintavia facility where PBF machines run, and while parts are being printed, no employees are apt to be in view.
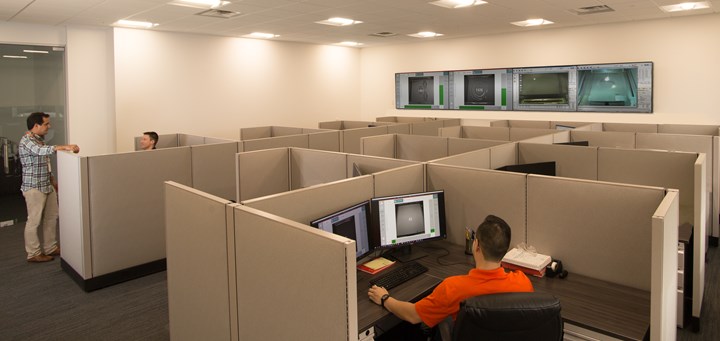
Displays in the engineering department provide real-time status information for production builds that run almost entirely unattended. Photo: Sintavia.
Information about production is instead delivered to where the employees are. The facility runs on Siemens’ suite of ERP systems, including Teamcenter and Opcenter, and it uses these systems to provide different data feeds to displays throughout the site. The most concentrated example of this is in the engineering department, where a bank of monitors like a mission control array provides real-time status information for various production jobs.
3. Building Design With the Future in Mind
Technology in additive manufacturing is changing fast and, as Neff notes, it will keep changing. The facility design has to anticipate that the machines used in just a few years might differ from the machines used today.
The most meaningful technology change he expects is the advance to larger PBF machines. This has to happen, he says. Machines with even larger bed sizes and work heights will expand the opportunities for AM into even larger structures consolidating even more assembly work into one piece, while also increasing productivity by permitting more smaller pieces in a single build. To accommodate the expectation that machines in the future will be bigger, the facility was designed with more floorspace and a much wider central hallway (for getting machines in and out) than what is needed for the dimensions of equipment today.
4. Powder as Part of the Process
Realizing efficient day-to-day AM production means (in the case of laser and electron beam PBF) developing effective daily practices for handling powder and assuring powder quality. Sintavia’s process in large part draws on simplicity and common sense. Separate rooms for separate metals (aluminum alloy, nickel alloys) assure there is no cross-contamination between very different material types. Powder cannisters the company designed itself and has custom-made allow employees to identify the contents of a cannister at a glance, according to the size and shape of the container.
For in-process assurance of powder quality, tiny white containers like pill bottles are used to carry powder samples from builds in work to an on-site QA lab. Where powder analysis reveals a departure from the required specification for a given part’s powder quality, a nonconformance team issues an “all stop” for the job until the discrepancy can be diagnosed and addressed.
5. Machining as the Heart of the Process
In additive manufacturing for components as precise and complex as aircraft engine parts, the 3D printing alone does not come close to realizing the part’s ultimate value. Attaining completed parts ready for delivery to the customer is the work of postprocessing, particularly machining. The machine shop in Sintavia’s facility occupies a relatively small percentage of floorspace, but Neff says the importance of postprocessing capability would be difficult to overstate. Additive alone can’t realize the tolerances needed. Metalcutting requirements on any given part are slight, but crucial — and they are also challenging. CNC machine tools in the shop include four-axis and five-axis machining centers, as well as a multitasking turn-mill lathe. In contrast to the unattended nature of 3D printing through much of the rest of the facility, the work in this shop relies on skilled machinists able to program, set up and fixture machining cycles for the geometrically complex forms. Sintavia’s advance will necessitate machining capacity increasing, Neff says.
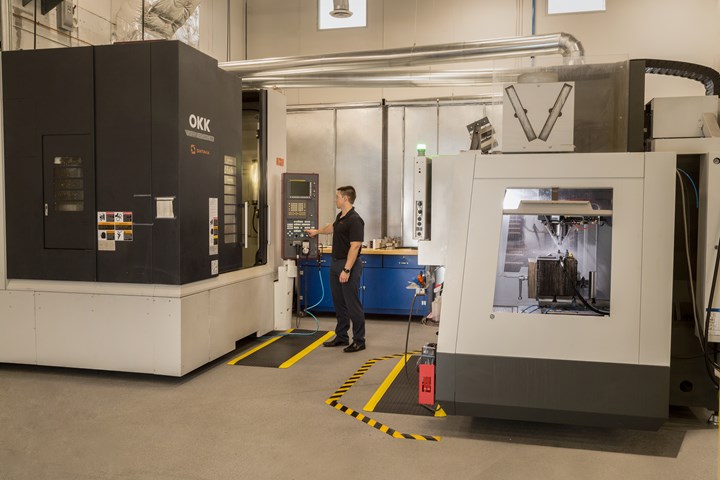
CNC machining centers in the facility's machine shop. Because metal 3D printing alone can't realize the tolerances needed, the expansion of additive manufacturing will create the need for more machining capacity. Photo: Sintavia.
6. No Smokestacks
When Neff points out that the AM facility has “no smokestacks,” he means that figuratively. Facilities doing machining, molding or assembly do not have smokestacks, either. What he means is waste streams: In additive manufacturing, the amount of waste is slight and the streams of waste are slender.
But they are challenging nonetheless. Indeed, Neff notes how AM faces challenges specifically because waste streams are so slight. The condensate in metal AM is a waste byproduct produced in such small quantities that no market-driven solution has yet appeared to receive and process this waste. Sintavia might be among the first companies generating byproducts such as this in sufficient quantities to drive a systemic solution. Finding responsible, sustainable solutions for the environmental impacts of 3D printing processes is one of the chief concerns the company recognizes it has to confront now so that it can scale in the future.
7. Focused on a Purpose
In a sense, the “factory” is back. That is, “factory” meaning a manufacturing facility purpose-built for a given end product. Manufacturing has shifted away from factories over time. Original equipment manufacturers (OEMs) today tend not to make their products, instead performing final assembly of components and subassemblies coming in. Contract suppliers, meanwhile, serve many markets — any given molder or machine shop might do business in aerospace, automotive, medical and other industries at once. But the Hollywood facility is something different. Sintavia is not an OEM, nor a general-purpose contractor. The facility here truly is purpose-built: a factory for turning powder metal into aircraft engine parts.
This is a subtle point, and an important one. Additive manufacturing is far more than a different manufacturing process or operation. It is also an approach to production that suggests an altogether different type of manufacturer.
8. Data and Documents Are Part of the Process
This point is not different from other aircraft-industry production facilities, but notable in the case of AM. Namely, a facility and an enterprise purpose-built for aerospace production has to account for the tracking and documentation needs of that production. Consolidating value and assembly into unified 3D printed complex parts in some sense consolidates all the paperwork of that value onto those parts as well. This is visible in Sintavia’s quality and inspection area, where the shelves for waiting parts stand near the shelves for the documentation accompanying them. “The paperwork can weigh more than the parts,” one technician noted.
9. Uninterrupted Power
Florida equals hurricanes. However, in a production facility where various jobs at any given time might be in the midst of one- or two-week-long delicate build cycles, continuous power is essential for ensuring the value of all the build time expended so far is not lost. For Sintavia, flywheel-driven power systems keep all of the building running for 30 seconds after a power loss, providing enough margin for the 15 seconds required for generators to switch on and take over. With its backup power resources, Sintavia can run exclusively on generator power for at least two weeks, says Neff.
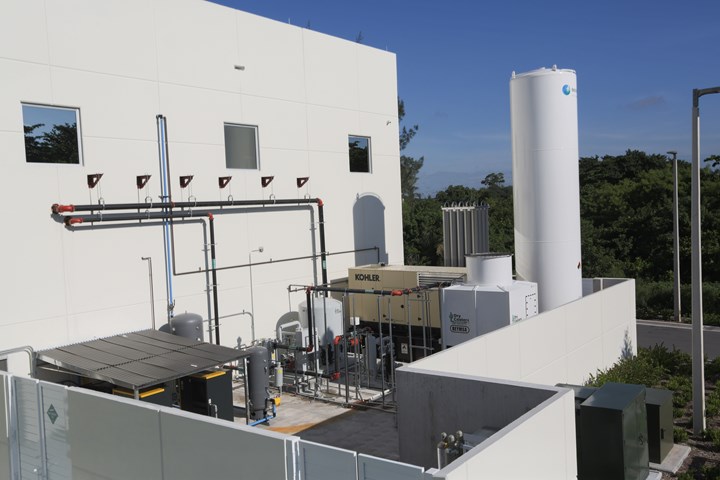
Generator capacity seen here can keep the facility running for at least two weeks after a power loss. Photo: Sintavia.
10. Customized Quality System
“When I talk to people about this facility, and the investment it has required, they look at the machines and think they see the cost there. But that’s not it. Our most costly investment has not been equipment, it has been the development of our quality system,” Neff says.
In developing this system over time, that investment was often paid in the form of instructive failure. “We have never been beaten by a part,” Neff says. But attaining precise, repeatable production of a challenging part, and systemizing the techniques necessary to assure that production — particularly at earlier times in the company’s development — sometimes might have required 20 or more iterative builds of the same component.
There is no ready template for the resources and procedures necessary to achieve a controlled, validated AM part production facility, he says. Conventional manufacturing processes do offer examples of other successful facilities to copy, but in additive production of high-end aircraft parts, the models are fewer. Sintavia’s team had to work out the steps and resources needed.
This, then, is perhaps the most fundamental difference between the Sintavia site and another, established production facility: the definition of the quality procedures. This is also the difference hardest to see. Indeed, it is invisible, except for the glimpses of details such as the pill bottles for in-situ powder inspection, the precautions around receiving and storing powder and (not yet noted but just as much a part of the system) the precaution against turning off lights or moving metal carts too close to the machines in the electron beam PBF room, because of the potential effect on the machines’ magnetic fields.
The facility is just the manifestation, just the physical resources. In realizing the capability to apply AM to high-end part production, what Sintavia really has had to build was the process.
Related Content
Additive/Subtractive Hybrid CNC Machine Tools Continue to Make Gains (Includes Video)
The hybrid machine tool is an idea that continues to advance. Two important developments of recent years expand the possibilities for this platform.
Read MoreDigital Transparency in Machining Key to Multi-Site Additive Manufacturing
Cumberland Additive’s CNC programmer in Pennsylvania spends most of his time writing programs for machine tools in Texas.
Read MoreA Fond Farewell to My Additive Friends
In his final “Additive Insights” column, Tim Simpson reflects on how additive manufacturing has progressed in the last six years. Standards and software are two examples.
Read MoreJTEKT Technology Days Showcases Synergies
The event took place following the company’s completion of its new showroom and decision to merge several of its brands under the JTEKT name.
Read MoreRead Next
Scaling Production at Sintavia Reveals Sustainability Challenges with AM
Additive manufacturing has not yet fully confronted all the factors that contribute to sustainability. Sintavia is discovering and working through these issues in metal AM as its production work scales.
Read More5 Rules of Thumb for Buying CNC Machine Tools
Use these tips to carefully plan your machine tool purchases and to avoid regretting your decision later.
Read MoreBuilding Out a Foundation for Student Machinists
Autodesk and Haas have teamed up to produce an introductory course for students that covers the basics of CAD, CAM and CNC while providing them with a portfolio part.
Read More