Share


Hwacheon Machinery America, Inc.
Featured Content
View More
Takumi USA
Featured Content
View More



ECi Software Solutions, Inc.
Featured Content
View More

This content originally appeared in our sister brand, Production Machining. For more insights and information about precision machining, visit productionmachining.com.
In machine shops across the globe, there is a definite trend toward implementing multitasking machines for the purpose of completing parts on one piece of equipment. This efficient machining process eliminates the need to run parts across multiple machines, which saves equipment floor space, setup time and labor.
Fuji Machine America Corp., a creator of automated machine tools, combines the machining and robot experience to present a new automated multitasking machining solution with an integrated robot.
“Any shop that can benefit from product completion in one machine is the ideal candidate for the Gyroflex,” says Frank Tortorich, vice president of sales and service at Fuji Machine America. He explains that the machine handles the process from the beginning with the raw material, all the way through to a finished part, including measuring and testing for quality.
By using Fuji automation, the Gyroflex offers the size, rigidity and productivity necessary to handle simple to complex workpieces. Photo Credits: Fuji Machine America Corp.
The machine’s dual-opposed main spindles for simultaneous operation, a B-axis milling tool spindle, multiple workflows, tooling capacity, integrated automation, and rigidity are among the key features of the Gyroflex.
Dual-opposed spindles. The machine’s opposed twin spindles positioned on Z-axis slideways are equal in size and machining capability. They can perform the same operations (op-10a/10b) or can pass a part from the first spindle to the second while maintaining positioning accuracy, thereby performing op-10 and op-20. If the application calls for two separate operations, a partition inside the machine is used to create two separate workzones. Also, the Z-axis slide can move at high speeds to reduce loading time to the second spindle.
B-axis milling spindle. The B-axis milling spindle is mounted on rigid X- and Y-axis boxway slides. The spindle accesses the two Z-axis spindles and swings up to 190 degrees, enabling different types of operations, including turning, drilling and part probing. Further, the B axis and the tool are clamped by curvic coupling, resulting in accurate index location with the turret precisely centered, according to the company. Gyroflex also comes standard with Sandvik Coromant Capto C6 toolholder interfaces, which provide virtually unlimited combinations of tooling for all different types of applications, Tortorich explains.
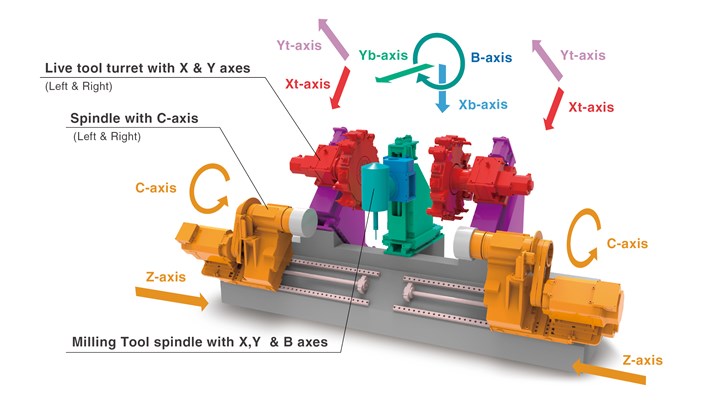
The machine’s opposed twin spindles positioned on Z-axis slideways are equal in size and machining capability. The B-axis milling spindle is mounted on rigid X- and Y-axis boxway slides. The spindle accesses the two Z-axis spindles and swings up to 190 degrees, enabling different types of operations, including turning, drilling and part probing. Further, the B axis and the tool are clamped by curvic coupling.
Multiple workflows. Various workflows are accommodated on this machine, depending on the needs of the machine shop. Left to left, right to right, left to right and right to left are all available. The company says the machine’s multiple workflows enable flexible part processing and reduced setup/changeover times.
Tooling capacity. Both live tool turrets hold 15 tools, while the automatic tool changer (ATC) — located at the top of the machine — holds 40 tools. The ATC holds multiples of the same tool for low-mix, high-volume applications where a tool might break or wear and need replacement. And, for high-mix, low-volume applications, it can hold many different types of tools for quick tool replacement.
Fuji’s three-axis gantry robot for parts handling accesses peripheral devices at the left and right sides of the machine.
Integrated automation. The company’s own three-axis gantry robot is integrated in the machine for unattended parts handling. The robot’s two arms — primary and secondary — access peripheral devices at the left and right sides of the machine, the company says.
The hydraulic robot chuck enables stable clamping and workpiece handling with minimum space requirements. The thin-type, double-hand design, according to Tortorich, offers flexibility and easy setup of workpieces as well as handling that requires minimum space.
The company offers an optional robot chuck clamp confirmation sensor on the Gyroflex. This is said to ensure that the workpiece is clamped properly in the robot hand before loading or unloading the machine for a smooth and quick automation transfer process.
Rigidity. This machine is extremely rigid with a solid one-piece casting base design and box ways for both turrets, and X-, Y- and B-axis slideways, the company says.
Fuji Machine America Corp. | fujimachine.com
Related Content
Integration, Automation and Green Tech Highlight JIMTOF 2022
Known as one of the largest machine tool trade shows in the world, the Japan International Machine Tool Fair (JIMTOF) has a reputation for being a machining technology show more than a machine tool sales event. And this year’s show in Tokyo — the first in-person Japanese machine tool trade show in four years — did not disappoint.
Read MoreBuilding Machines and Apprenticeships In-House: 5-Axis Live
Universal machines were the main draw of Grob’s 5-Axis Live — though the company’s apprenticeship and support proved equally impressive.
Read MoreHow to Meet Aerospace’s Material Challenges and More at IMTS
Succeeding in aerospace manufacturing requires high-performing processes paired with high-performance machine tools. IMTS can help you find both.
Read MoreDigitalization and Done-In-One Reign Supreme at BIEMH 2024
European manufacturers may have a different balance of markets than their U.S. counterparts, but the practical challenges they must overcome are often similar — as are the solutions.
Read MoreRead Next
5 Rules of Thumb for Buying CNC Machine Tools
Use these tips to carefully plan your machine tool purchases and to avoid regretting your decision later.
Read MoreRegistration Now Open for the Precision Machining Technology Show (PMTS) 2025
The precision machining industry’s premier event returns to Cleveland, OH, April 1-3.
Read MoreBuilding Out a Foundation for Student Machinists
Autodesk and Haas have teamed up to produce an introductory course for students that covers the basics of CAD, CAM and CNC while providing them with a portfolio part.
Read More