Vise System for Quickly Clamping 16 Parts
A New York job shop minimizes setup and change-over time with a homegrown system consisting of closely spaced double-acting vises embedded into a plate. After using it for decades, the shop is now supplying this system to other shops.
Share






.png;maxWidth=45)
DMG MORI - Cincinnati
Featured Content
View More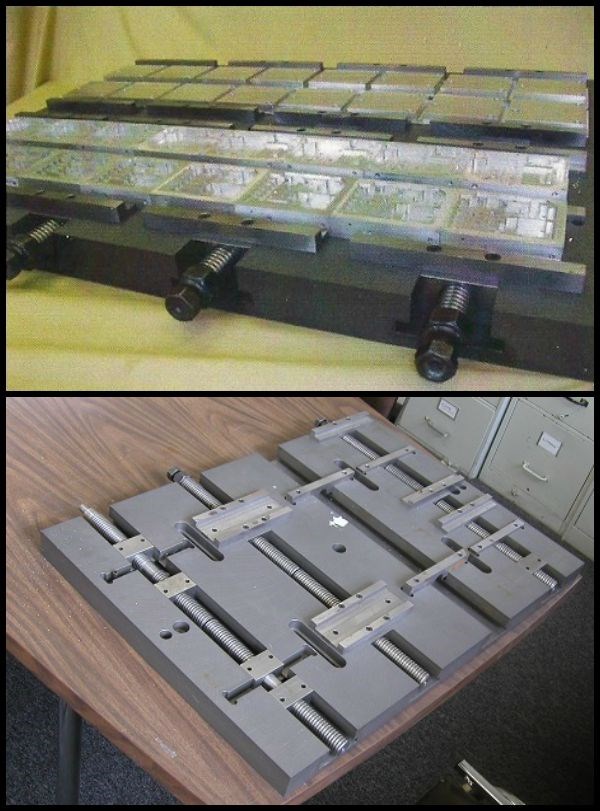
The workholding system that TRP Machine is calling the “MV16” is not actually a new product, but instead it is the way this Bohemia, New York job shop has held parts for machining for more than 20 years. Looking for a simple and inexpensive way to (A) hold several workpieces in one machining cycle, (B) hold a variety of different part numbers without setup changes, and (C) load and unload workpieces quickly from one machining cycle to the next, the shop devised a workholding system on its own able to realize those objectives. What is new now, says shop owner Roger Price, is that TRP has begun to manufacture the MV16 as a product available to other machine shops.
The system is essentially a single large plate embedded with eight independent and closely spaced double-acting vises. Each of the 16 jaw positions opens to a width of 3.25 inches, and clamps parts to a location repeatability of 0.0005 inch. Thus, 16 identical pieces can be quickly and precisely clamped for machining in the same setup, or 16 entirely different parts can be clamped into a single setup as well. Or, since the jaw positions lie in parallel, a row of four jaw positions at once can be used to clamp a workpiece up to 28 inches long.
Mr. Price says the system has been invaluable to TRP in allowing the shop to maintain high in-cut time percentages on its machining centers. The standard MV16 plate is 20.25 by 28.25 inches, but he says the system can also be customized to different sizes and even to a different number of vise positions. A tombstone version of the system uses four double-acting vises on each of four different faces to achieve a total of 32 jaw positions. Learn more from TRP Machine.
Related Content
-
Chuck Jaws Achieve 77% Weight Reduction Through 3D Printing
Alpha Precision Group (APG) has developed an innovative workholding design for faster spindle speeds through sinter-based additive manufacturing.
-
Lean Approach to Automated Machine Tending Delivers Quicker Paths to Success
Almost any shop can automate at least some of its production, even in low-volume, high-mix applications. The key to getting started is finding the simplest solutions that fit your requirements. It helps to work with an automation partner that understands your needs.
-
Fixturing Castings Made Simple Through Adhesive Workholding
When a casting proved too malleable for traditional gripping, Thomas/Euclid Industries adopted — and succeeded with — Blue Photon adhesive workholding.