Share



Jack Burnie, who has been a machinist with KCS Advanced Machining Services since 2019, has taken on not only five-axis programming duties for the company, but is also spearheading its new inspection lab.
Kyle Szczypienski earned his CNC machining and programming chops at Roush Industries — a company that was first made famous for its custom automotive parts — shortly after graduating with an associate degree in automotive and diesel technologies in 2006. At Roush, Szczypienski (pronounced Shuh-Pin-Ski) was first assigned to the company’s shop floor to learn about feeds and speeds, depths of cuts and programming strategies via direct experience with an array of 30 CNC machines. But Szczypienski’s acute interest in programming was hard to keep secret, and it quickly earned him the dubious honor of writing code for all 20 of the plant’s other machinists on a wide variety of machine tools.
Kyle Szczypienski, founder and owner of KCS Advanced Machining Services, sets up a pallet on one of the company’s new Matsuura five-axis machines.
It was a 1969 Pontiac Lemans, though, that ultimately led the young Szczypienski toward opening his own shop. Still living at home where he kept the old dragster parked in front of the house — a yard decoration that his parents failed to appreciate — Szczypienski needed a place to work on restoring it to its former glory. He purchased an old building on the outskirts of Detroit where he planned to work on the Lemans and possibly establish a side hustle fixing racecars.
Sitting around one night in the late aughts with little to do, Szczypienski found a Fadal machining center listed on eBay for $17,000. “I can afford that!” he thought to himself as he placed his bid — and won.
While Szczypienski attributes much of his early success to luck, anyone who knows him could have predicted what happened next. His aptitude and reverence for CNC programming and machining started to become well known in local circles. He began to use Instagram to share success stories through video and images of some of his favorite machined parts. Word got around and he began gaining customers — enough customers to justify leaving Roush in 2013 and begin working for himself at his newly christened machine shop, KCS Advanced Machining Services.
I visited KCS last year after receiving an email from Gordon Cole, the company’s vice president of strategy and business development, who had a good story to tell about how the shop leaned heavily on automation to deal with challenges related to skilled labor, long setup times and competition from automotive OEM suppliers in and around Detroit. But a tour of the shop revealed something else that stands out, too: Almost all of KCS’s employees are skilled CNC programmers.
They are also young. Except for Gordon Cole, every single employee is less than 40 years old. On top of that, this young, talented staff is almost fearless when it comes to five-axis machining, an approach that has enabled reinvesting profits back into the business — particularly in automation — at a dizzying pace for a small but growing shop.
The staff of KCS Advanced Machining Services. From L to R: Gordon Cole, Kyle Lindsay, Matt Sweeney, Jack Burnie, and Kyle Szczypienski.
Into the Night
In the fall of 2019, KCS was hustling to stay on top of a heavy workflow comprised mainly of prototype work for the automotive and aerospace industries. Much of the work was highly complex, including NASA-commissioned parts for the Artemis space program as well as a multi-port, multi-faceted, 3D scalloped hydraulic manifold for hydrofoil sailboats. KCS’s existing five-axis machines, including two Hurco VMX models and a Bridgeport 5ax, were taxed to the limit, largely due to the outsized amount of time dedicated to setup. With one operator running two machines, the shop had reached a limit of 16 hours of machining time per day.
A multi-port hydraulic manifold for hydrofoil sailboats machined at KCS Advanced Machining Services.
Pallet changers changed everything. The first was a four-pallet automation system for a new Matsuura Maxia MX-520 five-axis machine, which KCS installed in September of 2019. This was followed recently by the installation of a Matsuura MAM 72-35V — a 32-pallet system with 320-tool capacity.
The flexibility to load different pallets with different parts and run them through the night has changed the nature of the business. Although the shop still focuses on prototypes, KCS now can shift into low-to-medium production quickly, even for complex parts. Szczypienski and Cole say this capability is particularly valuable when dealing with customers that represent startup businesses — businesses that offer opportunities for KCS to grow and mature alongside them.
A Team of Programmers
None of this would be possible, of course, without what Szczypienski refers to as the “force multiplier” that allows KCS to be a five-axis shop. That force multiplier is Open Mind Technologies’ HyperMill.
This software's simulation and collision avoidance features are crucial to taking advantage of the constantly shifting orientation of a five-axis machine’s spindle in relation to the workpiece and the rotary axis, Szczypienski says. Previewing operations in advance was especially critical for the hydraulic manifold parts, each of which is jam-packed with more than half a dozen crisscrossing hydraulic fittings.
“Most CAMs, when you’re looking at your stock, you just draw a rectangle and place the cutter path inside of it,” Szcypienski says. “That might not be so bad if you're machining from a vertical orientation and your material is square. But when you’re machining most of the material away from your arbitrary top face on a five-axis machine, and then tip the workpiece 45 degrees, your top face is skewed. You're going to machine air until you get to metal, or you're going to end up putting yourself in a really vulnerable spot.”
Mentally keeping track of the stock orientation is often very difficult, he says, especially with a sophisticated part. “You're going to not see something coming and you're going to break an end mill or worse.”
While Szczypienski is KCS’s most experienced programmer, most of the shop’s employees are capable of programming five-axis work, including machinists Matt Sweet and Jack Burnie, both of whom joined KCS in the last two years.
“You really just can't get discouraged by the scope of the work,” Burnie says. “Programming is more important here than in the shops I was in before. Some of these parts are intimidating, but once you get to the end you realize it's really not that bad. You do your due diligence on the machine and take it piece by piece and get through it.”
Why Do They Come to Us?
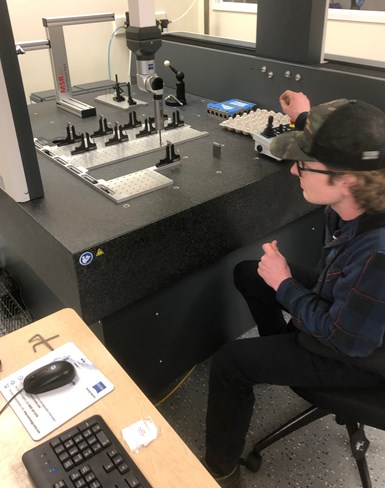
KCS machinist Jack Burnie operates the company’s Zeiss Contura CMM in the new inspection lab.
Of course, the complexity inherent with being a five-axis shop also provides an incentive to push those capabilities ever further. KCS is taking that challenge to heart with its push toward AS9100D certification — a goal that required the company to apply new standards to its inspection processes, including the purchase of a Zeiss Contura G2 CMM and the building of a new, dedicated inspection lab, as well as implementing quality management system (QMS) processes into its daily operations.
“We are developing more into the low to medium volume work with a mix of sophisticated work that a lot of shops won't touch,” Gordon Cole says. “What are the things that those customers value? Why do they come to us? We're a humble little shop with a young staff, right? Why do they come to us? Well, we give them the quality and a high degree of sophistication that they can’t find elsewhere, and we're planning our business strategically to track along with those of our larger customers. We're not just buying equipment. It's all part of a plan, and that’s what we are executing.”
Related Content
Lean Approach to Automated Machine Tending Delivers Quicker Paths to Success
Almost any shop can automate at least some of its production, even in low-volume, high-mix applications. The key to getting started is finding the simplest solutions that fit your requirements. It helps to work with an automation partner that understands your needs.
Read MoreFour-Axis Horizontal Machining Doubles Shop’s Productivity
Horizontal four-axis machining enabled McKenzie CNC to cut operations and cycle times for its high-mix, high-repeat work — more than doubling its throughput.
Read MoreHow to Accelerate Robotic Deburring & Automated Material Removal
Pairing automation with air-driven motors that push cutting tool speeds up to 65,000 RPM with no duty cycle can dramatically improve throughput and improve finishing.
Read More3 Ways Artificial Intelligence Will Revolutionize Machine Shops
AI will become a tool to increase productivity in the same way that robotics has.
Read MoreRead Next
Matsuura Five-Axis Machines Give Shop Unattended Capacity
Matsuura five-axis machines drastically increased Flying S’ process reliability in making complex aerospace parts, in one example leading to over 90% first part integrity on first machining attempts.
Read MoreNo Such Thing as Luck: A One-Person Shop Owner’s Success Story
You could say he’s a lucky Guy. He has the ideal setup for a moonlighting at-home-machinist: The perfect location, the perfect day job, and a double-threat skill set that allows him to hire himself for prototyping and low-volume production work. But Guy Driscoll’s biggest talent might be creating his own luck.
Read MoreOpen Mind Technologies' HyperMill CAM Software Enables Real-Time Synchronization and Simulation
EMO 2019: Open Mind Technologies’ HyperMill CAM software was developed with Industry 4.0 in mind.
Read More