United Grinding Offers Compact, Automated Parts Loading
The Studer RoboLoad saves shop floor space while offering room for workpieces to be manually loaded on six trays within a small work area.
Share



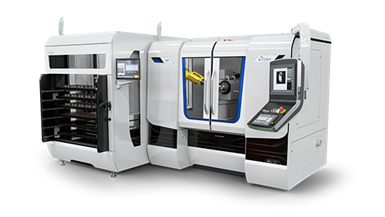
United Grinding’s new Studer RoboLoad system is said to offer manufacturers seamless part-loading automation for CNC radius internal grinding machines such as the company’s Studer S121, S131 and S141. The new Studer loader is said to have a small footprint.
On the Studer S121, S131, and S141 machines – often used to produce dies for the packaging industry – automatic B-axes swivel in a range from -60° to +91°. According to Daniel Schafroth, systems division manager at Studer, this is why any automation must be able to exit the machine and give the B-axis the freedom to swivel — a capability that the Studer RoboLoad offers.
As an external loader, Studer RoboLoad measures 59.06" (1.50 m) wide: half the width of the machine itself. This saves shop floor space while offering room for workpieces to be manually loaded on six trays – each measuring 42.52" × 12.6" (1080 mm × 320 mm) – within a small work area.
“We are not talking about large-scale production, but instead unmanned production during the night shift, for example, or making optimum use of breaks in other production processes,” explains Schafroth. Operators can bring up any grinding program for the workpieces, and the Studer RoboLoad processes them and places each workpiece back in the same place after machining.
For simplicity of operation, the Studer RoboLoad incorporates a setup wizard developed by automation specialists from Wenger of Winterthur, Switzerland. It is said to require no programming knowledge on the part of the setter or machine operator.
Related Content
-
Using the Toolchanger to Automate Production
Taking advantage of a feature that’s already on the machine tool, Lang’s Haubex system uses the toolchanger to move and store parts, making it an easy-to-use and cost-effective automation solution.
-
Cutting Part Programming Times Through AI
CAM Assist cuts repetition from part programming — early users say it cuts tribal knowledge and could be a useful tool for training new programmers.
-
Four-Axis Horizontal Machining Doubles Shop’s Productivity
Horizontal four-axis machining enabled McKenzie CNC to cut operations and cycle times for its high-mix, high-repeat work — more than doubling its throughput.