How Manufacturing Data Can Save the World
Digital spaces rooted in real-world sensor data help scale big ideas and move humanity toward a more sustainable, autonomous future.
Share



In the summer of 2019, Ola Rollén, President and CEO of Hexagon, proclaimed that environmental sustainability is not a barrier to business, but the greatest business opportunity of our age. This past June, returning to the same stage at the annual HxGN Live conference in Las Vegas, Rollén doubled down. “What stands in the way becomes the way,” he said, quoting Roman emperor and philosopher Marcus Aurelius in an outline of how efforts to make sustainability profitable have accelerated despite more than two years of pandemic-related disruption.
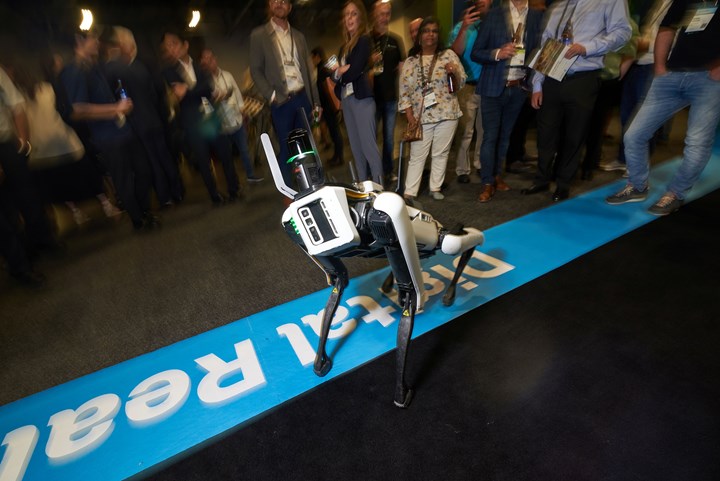
“Spot,” the quadruped robot “dog” from Boston Dynamics, is the first autonomous platform to be fitted with a Leica BLK ARC laser scanner, which uses real-time LiDAR scanning and SLAM tracking for mobile mapping of any 3D space, from solar fields to building interiors. BLK2FLY, a drone-based system, scans from the air. Photo courtesy of Hexagon.
In this case, “what stands in the way” is industry’s accountability for its impact on the environment. Turning this perceived burden into a business opportunity is all about reducing waste, which Rollén says robs roughly 20% of every dollar spent in discrete manufacturing. The big idea is that iterating and optimizing in virtual space first can turn that waste into revenue while simultaneously minimizing the use of our planet’s resources.
As a developer of reality-capture, simulation and automation technology that fuels not only smarter factories, but also smarter cities, smarter mines and even self-driving vehicles, Hexagon is ideally positioned to serve such a need. However, recent activities suggest that the global conglomerate sees its mission as more than supplying the necessary technology. Hexagon also aims to take an active role in applying it, whether via its own initiatives or through direct support of entrepreneurs and startups seeking to scale big ideas.
Consider the recent investment in a 40-hectare solar farm in Archidona, Spain. The goal of this growing venture — which is among the first for R-Evolution, a Hexagon subsidiary launched in 2021 specifically to accelerate sustainable (and profitable) transition — is not to get into the solar energy business. Rather, it is to help that business grow in a more general sense by building a blueprint for others.
Specifically, the company is putting data to work by employing camera- and laser-based scanners to conjure a virtual version of the entire site from thin air. Faithful to the point of replicating individual components of individual panels, this artificial reality leverages a varied stack of artificially intelligent simulation software to predict and optimize outcomes. Examples include improving maintenance, aiding inspection, detecting anomalies and even determining how to angle the swiveling panels into the wind for efficient cooling.
With costs projected to drop and capacity projected to expand, solar energy is not a sector that appears to need any help. However, that is precisely the point. With humanity essentially running out of time, R-Evolution aims to identify what already works, then accelerate the growth trend to speed our transition to a more sustainable economy. CEO Erik Joseffson calls his business unit “the thumb” of Hexagon, in that it pulls resources and expertise from the others as-needed to meet this goal by, as he puts it, “turning talk into action.” The end result is generally a “smart digital reality” like the one created for the solar field project — that is, realistic, self-evolving simulations that essentially add autonomy to the digital twin.
Other examples of R-Initiatives include a pioneering green hydrogen plant in Australia and a collaborative effort with an nonprofit organization to map C02-soaking sea grass meadows in the Caribbean, with the eventual goal of creating a system of carbon credits. However, R-Evolution’s latest efforts evidence a recognition that some of the best ideas start small. Just a few months prior to the conference, the division announced a new venture capital arm, R Ventures, that directly supports promising green-tech startups. In return for equity in these startups, the company provides seed funding or in-kind technology, as well as access to its broad market access and range of expertise.
For another new initiative, supporting entrepreneurs and startups constitutes the entirety of the mission. Created earlier this year, 6th Sense is a competition that invites startups to present their ideas before a panel of industry experts, who choose which proposals to back with funding, technology and the expertise required to scale. According to the company, a primary differentiator from other incubators and business accelerators is a focus on ideas already proven to be successful (for example, candidates must have series A or similar level of funding).
In keeping with the company’s broader mission, candidates must also focus on sustainability directly, or at least the technologies driving the digital revolution — namely, those involving machine learning, sensors and/or robotics. The first two winners appeared at HxGN live. SmartParts embeds digital barcodes directly into raw material to enable full product-lifecycle traceability for 3D printed parts (and, perhaps eventually, other materials for other manufacturing applications). The second, RIIICO, offers facility-layout design software with an intuitive, essentially “drag-and-drop” interface that virtually anyone can use.
For those in the business of CNC machining, helping to save the world with data does not require such revolutionary ideas, nor any direct involvement in sustainability projects. In fact, “what stands in the way” could be as fundamental as the collection of quality data from machined parts. Rather than a necessary evil, this process could become a driver of productivity, whether for offset-correcting feedback loops or the use of digital twins for more comprehensive process optimization before machining begins.
Feedback loops aside, the more manufacturers seek to make what stands in the way become the way, the more we all stand to gain, and not just in a financial sense. It’s time to buy in.
Related Content
How to Accelerate Robotic Deburring & Automated Material Removal
Pairing automation with air-driven motors that push cutting tool speeds up to 65,000 RPM with no duty cycle can dramatically improve throughput and improve finishing.
Read MoreManaging Coolant with Skimmers, Refractometers and More
Bacteria-infected coolant harms machines and sickens machinists. Coolant management technologies like skimmers and automated systems counter this tendency.
Read MoreInside the Premium Machine Shop Making Fasteners
AMPG can’t help but take risks — its management doesn’t know how to run machines. But these risks have enabled it to become a runaway success in its market.
Read MoreIncreasing Productivity with Digitalization and AI
Job shops are implementing automation and digitalization into workflows to eliminate set up time and increase repeatability in production.
Read MoreRead Next
Digital "Fingerprints" Put Twins in Perspective
Unique identifiers keep the digital thread intact through design, production and quality control.
Read MoreProbing Feedback Keeps CNC Machining On Track
CNC machine tools that operate like self-contained, automated smart factories can be an introduction or an addition to digital manufacturing workflows.
Read MoreSetting Up the Building Blocks for a Digital Factory
Woodward Inc. spent over a year developing an API to connect machines to its digital factory. Caron Engineering’s MiConnect has cut most of this process while also granting the shop greater access to machine information.
Read More