Swiss Grinding Technology in Motion
During a recent open house at Studer’s headquarters in Switzerland, the company highlighted advances in cylindrical grinding technology including automation solutions to enable long stretches of unattended operation.
Share





During this year’s Motion Meeting, Studer unveiled its second-generation Wiredress EDM dresser for grinding wheels. This new design features a number of additively manufactured components.
Early this month, I attended Fritz Studer AG’s annual Motion Meeting at its headquarters in Thun, Switzerland. (Studer is a member of the United Grinding Group.) This year’s event theme was “art of grinding,” and I learned a good bit about the state of the company, recent advances in its cylindrical grinding technology and its automation offerings ranging from basic to highly customized.
Studer’s sales in 2019 was third-best in the company’s history. Although it faced challenges in the automotive industry, it sales grew in the aerospace sector. It continues to ramp up production of new universal cylindrical grinding models such as the S31, S33 and Favorit. In fact, the company sold more than 100 of these machines last year.

Over 20 years, Studer has rebuilt more than 400 CNC grinding machines. Here is a wheelhead before rebuilding. The next photo shows it after rebuilding.
Studer is also upgrading its in-house machining capabilities for critical components such as spindle shafts by adding five-axis and turn-mill multitasking machines. In addition, the company continues to implement its Smart Factory manufacturing concept using data-driven concepts to streamline grinding machine production.
During the event, it highlighted its grinding machine rebuilding services, which had its highest sales in 2019. Studer has offered this service for 20 years and has overhauled more than 400 machines to date. During the rebuild process, each machine is completely disassembled and brought back to optimal performance with new components. Customers can request machine reconfigurations or add automated functionality, and each rebuilt machine comes with a one-year warranty. Customers can also request loaner machines to use while theirs are being refurbished. The cost of a typical machine rebuild is roughly half of a comparable new machine.

This wheelhead has been completely overhauled as part of Studer’s rebuilding service.
Studer also unveiled what it believes to be a few significant grinding technology advances at the event. One is the second generation of its Wiredress wire EDM wheel dresser, which dresses metal-bonded wheels while they remain mounted in the grinder. What’s interesting is that multiple components in this new version are produced via additive manufacturing. These AM parts are manufactured by the company’s IRPD (Institut for Rapid Product Development) business unit. IRPD originated at Switzerland’s St. Gallen University in 1996 and became part of the United Grinding Group in 2015. In addition to producing parts for the Group’s grinding machines, IRPD offers AM consulting, design and production services for other companies for both metal and plastic components.
Another development is Studer’s second-generation synchronous tailstock set to replace the existing hydraulic synchronous tailstock design. The new version features a servo drive with electrical clamping instead of hydraulics. It offers an increased stroke of 30 mm, center pressure through both an NC axis and spring tension, low tip pressure and a pneumatic chuck. A third development is in-process laser measurement, which is said to provide 60% faster measurement times compared to conventional techniques.
The company also delivered a presentation highlighting the various ways CNC grinding machines can be automated to enable long stretches of unattended operation. These range from off-the-shelf alternatives to highly customizable solutions.

The Easyload unit, which features a gantry loader and parts trays, is an example of an entry-level automation solution for cylindrical grinding machines.
For example, its Easyload is an entry-level model featuring a gantry loader for shaft components as long as 300 mm and diameters ranging from 4 to 30 mm. The WeStack and WeSpeed cells, manufactured by Wenger Automation and Engineering AG, enables fast changeover of grippers from shaft to chuck parts. Highly customizable automation solutions can include processes such as part deburring, brushing, measurement, demagnification, cleaning and marking.
The company also offers its Flexload enclosed robotic loading unit that can be added to Studer models S31, S33 and S41 cylindrical grinding machines. Developed by United Grinding North America, the Flexload features a six-axis robot on a seventh-axis gantry. The robot with two grippers travels between machine and part collecting trays.
Similarly, the company offers a collaborative robotic loading system (video above) that features a six-axis Staubli robot with a Sick laser that scans the area to detect a person’s presence. When no person has entered either a defined outer or inner zone surrounding the robot, the robot operates at full speed. When a person enters the outer zone, the robot slows. When a person enters the closer inner zone, the robot stops. Once the zones are cleared of people, an operator can re-start the robot. This eliminates the need for safety fencing or enclosures industrial robots typically required to prevent worker injury.
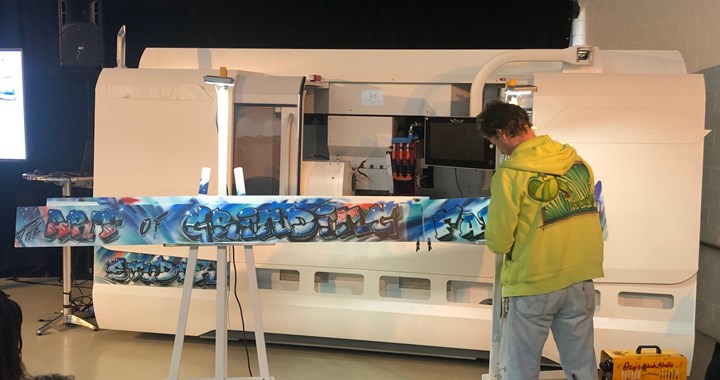
The theme of this year’s Motion Meeting was “the art of grinding.” Here’s a Favorit-model machine that will soon have a completely new look.
Related Content
Four-Axis Horizontal Machining Doubles Shop’s Productivity
Horizontal four-axis machining enabled McKenzie CNC to cut operations and cycle times for its high-mix, high-repeat work — more than doubling its throughput.
Read MoreInvesting in Automation, Five-Axis to Increase Production Capacity
To meet an increase in demand, this shop invested heavily in automation solutions and five-axis machines to ramp up its production capabilities.
Read MoreUsing the Toolchanger to Automate Production
Taking advantage of a feature that’s already on the machine tool, Lang’s Haubex system uses the toolchanger to move and store parts, making it an easy-to-use and cost-effective automation solution.
Read MoreWhich Approach to Automation Fits Your CNC Machine Tool?
Choosing the right automation to pair with a CNC machine tool cell means weighing various factors, as this fabrication business has learned well.
Read MoreRead Next
United Grinding Unveils New Ohio Facility
The new facility will consolidate the company’s offerings in a single location in Miamisburg, Ohio.
Read MoreWire EDM for Dressing Metal-Bonded Wheels
The Studer WireDress system, which uses the wire “spark erosion process” to dress a metal-bonded grinding wheel while it is still mounted in the grinder, makes using these wheels more efficient and economical.
Read MoreUnited Grinding Appoints President, CEO
Markus Stolmar has worked more than 20 years with the company in executive positions for its Walter and Ewag brands.
Read More