New CAD/CAM Features Extend Shop's Three-Axis Capabilities
Mastercam’s Dynamic Motion technology enables advanced tool paths that make Industrial Machine & Supply competitive with only a three-axis milling machine.
Share




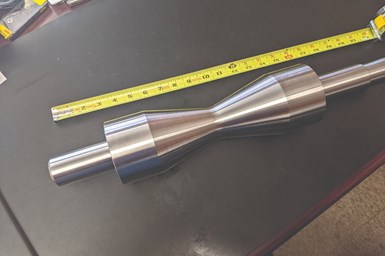
Mastercam’s Dynamic Motion feature enabled IMS to machine a v-roller part at 1,050 sfm with a 25% stepover. Images courtesy of Industrial Machine & Supply, Inc.
Industrial Machine & Supply, Inc. (IMS) cut its teeth on parts for textile mills. But by the time its founder passed the business to his son, David Williams, in the late 1990s, the local textile industry had shrunk. Williams decided to expand the shop’s clientele to international industries like material handling, agriculture, automotive and consumer goods. Doing so, however, required CAD/CAM software.
“I was looking at jobs I knew I could get if I could just write the programs,” Williams recalled. He knew that IMS needed powerful CAD/CAM software to work alongside its three-axis CNC milling machines and two-axis CNC lathes, as the limitations of manually writing G-code had begun to rear their heads. The time it would take to accurately program complicated parts by hand was prohibitive, and Williams was aware of the risk of user error.
Williams attended the 1998 International Manufacturing Technology Show (IMTS) to find a solution. There he met Allen Drost Jr., founder of CAD/CAM Solutions, a certified reseller of Mastercam. “Drost came directly to my shop after the event, loaded Mastercam on my computer and ran a part right in front of me. He sold me on the software right there,” Williams says. “With this software, I’m able to take on complex jobs I could never even look at before.”
Over 20 years on, Mastercam has continued to provide Williams and IMS with a competitive edge.
Dynamic Improvements
Several years ago, Williams machined a facial extrusion die for the composite decking industry that would not have been possible without CAD/CAM software. As impressive as it was at the time, however, he believes he could be even more efficient today with some of Mastercam’s newer functions.
“I knew if I could nail down a good tool path, that we could make this part,” Williams says. “It was just a matter of finding it.”
“That was several years ago, and if I were to do this same part today, I would look at different tool paths such as OptiRough for roughing out the part,” Williams says. “Another one of our longtime customers just brought us a job that we’re very familiar with and have done before. This time, though, I said, ‘We’re going to do this differently now,’ because there are so many more tool paths I understand now that can make this easier. The dynamic tool paths have really changed the way I look at some of the jobs we get.”
Mastercam’s Dynamic Motion technology relies on proprietary algorithms to monitor stock material and make immediate adjustments to cutting speed and angle during the machining process. CNC Software, Mastercam’s developer, says these adjustments maximize material removal while minimizing the chance of tool breakage or stock gouges. OptiRough, the software’s method for removing large amounts of material during the roughing stage at previously impossible speeds, is one example of an advanced tool path type created with Dynamic Motion.
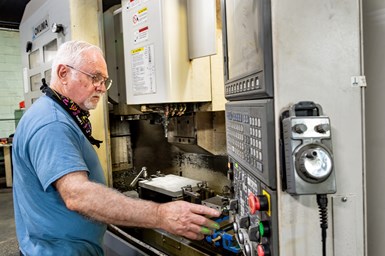
As part of diversifying its clientele, IMS adopted CAD/CAM software to expand the functionality of its three-axis CNC milling machines and two-axis CNC lathes.
Cutting Cycle Times
Even before beginning a job, Williams finds ways to use Mastercam.
“It helps with quoting,” he says. “If I have a complex job — especially one that has a lot of parts to it or maybe quite a few steps and operations — I semi-program it to see my cycle times.”
Williams leveraged this capability when providing a quote for a roller that works in a conveyor system. The v-rollers, as Williams calls them, start as bars of 4340 tempered steel 4 inches in diameter and 21.625 inches long. To create his quote, Williams uploaded the part drawing into Mastercam and programmed it to find his cycle time.
“For roughing, I could have used a traditional turning tool path with extra stepdowns if I’d wanted the cutting path to go in just one direction. With the dynamic tool path, though, it actually went back and forth all the way down. It saved so much time.”
Williams was able to predict a run at 1050 sfm with a 25% stepover. The 15-operation program took less than 11 minutes to rough before it was finished with a standard contour tool path. These shortened cycle times enabled Williams to present a more-than-competitive quote to the customer and win the job.
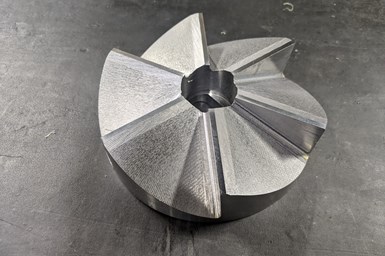
Mastercam’s advanced tool paths enabled IMS to machine this backspot face tool using a three-axis milling center.
Managing New Heights of Three-Axis Complexity
Williams also recalls a recent job IMS undertook to manufacture a backspot face tool. “It’s a tool that is used in the ship building business,” he says. “It attaches to a mandrel and is run to cut a spot face on the back side of a hole.”
“We knew this part would have been easy to do with a multi-axis machine, but we only have our three-axis,” Willaims continues. “So, the first time we looked at it, we just needed to see if we could do it. I knew if I could nail down a good tool path, that we could make this part. It was just a matter of finding it.”
At first, Williams struggled to maximize the tool path efficiency, so he called the specialists at his reseller, CAD/CAM Solutions. Together, Williams and CAD/CAM Solutions president and applications engineer Brian Kadow found a way to machine the part efficiently using IMS’s three-axis milling center.
The part started as a bar of M2 tool steel before it was faced, turned and bored on a lathe. Williams then set up a dividing head indexer tilted to six degrees, set the hole as center zero and incorporated Kadow’s suggestion — a surface high-speed radial 3D tool path — before finishing the part with a contour tool path using a 0.125-inch ball end mill. Machining took approximately eight minutes per tooth. With only six teeth on each part, total machining time per part was well under an hour, an achievement that would have been impossible without CAM software.
Related Content
Tips for Designing CNC Programs That Help Operators
The way a G-code program is formatted directly affects the productivity of the CNC people who use them. Design CNC programs that make CNC setup people and operators’ jobs easier.
Read MoreHow this Job Shop Grew Capacity Without Expanding Footprint
This shop relies on digital solutions to grow their manufacturing business. With this approach, W.A. Pfeiffer has achieved seamless end-to-end connectivity, shorter lead times and increased throughput.
Read MoreAutomated CAM Programming – Is Your Software Really Delivering?
A look at the latest automation tools in Autodesk Fusion 360 software and how forward-thinking machine shops and manufacturing departments are using them to slash delivery times and win more business.
Read MoreCan AI Replace Programmers? Writers Face a Similar Question
The answer is the same in both cases. Artificial intelligence performs sophisticated tasks, but falls short of delivering on the fullness of what the work entails.
Read MoreRead Next
What Sandvik's Mastercam Acquisition Means For Users
While Sandvik says it plans to give recent acquisition Mastercam independence and keep its software platform-agnostic, the company also plans to leverage its new reach into the small to medium manufacturers to cross-sell tools.
Read MoreTool Libraries and Simulations in CAM Software Accelerate Cycle Times
Schupan Aluminum was able to reduce its CNC machining cycle times and perform complex five-axis work through Mastercam’s toolpaths and advanced features.
Read MoreBoost Metal Removal Rates with Constant Chip-Load Machining
The benefits of constant chip-load machining have been known for a while, but efficiently programming the toolpaths was impractical for most shops. However, new CAM technology makes the process easy, and the improvements in machining productivity can be dramatic.
Read More