A Fond Farewell to My Additive Friends
In his final “Additive Insights” column, Tim Simpson reflects on how additive manufacturing has progressed in the last six years. Standards and software are two examples.
Share




All good things must come to an end, as they say, and so it is for my column — but not for additive manufacturing (AM) by any means. If anything, AM is on more solid footing now than it was six years ago when I wrote my first column, and its future looks brighter than ever.
The changes over the last six years have been remarkable. AM systems are bigger and faster, and prices on machines and materials continue to fall. Reliability and repeatability have improved dramatically given all that has been learned about the process physics underpinning the different technologies. We can now model and simulate AM processes to help optimize process parameters faster and reduce the likelihood of build failures, saving companies hundreds of thousands of dollars, if not more, during ramp up to additive production.
Meanwhile, interest in topology optimization tools and generative design software continues to increase given the ability to optimize and lightweight components with AM. Established software providers are investing in their CAD and CAE tools like never before, and dozens of new startups have emerged to provide new design capabilities and tools, many of which have already been acquired and integrated into existing software to improve the digital workflow that underpins AM.

Me and my 3D printed replica from Doob-3D. The 3D printed replica is made from my “digital twin” which was created using full-body 3D imaging technology. Photo Credit: Tim Simpson
While new software tools for design abound, the future is full of potential for AM materials. As our understanding of the process physics has improved, so has our ability to design and tailor alloys, microstructures and properties to different applications. The ability to process multiple materials at once to vary alloy composition and functionally grade an AM component opens up entirely new realms for designers to engineer superior parts and products. The material freedoms of AM have long been overshadowed by the focus on design freedom, but that is certain to change in the near future.
Standards for AM have also advanced rapidly over the past decade, particularly the last few years — an unexpected benefit from the pandemic lockdown. This is great for companies new to AM, but it is easy to get overwhelmed by all of the options that are now available. Thankfully, ANSI and America Makes are pushing another standards coordination effort to identify gaps and ways to harmonize the plethora of standards that have finally been created in response to the demands from industry.
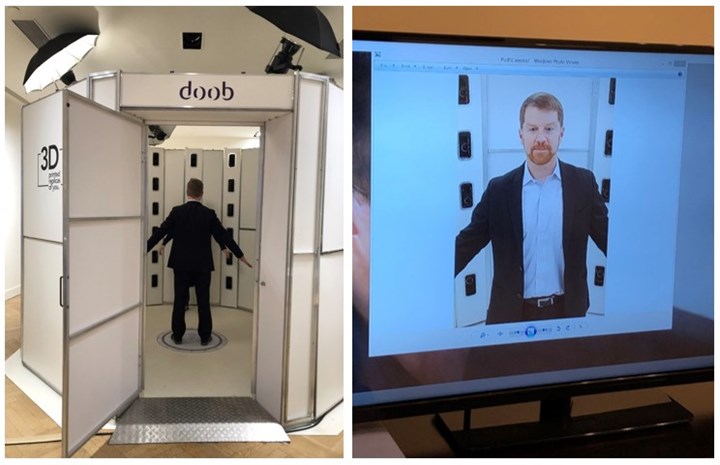
Me getting 3D scanned to create my “digital twin” so that I could be 3D printed.
Photo Credit: Tim Simpson
In addition to new standards, requirement documents for AM parts have been publicly released for aerospace materials systems by SAE International and for space flight by NASA. These add to the growing body of regulatory policies and guidance documents that have existed in several fields, including the medical industry which embraced AM early. These not only help boost the confidence for companies new to the game but also strengthen the return on investment that many companies have been anxiously awaiting.
While making a compelling business case for AM may still seem far off for many, companies in nearly every industry have found a way to profit from AM, including metals. Medical implants have been transformed by AM, following suit behind hearing aids, aligners and dental implants. The space industry has fully embraced AM and is pushing the boundaries on performance and productivity faster than most people think possible. Meanwhile, legacy parts for automotive, aerospace and defense applications can now be easily replaced, and many supply chain disruptions can be alleviated with AM. In fact, thanks to the resiliency that AM showed during the pandemic, government programs like AM Forward led by ASTRO America are poised to transform the supply chain and help regionalize manufacturing. This is good for the economy and exciting for the workforce, but the fight for talent will only intensify. Companies will need to invest in their people as well as their products and processes; otherwise, the competitive advantage that AM enables will not materialize if the talent is not there to help.
It is clear that the future of manufacturing will be digital, thanks to AM and other advanced manufacturing technologies that rely so heavily on data. The data being generated during the process is already being harnessed to create “digital twins” that will contribute to the “digital thread” that will tie the “digital workflow” and the “digital factory” together. Artificial intelligence (AI) and machine learning (ML) are poised to assist and will play a critical role in ensuring part quality as companies shift to production with AM and other digital manufacturing technologies.
While this may frighten some of you, I believe the future of manufacturing is brighter than ever before, and I think the machining experts and manufacturing professionals are poised to be the digital pioneers of the future. Will you accept the challenge and take the risk? I hope so!
Thanks all and good luck!
Related Content
Go Digital: How to Succeed in the Fourth Industrial Revolution With Additive Manufacturing
The digitalization of manufacturing is set to transform production and global supply chains as we know them, and additive manufacturing has been leading the way in many industries.
Read MoreDigitalization and Done-In-One Reign Supreme at BIEMH 2024
European manufacturers may have a different balance of markets than their U.S. counterparts, but the practical challenges they must overcome are often similar — as are the solutions.
Read MoreChuck Jaws Achieve 77% Weight Reduction Through 3D Printing
Alpha Precision Group (APG) has developed an innovative workholding design for faster spindle speeds through sinter-based additive manufacturing.
Read MorePush-Button DED System Aims for Machine Shop Workflow in Metal Additive Manufacturing
Meltio M600 metal 3D printer employs probing, quick-change workholding and wire material stock to permit production in coordination with CNC machines.
Read MoreRead Next
5 Rules of Thumb for Buying CNC Machine Tools
Use these tips to carefully plan your machine tool purchases and to avoid regretting your decision later.
Read MoreSetting Up the Building Blocks for a Digital Factory
Woodward Inc. spent over a year developing an API to connect machines to its digital factory. Caron Engineering’s MiConnect has cut most of this process while also granting the shop greater access to machine information.
Read MoreRegistration Now Open for the Precision Machining Technology Show (PMTS) 2025
The precision machining industry’s premier event returns to Cleveland, OH, April 1-3.
Read More