Nikon Metrology's Automation Software Connects the Shopfloor
The Inspect-X Automation OPC UA Interface software integrate third-party industrial, automation and control equipment more easily.
Share




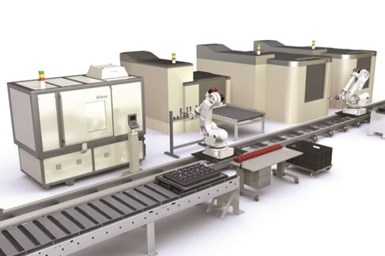
Nikon Metrology’s Inspect-X Automation OPC UA Interface software is designed to simplify the way manufacturing execution systems (MES), statistical process control systems or handling robots communicate with Nikon’s X-ray computed tomography (CT) machines.
The company’s existing systems in production lines use an in-house inter-process communication (IPC) interface, which requires working knowledge of the X-ray CT system and a software developer who understands the Nikon IPC contract. While this interface remains in the software for intricate control of the system, applications on the shop floor are now supported by the OPC UA interface. This means that integrators with knowledge of it are able to integrate third-party industrial, automation and control equipment more easily, saving time and costs when installing or reconfiguring production line systems within a single factory, or across multiple connected facilities around the globe.
Nikon says its alignment with the industry-standard OPC UA communication protocol shows its intention to developing fully automated, non-contact, X-ray CT quality control systems for the shop floor. X-ray CT is able to inspect and measure the interior of components non-destructively as well as the exterior. According to Nikon Metrology, the OPC UA interface is now one of the main communication protocols for networking within Industry 4.0 factories.
Related Content
-
Cutting Part Programming Times Through AI
CAM Assist cuts repetition from part programming — early users say it cuts tribal knowledge and could be a useful tool for training new programmers.
-
The Power of Practical Demonstrations and Projects
Practical work has served Bridgerland Technical College both in preparing its current students for manufacturing jobs and in appealing to new generations of potential machinists.
-
How to Mitigate Chatter to Boost Machining Rates
There are usually better solutions to chatter than just reducing the feed rate. Through vibration analysis, the chatter problem can be solved, enabling much higher metal removal rates, better quality and longer tool life.