What a Machining Center Really Costs: Total Lifecycle ROI
A white paper explains why it’s important to look at the entire lifecycle of a machine to determine its true costs and benefits.
Share




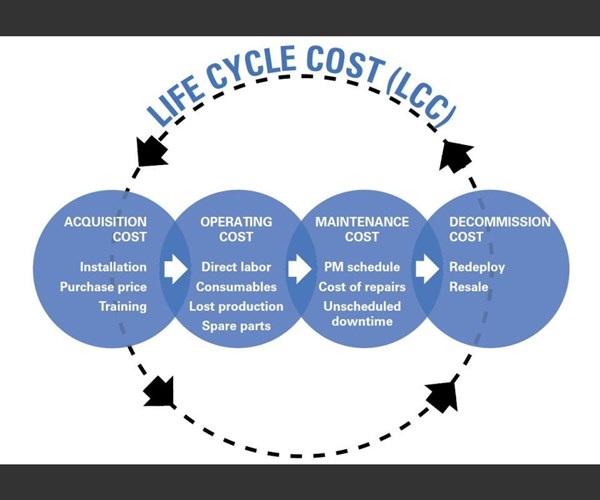
A white paper explains why it’s important to look at the entire lifecycle of a machine to determine its true costs and benefits.
The problem is simple to define, but getting ahead of it can quickly become complex: “Manufacturers often focus only on equipment price when making [return-on-investment (ROI)] calculations and fail to evaluate the total life cycle cost or anticipated performance of the equipment.”
That’s how Makino's white paper, “High-Performance Machining Center ROI: How to Determine a Machine’s True Value” begins. The true cost of a vertical or horizontal machining center cannot be encompassed by its asking price. The authors, Vice President of Finance Tom Scherpenberg and former VP Tom Clark, argue that you have to consider operation, maintenance and decommission costs in any serious evaluation of the expenses and revenues generated by a particular machine.
Editor’s Note: In place of the white paper, Makino now hosts a webinar of the same title, linked above.
Given a moment’s reflection, this makes obvious sense, but it can be difficult to account for all the ways a machine impacts the bottom line over the course of its life cycle. Their paper outlines four categories to keep track.
1. Acquisition Costs
In general, these costs relate to obtaining and setting up the machine:
- Purchase price
- Installation and setup
- Employee training
The authors add that post-sale service, supplier reputation, equipment warranty and support services are also important at different times in the machine’s life cycle. For example, they write, “A vendor’s availability to conduct operations and maintenance training and improve employee competency is something that can prevent productivity drag.”
2. Operation Costs
These costs come from the accumulated hours of cutting metal on the machining center. For Mr. Clark and Mr. Scherpenberg, estimating operation costs requires carefully looking at how the machine’s design and construction might impact its productivity.
Cycle Time
Cycle time is an important component of determining lifecycle ROI for a machine. The authors cite the following machine features as examples of design elements that can affect cycle times and hence ROI:
- A high-power spindle can speed cutting
- A larger spindle bearing can better handle cutting forces for greater accuracy and hence less finishing work
- Acceleration/deceleration rates can affect non-cutting time
- Structural characteristics such as single-piece casting, three-point leveling, and a tiered or stepped column design can reduce machine vibration for greater accuracy
Another thing to remember when thinking about cycle time is part setup. Can multiple workpieces be prepared in a single setup? Can the machine be preprogrammed for each job? Cranking out more parts with less labor automatically lowers the cost per part.
Tool Life
Operation costs should also take account of tool life. As noted above, the way the machine design handles cutting forces and maintains stability ultimately has effects on ROI. The authors note the benefits of rigid construction and extended tool life:
- Fewer necessary cutting passes reduce processing times
- Less rotational deflection due to stability issues leaves less stock for the finish tools
- Fewer passes from finish tools are necessary for certain features
- Increased metal removal rates are realized from cutting at deeper axial depths
In addition, the authors write, longer tool life means less labor devoted to changing tools, measuring them, updating tool information and other associated tasks.
Part Quality
Rigid, accurate machining directly affects a third category of operational costs: part quality. Parts machined to tighter tolerances and higher-quality surface finishes are less likely to require secondary operations like spotting, hand finishing or EDM processes. Reducing extra processing obviously has an impact on turnaround and lead times.
Process Reliability
ROI can be affected by the amount and type of labor involved over the course of a machining cycle. Control and programming features that enable uninterrupted or unattended machining can bump up return because of less need for operator intervention and thus fewer chances for the introduction of mistakes or variation.
3. Maintenance Costs
Although maintenance budgets are usually incorporated into operating costs, the authors say they may not be accurately reflected in machine ROI calculations. Maintenance means downtime, and repairs usually mean unscheduled downtime, but the authors also astutely note that maintenance issues can affect a machine’s productivity well before it finally goes down for repairs.
For example, the authors present a hypothetical scenario in which a ballscrew needs to be replaced. The shop must see to the costs of the part and its installation, scrapped parts, unplanned downtime and overtime to catch back up. But that ballscrew didn’t fail all at once. “The machine was likely declining in performance before anyone realized what went wrong,” they write. That gradual failure could also easily reduce part quality.
4. Decommission Costs
Finally, the authors argue that ROI should account for the residual value of the machine and the costs and benefits of disposing of or continuing to use the machine once payments are completed or the lease expires. A lower-cost machine’s maintenance costs tend to increase during years four through 12, negatively affecting part quality, scrap and tooling costs. Some high-performance machine tools, the authors write, may retain 50 percent of their value by the three-year mark. These sorts of estimates ought to be included in ROI calculations.
The full, 13-page white paper includes more details about each of the four categories of costs affecting a machine’s total lifecycle ROI. In addition, the paper includes a section on how adding automation can improve ROI on some machine tools; a section comparing the impact of leasing versus buying a new machine; and a couple examples of ROI spreadsheets with links to downloadable, interactive versions. Find the full white paper at makino.com.
This blog post originally appeared on techspex.com.
Related Content
How to Successfully Adopt Five-Axis Machining
While there are many changes to adopt when moving to five-axis, they all compliment the overall goal of better parts through less operations.
Read MoreCNC Machine Shop Honored for Automation, Machine Monitoring
From cobots to machine monitoring, this Top Shop honoree shows that machining technology is about more than the machine tool.
Read More6 Machine Shop Essentials to Stay Competitive
If you want to streamline production and be competitive in the industry, you will need far more than a standard three-axis CNC mill or two-axis CNC lathe and a few measuring tools.
Read MoreBallbar Testing Benefits Low-Volume Manufacturing
Thanks to ballbar testing with a Renishaw QC20-W, the Autodesk Technology Centers now have more confidence in their machine tools.
Read MoreRead Next
Registration Now Open for the Precision Machining Technology Show (PMTS) 2025
The precision machining industry’s premier event returns to Cleveland, OH, April 1-3.
Read More5 Rules of Thumb for Buying CNC Machine Tools
Use these tips to carefully plan your machine tool purchases and to avoid regretting your decision later.
Read MoreSetting Up the Building Blocks for a Digital Factory
Woodward Inc. spent over a year developing an API to connect machines to its digital factory. Caron Engineering’s MiConnect has cut most of this process while also granting the shop greater access to machine information.
Read More