TDM Systems Software Update Increases Machining Efficiency
The TDM Global Line 2020 release is designed to give users greater transparency regarding their tooling costs and key figures through individually configurable TDM Global Line dashboards.
Share



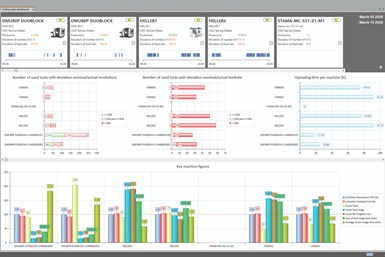
The latest versions of TDM Systems’ TDM and TDM Global Line software includes updates and new modules intended to reduce tooling costs and increase efficiency.
The TDM Global Line 2020 release is designed to give users greater transparency regarding their tooling costs and key figures through individually configurable TDM Global Line dashboards. Users can display the relevant reports in the dashboard, print them or transfer them to Excel.
The 2020 release also includes the TDM Feeds & Speeds Manager. In conjunction with the Comara Box, actual applied cutting data is recorded, compressed and evaluated directly from the machine. By comparing the planned cutting values defined in the NC program with the actual applied cutting values in the machine, users can specify reliable cutting values as early as the planning phase. Expertise from production is saved centrally so the company can retain knowledge, even if employees leave the company.
The latest release also provides new modules such as the TDM NC-Program Manager Global Line, a tool designed to guarantee a continuous production process while retaining existing application expertise for the company.
Managers can use the TDM Purchase Request Module Global Line to manage tool requirements and forward them to an ERP system. This helps the company provide all the required tools at the right time and in the right quantities.
The TDM Barcode Module Global Line expands the Global Line Tool Crib and allows companies to control processes by using barcodes, while the TDM 3D Solid Editor Global Line streamlines modification of 3D models.
Additionally, the completeness check of CAM-specific tool data and the automated calculation of collision data is now more transparent, which is particularly useful for Catia and NX users.
Related Content
-
5 Stages of a Closed-Loop CNC Machining Cell
Controlling variability in a closed-loop manufacturing process requires inspection data collected before, during and immediately after machining — and a means to act on that data in real time. Here’s one system that accomplishes this.
-
Diving Deeper Into Machine Monitoring Data
Data visualization is the first step in using machine monitoring data, but taking it to the next level requires looking for trends within the data.
-
Four Questions (& Answers) About Data-Driven Process Improvement at CNC Job Shops
How can shops can make informed decisions using data-driven feedback to improve shopfloor efficiency and profitability? And how will these technologies differ between high- and low-volume production?