Share



After a short introduction, Grob let the testimonials and machines do the talking at its 5-Axis Live event in Bluffton, Ohio, on Aug. 22. The event largely focused on the company’s line of universal five-axis machines, with demonstrations showcasing applications for different models and customizations. The company also conducted tours of the factory floor, where Grob produces machines for the U.S. and Canadian markets, and gave attendees access to its service and apprenticeship teams to discuss the company’s internal successes and outreach.

Grob’s universal machines were the stars of the show at 5-Axis Live, but the company also pointed out examples of its other machines during a tour of the shop floor, where they were used to manufacture Grob machines for future customers.
Universal (Machine) Praise
Grob’s demonstrations of its universal five-axis machines showcased various machine configurations, from the compact G150 to three varieties of the G350 with different tables to the large G750T mill-turn machine. The sample parts were equally varied, with aerospace components, molds and 3D-printed medical parts.
These machines and others were also on display during a tour of the factory floor. According to Mike Hough, sales engineer at Grob, the Bluffton facility makes about 85% of parts for its machines in-house, and many of the machines used to do so are Grob machines. Of the remaining 15% of parts, some are outsourced to specialized facilities, while others are produced at different Grob factories. Notably, this is the case for the machine spindles, which are produced at Grob’s central factory in Mindelheim, Germany, and stocked at the Bluffton facility as assembly parts for new machines and as replacement parts for older machines.
In addition to its live demonstrations, Grob enlisted several customers to discuss their use cases and successes with the machines. Robert Geoffroy, vice president of engineering at Davis Manufacturing, and Don Stankus, vice president of Operations at Arch Medical Solutions, both had high praise for Grob’s installation team, reporting that Grob’s team swiftly set up their universal machines and provided useful five-axis training and tips to shopfloor operators. After setup, Geoffroy says, the horizontal orientation of the machines aided Davis Manufacturing in managing chips while performing simultaneous five-axis work on complex missile housings. Stankus, meanwhile, says the G350 and G550 machines Arch uses consolidated part operations, in some cases cutting cycle times in half.
Edwin Gasparraj, founder of Six Digma, says his company’s consulting efforts are much stronger with Grob machines: One company was able to tighten tolerances from 0.01 inch to 0.001 inch while improving its yield rate from 40% to 98%. John Michalko, associate general manager at FPD Company, meanwhile, gave high praise to the machines’ pallet setups and found their Z-axes invaluable when machining aerospace and orthopedic parts.
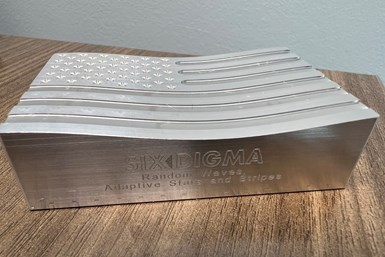
Sample parts made using the Grob machines included impellers, orthopedic implants — and an American flag machined into a block. Six Digma leveraged advanced programming features and the accuracy of the Grob machines to machine parts with unique wave forms for each part.
Service Calls
The presenters also praised Grob’s service team, which was revamped about four years ago. Today, the team doesn’t just step in when machines show problems, but proactively assists customers by informing them of machine features and Grob-related solutions to ensure uptime and successful machining.
The team relies heavily on remote diagnostics, which Grob after sales consultant Jon Keske says speeds up service times and eliminates about 80% of in-person visits to shops. He also says the Grob-NET4Industry package includes some predictive maintenance capabilities, with monitoring of axis performance and ball screw conditions, both of which can be sent to a cloud-based data repository for analysis and evaluation.
To meet cybersecurity protocols, the Bluffton facility includes a dedicated room that follows ITAR guidelines, routing all remote data from ITAR-certified shops there. For shops that cannot use cloud-based systems at all, Grob also supplies its machines with remote diagnostic toggles to turn off this feature.
Grob’s representatives at the event describe the G550 as an all-rounder machine that has gained popularity in the aerospace market due to its ability to rough while providing an acceptable surface finish.
Rhodes to Manufacturing
In contrast to the service department, Grob’s apprenticeship program has a long history. This program is in its 33rd year and has seen class sizes of about 40 people for several years running. While this doesn’t fulfill all the company’s staffing needs — it hired 150 employees in the last 12 months alone — retention is high enough that former apprentices make up a large portion of the company’s payroll. Out of 825 employees based out of the Bluffton facility, 284 are past or current apprentices.
To add further context, the program lasts four years and boasts a five-year retention rate of 85% and a 10-year retention rate of around 70%. Recruitment starts early, with the program’s admin teams doing general STEM outreach to middle schools before following up with tours, job shadows and high school visits in a 50-mile radius of Bluffton. Their primary goal is to hook students by dispelling old and inaccurate myths about manufacturing. “Everywhere in the world, manufacturing doesn’t look like it did even 10 years ago,” says Mark Reed, apprentice training supervisor at Grob. Getting parents on board with a manufacturing career path has also proved easier, especially since Grob’s apprentices receive a full benefits package from the start of the program.
Grob’s apprenticeship program takes place over four years. The first two years combine hands-on training at Grob’s facility with instruction at Rhodes State, a community college in nearby Lima, Ohio. The first 20 weeks of this period serve as a “basic training” crash course that introduces students to the basics of machining. After this point, the cohort splits into mechanical and electrical groups for the remainder of the apprenticeship. Apprentices receive their associate degree during their second year, then spend the next two working toward a journeyperson’s certification.

5-Axis Live also boasted a significant third-party technology provider presence. Representatives from Siemens, Open Mind and Seco all spoke during the presentations, while an even wider selection of partner companies maintained busy booths near the demonstrations.
McKenzie Chishko, training apprenticeship coordinator at Grob, says a large part of the company’s success with apprenticeships is that Grob’s flagship German team was quick to fund the program from its earliest days, reflecting the fact that apprenticeships are a vital part of German manufacturing culture, and thus, part of Grob’s DNA. The company’s close relationship with Rhodes State is equally vital — Grob’s program supplies the vast majority of Rhodes State’s students in the Electro-Mechanical Engineering Technology degree path, and the college both handles paperwork for the journeyman program and adjusts its curriculum to ensure its graduates have the skills they need to succeed at Grob.
Grob plans to continue expanding its program and is currently planning to construct a new building on the Bluffton campus to serve as a hub for apprentices. With the new building, the company plans to enlarge its apprenticeship cohorts to around 60 apprentices each year. It also plans to investigate a potential 2+2 bachelor’s degree program, partnering with both Rhodes State and Miami University in Oxford, Ohio.
Related Content
In Moldmaking, Mantle Process Addresses Lead Time and Talent Pool
A new process delivered through what looks like a standard machining center promises to streamline machining of injection mold cores and cavities and even answer the declining availability of toolmakers.
Read MoreFinding the Right Tools for a Turning Shop
Xcelicut is a startup shop that has grown thanks to the right machines, cutting tools, grants and other resources.
Read MoreManufacturing Madness: Colleges Vie for Machining Title (Includes Video)
The first annual SEC Machining Competition highlighted students studying for careers in machining, as well as the need to rebuild a domestic manufacturing workforce.
Read MoreCan Connecting ERP to Machine Tool Monitoring Address the Workforce Challenge?
It can if RFID tags are added. Here is how this startup sees a local Internet of Things aiding CNC machine shops.
Read MoreRead Next
Grob Mill-Turn Machining Center Provides Flexible Performance
The G550T mill-turn universal machining center offers optimized milling and turning performance for a broad range of part materials in one setup.
Read MoreGrob Goes Big on Universal Machining Centers
At an open house in Germany, Grob described its focus on the aerospace market for its line of universal machining centers.
Read MoreThe Benefits of Horizontal Turning on a Mill-Turn Machine
A mill-turn machine that can rotate a large, bell-shaped workpiece in a horizontal orientation enabled this manufacturer to hit tight tolerance and cost targets. Minimizing non-value-added time and running lights out were also essential for success.
Read More