Volkmann Introduces Self-Contained Metal Powder System
Volkmann’s PowTrex system safely and automatically transfers 3D-printing powders in large volumes from a container or supply hopper to one or more machines without risk of spillage, contamination, explosion or contact with workers.
Share



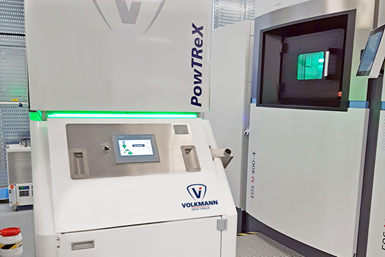
3D-printing equipment manufacturer Volkmann USA has added its PowTrex system for the safe transfer, recovery and reuse of metal powders to its on-site test laboratory. The PowTrex metal powder transfer system was installed to permit material formulation testing and verify system performance in operating conditions that closely simulate an actual additive manufacturing environment. According to Volkmann, approximately five cubic feet of each non-hazardous metal powder can be provided when scheduling a test to ensure the testing is accurate and the results are actionable.
Suitable for testing a wide range of metal powders and other materials with bulk densities up to 400 lbs/ft.3, the PowTrex system safely and automatically transfers 3D-printing powders in large volumes from a container or supply hopper to one or more machines without risk of spillage, contamination, explosion or contact with workers. The self-contained metal powder handling system loads the material in the printer, unloads and screens unused material and returns the unused material back into the process for substantial savings in material costs. Testing may be viewed live at the test laboratory or streamed live online on Volkmann’s website.
Related Content
-
Increasing Productivity with Digitalization and AI
Job shops are implementing automation and digitalization into workflows to eliminate set up time and increase repeatability in production.
-
Four-Axis Horizontal Machining Doubles Shop’s Productivity
Horizontal four-axis machining enabled McKenzie CNC to cut operations and cycle times for its high-mix, high-repeat work — more than doubling its throughput.
-
How to Accelerate Robotic Deburring & Automated Material Removal
Pairing automation with air-driven motors that push cutting tool speeds up to 65,000 RPM with no duty cycle can dramatically improve throughput and improve finishing.