GCH Machinery Redesigns Grinding System for EV Manufacturer
GCH Machinery redesigned and repurposed an electric vehicle automaker’s older dual-head grinder to the latest technology. The redesign was aimed at fulfilling the automaker’s green initiative.
Share





ECi Software Solutions, Inc.
Featured Content
View More
.png;maxWidth=45)
DMG MORI - Cincinnati
Featured Content
View More

Autodesk, Inc.
Featured Content
View More
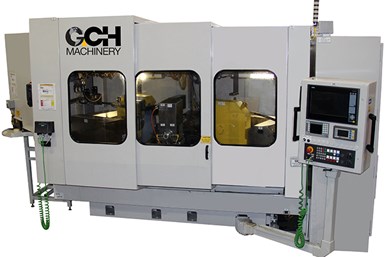
GCH Machinery recently shipped a turnkey grinding system to a major automaker. The grinding system will reportedly be used to manufacture transmission parts for the carmaker’s electric vehicle (EV) product line.
GCH Machinery redesigned and repurposed the automaker’s older dual-head grinder to the latest technology; in addition, the redesign was aimed at fulfilling the automaker’s green initiative. According to GCH Machinery, high-efficiency motors and a mist containment system are among the new system’s components that will support the company’s move toward environmentally friendly manufacturing.
This fully automated grinder, with two separate and independent grinding wheel spindles, can reportedly process two ends of the part simultaneously, which is said to eliminate the need for a second grinder. The machine’s ability to process specific sections of the part at the same time leads to a more accurate part, according to the company, which is critical to any transmission.
“We took an older machine that wasn’t able to hold size and was difficult to keep in operation due to its many older components, and retooled it for two brand-new EV parts,” explains Dan Geddes, president of GCH Machinery. “The automated turnkey system produces parts that meet the automaker’s tight tolerances.”
The grinder is said to meet all of the automaker’s green standards, as well as the safety standards established by the UL. Other features of this remanufactured grinder include updated electrical controls, an internal robot, an in-process part gaging system, an HMI touch screen, a wheel balancer, an automatic part de-oiler and new lubrication, pneumatic and electrical systems.
“We know that more and more of our automotive partners are offering hybrid and electric vehicles. Our process translates to the needs of the growing EV industry,” says Geddes, who adds that “GCH is actively implementing ways to cut our own carbon footprint.”
Related Content
-
The Role of Surface Finishing in Modern Manufacturing: Trends and Best Practices
You’re attending IMTS to advance your business. Regardless of your role in the manufacturing process, considering how your parts will be finished is crucial. This article can help you understand trends in surface finishing and better communicate with your finishing partners.
-
4 Steps to a Cobot Culture: How Thyssenkrupp Bilstein Has Answered Staffing Shortages With Economical Automation
Safe, economical automation using collaborative robots can transform a manufacturing facility and overcome staffing shortfalls, but it takes additional investment and a systemized approach to automation in order to realize this change.
-
Sunnen Products Company Partners With Hendrick Motorsports
The partnership puts the new Sunnen SV-series honing machine in the Hendrick Motorsports engine operation alongside other Sunnen honing and engine building machines.