Tool Setting Fixture Boosts Process Security for High-Volume Shop
Along with switching to a different milling tool to improve surface finishes on aluminum parts, Alupress also employed Mapal's Uniset-P setting fixture to make the process reliable and efficient.
Share





Patrick Wittig operates Mapal’s Uniset-P, which has been in the presetting room of Alupress in Berlin since October 2018.
Alupress Berlin GmbH is a specialist in the complex machining of die-cast aluminum parts, manufacturing such workpieces to micron-level accuracy in large-scale series production. Very precise tools are required to achieve this kind of production. When these tools need to be set, Alupress has come to rely on Mapal’s Uniset-P setting fixture.
Every week, 75,000 completely machined aluminum housings and flanges leave Alupress. More than 80% of these parts are manufactured using cutting tools from Mapal, says Patrick Wittig, who is responsible for tool management in the shop.
Mr. Wittig says that high precision is often a requirement in Alupress’ line of work: “We must manufacture bores in large-scale series production within a tolerance of 5 microns and achieve a surface roughness of Rz = 2 microns.” Such requirements have implications for the tools used.

Mapal employees provide support directly at the machine. Once a week, this technical consultant is on site to ensure the tool stocks are correct, to check newly arrived tools or to initiate repairs, among other things.
Challenge of Setting to the Micron
During the machining of one particular flange, the shop found it was not achieving the required surface finish using a tool with brazed cutting edges. “For this reason, we changed to a milling cutter with adjustable polycrystalline diamond (PCD)inserts,” recalls Burkhard Schimkat, who is responsible for fixture and tool technology at Alupress. However, this kind of tool required that the axial runout on every insert be set to the micron.
Setting the inserts accurately presented a challenge. “We only used an optical setting fixture,” Mr. Wittig says. “However, tactile measurement with contact against the cutting edge was indispensable to manufacture to the required tolerances.” The final accuracy had to be set directly in the machine, and that process was complex, susceptible to mistakes and time-consuming. The machine was kept idle for up to two hours for this reason.
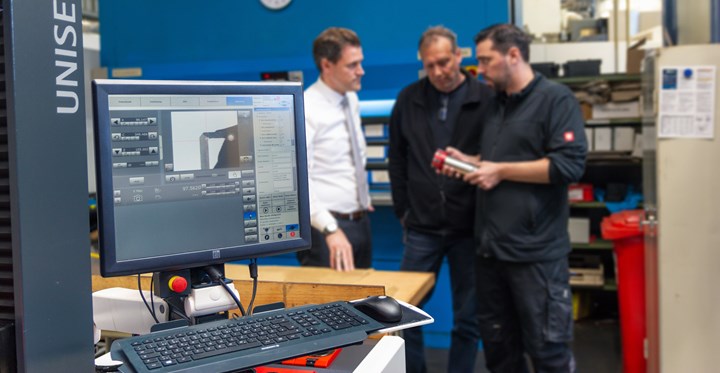
The procedure for setting the tools can be predefined and saved. Operators are then prompted, step by step, cutting edge by cutting edge, through the tool-setting program.
Alupress looked for an alternative for tool setting. “It was only natural we approach Mapal directly with our challenge for setting the tools,” Mr. Wittig says. Through use of Mapal’s Unibase-M dispensing system, the shop became aware of the company’s setting fixtures, including the Uniset-P.
Setting Milling Tools for Success
The portal-type Uniset-P has a measuring camera and backlight source for optical tool measurement housed in the fixture’s pillars. “The setting fixture is equipped with an additional cross-member in the portal,” explains Michael Hils, a product manager with Mapal. Attached to this cross-member are a second camera for making rotation center measurements and cutting edge inspections as well as an axial measuring probe for tactile measurement and axial runout setting with contact against the cutting edge.
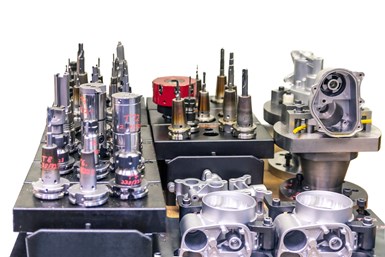
Over 80% of the parts at Alupress are manufactured using tools from Mapal. The company says it was only natural, in that case, to check with Mapal on tool setting guidance.
According to Mr. Wittig, the company sets its PCD face milling cutters to 2 microns using the Uniset-P. Additional fine adjustment of the milling cartridges in relation to the axial runout in the machine compartment is not required thanks to the new setting fixture, he says. For Alupress, this cashes out to big time savings.
“The procedure for setting the tools can be pre-defined and saved,” Mr. Hils says. This means the operator can select the tool to be set on the monitor and receive step-by-step explanations about the values that need to be set. These values are specified once for each tool, then the related measuring program is prepared and saved. “The handling is very straightforward. Once a tool has been added, any of the operators can set the tool,” Mr. Wittig adds. The feature increases process reliability, since required tolerances can only be achieved if the tools are correctly set. Additionally, the second camera enables accurate documentation of such things as cutting edge inspection.
Alupress is satisfied not only with the technology of the setting fixture but also the training. “We have received excellent training on the fixture,” Mr. Wittig says. “As a result, we no longer have any tool bottlenecks.”
Related Content
Walter Ceramic Inserts Enable Efficient Turning, Milling
Suitable turning and milling applications of the WIS30 ceramic grade include roughing, semi-finishing and finishing, as well as interrupted cuts.
Read MoreThe Impact of Cutting Teeth Spacing on Machining Stability
Many cutter designs are available, and variable teeth spacing (or variable pitch) cutters can be used to influence milling stability. Let’s discuss why teeth spacing affects stability.
Read MoreOSG End Mills Provide High-Efficiency Milling
The company has expanded its range of end mills with two offerings for high-speed milling.
Read MoreThe Future of High Feed Milling in Modern Manufacturing
Achieve higher metal removal rates and enhanced predictability with ISCAR’s advanced high-feed milling tools — optimized for today’s competitive global market.
Read MoreRead Next
Tool Management System Eliminates Information Silos
Wagstaff Inc.'s tooling information wasn't digitally traceable or searchable. TDM Systems' Tool Life Cycle Management system reduced lost time and money for the shop.
Read More5 Rules of Thumb for Buying CNC Machine Tools
Use these tips to carefully plan your machine tool purchases and to avoid regretting your decision later.
Read MoreBuilding Out a Foundation for Student Machinists
Autodesk and Haas have teamed up to produce an introductory course for students that covers the basics of CAD, CAM and CNC while providing them with a portfolio part.
Read More