Walter Surface Technologies Ceramic Tools Enhance Product Life
Walter’s Smart Resin Technology is designed to achieve a productive balance between sharpness and tool life in a metalworker’s given application.
Share




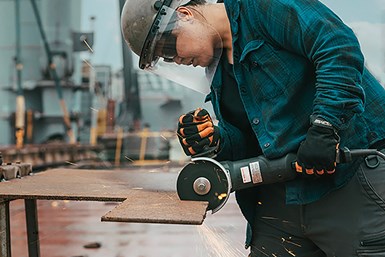
Walter Surface Technologies has launched three new technologies to further maximize life of its high-performance ceramic abrasives.
Walter’s Smart Resin Technology, found in bonded abrasives such as the Zip XX and the Xcavator XX, works to expose fresh ceramic grains at the optimal moment to achieve a productive balance between sharpness and tool life in a metalworker’s given application.
Walter’s V-Strong Backing Technology, found in its ceramic sanding discs such as the Xtracut and the Coolcut XX, is said to improve durability and toughness of the wheel due to to stronger resistance of the cloth. “With 14% more vulcanized fiber in the cloth than competitors, Walter ceramic sanding discs last longer, resulting is less wheel changeover,” says Marc Brunet Gagné, senior product manager, abrasive power tools. He adds, “Ceramic grains provide longer life, higher removal rates and improve comfort for operators.”
“Most flap discs are baked during the manufacturing process to bond the flaps to the backing. Unfortunately, this process can dry out the backing cloth of the flaps, reducing its performance” explains Brunet Gagné. To avoid this, Walter’s new Max Life cold curing glue is said to provide the freshest abrasives possible to avoid micro-cracking and drying out, which improves consistency and can reportedly extend disc life by up to 25%.
Related Content
-
Shoulder Milling Cuts Racing Part's Cycle Time By Over 50%
Pairing a shoulder mill with a five-axis machine has cut costs and cycle times for one of TTI Machine’s parts, enabling it to support a niche racing community.
-
How to Troubleshoot Issues With Tool Life
Diagnosing when a tool is failing is important because it sets an expectation and a benchmark for improvements. Finding out why gives us a clue for how to fix it.
-
Selecting a Thread Mill That Matches Your Needs
Threading tools with the flexibility to thread a broad variety of holes provide the agility many shops need to stay competitive. They may be the only solution for many difficult materials.