Mill-Turn Enables Complete Machining of High-Precision Parts
WFL’s Mill-turn machines have enabled Wittmann Battenfeld to combine milling, turning and boring operations for increased process flexibility and production efficiency.
Share




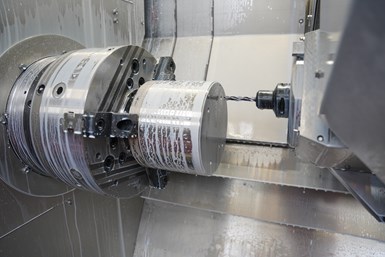
The M30’s standard milling spindle design permits coolant pressure up to 150 bar while also enabling high coolant flow through the spindle. This combination works toward stability of the machining process. Photo Credit: WFL Mill-turn Technologies
The machines that form free-flowing plastic into products that are used around the world require sophisticated parts, complex processes and special expertise. Wittmann Battenfeld’s injection molding machines can fulfill the machining portion of this requirement, and have done so for many industrial, medical and consumer clients.
The Wittmann Group consists of two main divisions: Wittmann Battenfeld and Wittmann. Over 2,200 employees around the world work for the Wittmann Group, which is active in industries such as automotive, medical technology and packaging.
Wittmann Battenfeld offers a diverse range of servohydraulic and electric machines — which can be either horizontal or vertical, depending on the customer's needs. Wittmann's product range includes robots and automation systems, material supply systems, dryers, gravimetric and volumetric dosing units, granulators, and tempering and cooling equipment. The two divisions complement each other to provide customers with complete solutions.
Complete Mill-turn
Wittmann Battenfeld took its first step toward complete machining in 1993, with the purchase of an M70 Mill-turn from WFL Mill-turn Technologies, followed by the purchase of an M50 Mill-turn in 1995. These machines combined turning, drilling and milling operations to improve production efficiency, reduce lead times and maintain process flexibility.
Wittmann Battenfeld soon added M60, M65 and M40 Mill-turn machines, which are all in use today. When time came to replace the original M70 and M50 in 2020, the company immediately turned to WFL again and purchased a new M30 Mill-turn. In addition to accuracy, Wittmann Battenfeld based its decision on WFL’s service team.
“The WFL service team have always been excellent in terms of speed and reliability,” says Martin Gorzolla, head of production at Wittmann Battenfeld. “We’ve been very pleased with the machines over the years, so we didn’t even think about switching to another provider.”
Complete for Many Parts
WFL’s Mill-turn machines can fully machine Wittmann Battenfeld’s range of parts, including screw tips, the plasticizing unit, captive C-washers, hollow shafts, struts and many other workpieces.
"We use these machines for anything that needs to be ultra-precise,” says Christian Grafl, head of maintenance. “We usually only need one of each component that we produce for our injection molding machines. Our products are highly customized, so we don't have any big batch sizes. Everything must be ready just-in-time."
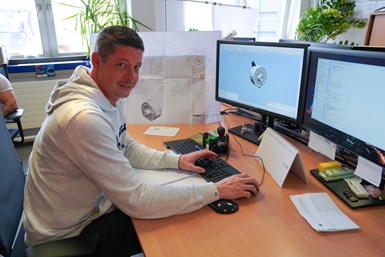
Wittmann Battenfeld has tasked four employees with programming different components in EXAPT PLUS. Photo Credit: WFL Mill-turn Technologies
Not only are the company’s production and assembly departments set up to handle just-in-time customization, Wittmann Battenfeld’s programming team is highly flexible, too. The programming team uses the EXAPT Plus programming system to quickly apply CAD data and create and realistically simulate the program. Thanks to the optimized post-processor, the programs are automatically converted into machine-readable programs and sent to a PC directly next to the active machine via the internal network. The machine operator calls up the jobs, loads the program into the machine's NC controller and — if they are not already in the magazine — orders the required tools from the warehouse via the internal tool management system. The different WFM machines can produce parts with diameters of 85 mm to lengths of 4,200 mm.
"This has allowed us to reduce machining times by around 20%,” Gorzolla says. “A real advantage when it comes to highly efficient production."
WFL’s Mill-turn machines can fully machine Wittmann Battenfeld’s range of parts, including screw tips, the plasticizing unit, captive C-washers, hollow shafts, struts and many other workpieces.
Making Parts With the M30
Wittmann Battenfeld’s new M30 Mill-turn boasts a milling power of 20 kW and is able to machine workpieces up to a maximum diameter of 520 mm and a maximum machining length of 2,000 mm. While the company continues to manufacture its different workpieces in single-part batches, it still finds the M30 impressive in its stability, reliability and precision.
Wittmann Battenfeld says the M30 has performed well on all machining tasks requiring 4,000 or 9,000 revolutions per minute on the main drive and turning-boring-milling unit. The turning-boring-milling unit’s strong gear spindle and backlash-free B-axis have enabled the use of large drills and milling cutters — thereby permitting the use of high feed rates with a large cutting depth. Stability is key to Wittmann Battenfeld’s operations, and the company says the M30 achieves the required level of stability thanks to a solid slant bed made of gray cast iron and WFL's standard axis arrangement, which directs the main cutting forces vertically into the bed. Extra-wide guide spacing, large guides and minimal distances between the machining point and the guides ensure stable behavior during difficult cuts as well as thermal stability for high-precision machining. A fixed, completely smooth guide plate on the lower slide maintains optimum chip flow. The company also achieves tight tolerances across all angles thanks to the high-precision, stable B-axis, which uses a direct measuring system and additional mechanical indexing through a Hirth coupling. Wittmann Battenfeld generally uses machines with a tailstock and a stable, steady rest slide with an automatic self-centering steady rest. This configuration offers great flexibility and enables machining of a wide range of workpieces with little changeover work.
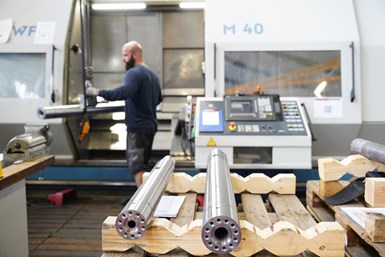
Wittmann Battenfeld currently uses four different mill-turn models from WFL. The M65 and the M40, the latter of which is pictured here, are mainly used for manufacturing wave-shaped workpieces. Photo credit: WFL Mill-turn Technologies
A 40-position disc magazine provides tool stock at the machine. For its M30 Mill-turn, Wittmann Battenfeld opted for a Capto C6 tool system, which uses highly stable and precise boring bars with C6 couplings. The company’s particular M30 is compatible with tools up to 450 mm long, but WFL says that it also offers the machine in configurations with greater magazine capacities and maximum tool lengths.
Wittmann Battenfeld uses an 80-bar coolant pump for the M30’s wide range of internal machining operations. The standard milling spindle design permits even greater pressures, up to 150 bar, and ensures high coolant flow through the spindle. These design elements lead to a noticeable improvement in chip breakage, chip removal and process reliability for all drilling operations. WFL also has a reliable coolant interface for the tool, as well as matching hardware components such as high-pressure coolant pumps, microfilters and additional cooling devices. Alongside the time savings, WFL says this coolant system improves process reliability, surface quality and control of chip removal while reducing unwanted workpiece heating to a minimum.
Related Content
Machine Tool Drawbar Made With Additive Manufacturing Saves DMG MORI 90% Lead Time and 67% CO2 Emission
A new production process for the multimetal drawbar replaces an outsourced plating step with directed energy deposition, performing this DED along with roughing, finishing and grinding on a single machine.
Read MoreSwiss-Type Control Uses CNC Data to Improve Efficiency
Advanced controls for Swiss-type CNC lathes uses machine data to prevent tool collisions, saving setup time and scrap costs.
Read MoreMultitasking Machines Cut Days From Shop’s Setups
Adopting WFL Millturn machines enabled BWXT to condense operations and setups while also providing a simple way to simulate and secure processes.
Read More5 Tips for Running a Profitable Aerospace Shop
Aerospace machining is a demanding and competitive sector of manufacturing, but this shop demonstrates five ways to find aerospace success.
Read MoreRead Next
Turn-Mill Machining Tech Improves Industrial Motor Performance
By replacing a welding process to create rotor cooling channels with multitasking machining from a solid forging, Siemens Norwood has realized improved induction motor vibration qualities and much faster overall rotor production times.
Read MoreTurn-Mills: Being About the B-Axis
With the addition of powerful B-axis milling spindles and automatic toolchangers, turn-mills combine the best of milling and turning worlds.
Read MoreThe Benefits of Horizontal Turning on a Mill-Turn Machine
A mill-turn machine that can rotate a large, bell-shaped workpiece in a horizontal orientation enabled this manufacturer to hit tight tolerance and cost targets. Minimizing non-value-added time and running lights out were also essential for success.
Read More