WFL Provides Basic and Advanced Process Monitoring Systems
The iControl from WFL enables users to monitor up to 16 process signals, incorporates data from external sensors, offers red and yellow limit settings and more.
Share




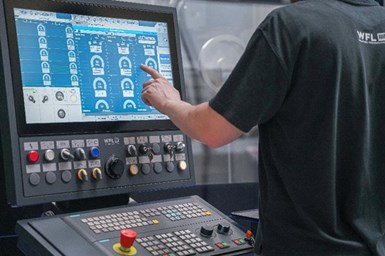
The iControl intelligent process monitoring system follows a multilevel monitoring logic to respond when collision limits or process limits are exceeded or if there are significant, rapid changes in force.
WFL Millturn Technologies has announced the new WFL iControl system, which enables process signals to be registered, evaluated and recorded in the CNC-kernel of the control with the maximum sampling rate. The company offers two variants. The iControl Basic monitors designated maximum machine loads and triggers a quick stop within ten milliseconds if these are exceeded. The iControl Advanced has this functionality, but also enables users to select an individually customizable monitoring strategy for each machining operation. The software was designed to ensure that the right monitoring strategy could be easily selected and freely combined with other limits.

As many as 16 process signals can be monitored using iControl.
Up to 16 process signals can be monitored; these are configured by WFL at the factory according to the machine equipment and displayed live on the control screen. The process signal from a complete machining sequence can be recorded using a teach-in cut. The allocation of upper and lower process limits defines the tolerance band within which the process signal must remain during machining. If these limits are violated, the machine will stop.
The signal value for process monitoring is derived directly from the drive torques of the NC axes and spindles. An algorithm reportedly eliminates friction and acceleration forces, making it possible to precisely analyze the process signals. The system is especially suitable for automation and series production.
Additional new features include:
- “Yellow limits,” which, when reached, will not stop the machine, but generate a message for the operator
- Ability to integrate external sensors into process monitoring
- Features for detecting tool wear and total breakage, including “wear limit” and “tool missing limit”
- Optional long-time data recording with iControl Data Recording.
- Maximum load selection for individual axes and spindles, up to the collision limit, meaning that there is a pre-set percentage of the maximum permissible load for each axis or spindle
- Option to perform monitoring without teach-in cut
- Monitoring of machining processes with different cutting depths
- Option for early detection of machine wear
Related Content
-
Generating a Digital Twin in the CNC
New control technology captures critical data about a machining process and uses it to create a 3D graphical representation of the finished workpiece. This new type of digital twin helps relate machining results to machine performance, leading to better decisions on the shop floor.
-
How this Job Shop Grew Capacity Without Expanding Footprint
This shop relies on digital solutions to grow their manufacturing business. With this approach, W.A. Pfeiffer has achieved seamless end-to-end connectivity, shorter lead times and increased throughput.
-
5 Tips for Running a Profitable Aerospace Shop
Aerospace machining is a demanding and competitive sector of manufacturing, but this shop demonstrates five ways to find aerospace success.