Tungaloy’s Product Seminar Focuses on Reducing Real Costs of Production
More than 1,050 products are included in the latest TungForce line, leveraging coatings and geometries to hit machining costs where it counts: speed.
Share


Hwacheon Machinery America, Inc.
Featured Content
View More






This TungTriShred flute mill on display at Tungaloy’s product seminar is equipped with chip-splitting inserts whose wavy edges break chips and reduce machining load. The inserts are staggered behind one another to clean up the grooves left by the one before, producing a good surface finish.
The key takeaway from Tungaloy’s April 6 seminar introducing the TungForce cutting tool line is this: The only way for tooling to really reduce total machining costs is by increasing productivity.
In terms of total investment, the lion’s share of machining costs (as much as 75 percent) are directly related to time, including labor and the cost of running the machinery. According to presenter Jacob Harpaz, president and CEO of the IMC Group which owns Tungaloy, tooling costs comprise a mere 3 percent of total investment; that means that even if you extended tool life twofold, you’d still only cut 1.5 percent of the total cost of machining. On the other hand, if you can reduce the time of production—by improving feed rates and cutting speeds, for example—then you can potentially make a much bigger dent in the aggregate.
This is the philosophy behind the more than 1,050 new products included under the TungForce banner. Mr. Harpaz introduced the line of tools for turning, grooving, drilling and milling to a crowd of over 500 machinists, distributors and salespeople in Chicago, Illinois, explaining how these tools’ coatings and geometries enable higher feeds and speeds to produce parts faster.
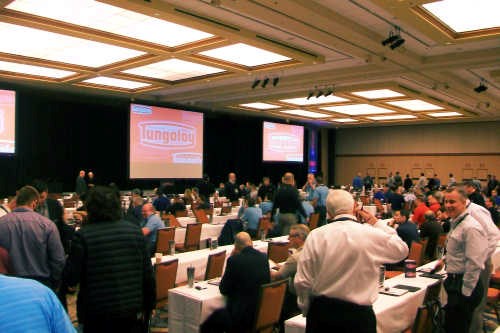
Over 500 people attended the seminar in the Sheraton Grand Chicago hotel.
The TungForce line includes grades with CVD- and PVD-applied coatings that prolong tool life to make up for increases in maximum cutting speeds. A post-treatment process is said to reduce thermal cracks that usually form in the coatings after the high-temperature deposition process, which further boosts tool life.
Meanwhile, the inserts’ geometries are designed to enable faster feed rates with chipbreakers and splitters. For the milling tools, positive rake angles and secure insert clamping enable faster, shallower cuts for roughing operations.

The horizontally-poised tools shown here are part of the DeepTriDrill series of indexable gundrills. Chip splitters allow for higher feed rates, and guide pads promote circularity and straightness, even with the series’ longest tool measuring 59 inches (1,500 mm)—90 times diameter.
Look for product releases on individual series within the TungForce line in upcoming issues of the magazine.
Related Content
-
Shoulder Milling Cuts Racing Part's Cycle Time By Over 50%
Pairing a shoulder mill with a five-axis machine has cut costs and cycle times for one of TTI Machine’s parts, enabling it to support a niche racing community.
-
Selecting a Thread Mill That Matches Your Needs
Threading tools with the flexibility to thread a broad variety of holes provide the agility many shops need to stay competitive. They may be the only solution for many difficult materials.
-
Quick-Change Tool Heads Reduce Setup on Swiss-Type Turning Centers
This new quick-change tooling system enables shops to get more production from their Swiss turning centers through reduced tool setup time and matches the performance of a solid tool.