Agile Tooling Prepares Shop for Machining Spaceflight Parts
Big Daishowa’s angle head and milling chucks have enabled Baker Manufacturing to keep up with the tight turnarounds and mystery metals of Blue Origin.
Share




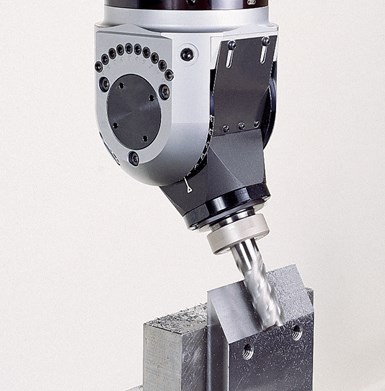
Big Daishowa’s angle head enables Baker to use a three-axis machine to access areas on parts that would have otherwise required a five-axis machine. Photos courtesy of Baker Manufacturing.
Baker Manufacturing needs to be agile, precise and ready to handle materials with unknown chemical makeups — its role as a supplier for Blue Origin spaceflight parts demands nothing less. Owner Tony Baker credits his shop’s success in part to its tooling. “The vast variety of tooling we have in inventory is a result of the agile approach we’ve always taken,” he says. “Waiting six weeks to purchase tooling is usually longer than you get for lead time for the whole job.”
Angling for Success
One of the tools Baker credits with maximizing the shop’s agility is Big Daishowa’s universal angle head. Some complex, closed-angle parts can’t be drilled with a straight-driven motion on the shop’s largest three-axis mill. On the shop’s five-axis machine, the angle head’s high clearance enhances capability to machine pockets.
“We use it mostly for milling and two-inch thread milling, but we’ve found ourselves using it all the time,” Baker says. The angle heads are available in fixed and adjustable forms for a wide variety of angles. A narrow-shank, spherical-lollipop head version has enabled the company to hit vectored holes, using the extra clearance to simultaneously move along the X, Y and Z directions on a large-bed vertical mill where vectoring a tool straight is not an option.
Baker says the angle head also helps with parts that are significantly larger than the travels of the machine. Oftentimes, these parts can’t be tilted to access certain angles or the ends, but the angle head can reach them.
Milling Chucks for Mystery Materials
The angle head has helped Baker Manufacturing stay agile enough to hit its demanding timelines, but Baker himself credits another tool with managing the tight tolerances and difficult materials.
“Blue Origin is sending us Inconels, titaniums, aluminums, even materials that haven’t been invented yet,” Baker says. “We’ll get a sample and all we can know is that it’s high-nickel or something.”
“The vast variety of tooling we have in inventory is a result of the agile approach we’ve always taken,” Baker says. “Waiting six weeks to purchase tooling is usually longer than you get for lead time for the whole job.”
Some of the most unusual materials are 3D-printed metals — almost like forgings — with a very tough, high scale-like finish that needs to be processed to the proper sheen. The combination of higher speeds and difficult metals burns through cutters quickly. Further complicating matters, Baker Manufacturing also uses 0.75”-diameter, 4.125”-long, nine-flute mills that cost hundreds of dollars. Both the length and number of these flutes contributes to higher friction and outward pull.
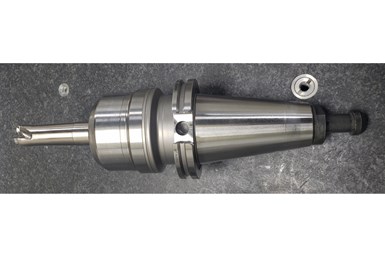
Baker reports the vibration damping of Big Daishowa’s milling chucks has enabled some of its mills to run 20 parts where it previously only ran one.
“You can go through one cutter per part if you’re not doing it right,” Baker says. “It’s all just too expensive. Not to mention, ruining a $500 cutter head and $10,000 part is a bad lesson to have to learn. We decided to seek out something with better balance and vibration damping.”
Baker and his team decided on Big Daishowa’s BCV50-Mega Series milling chucks with Big-Plus dual contact. As the nut of these chucks clamps down, it compresses the bore of the tool holder for high concentricity and rigidity. According to the company, the milling chucks provide more gripping force than collet chucks and less runout than side-lock systems.
“Pullout and slippage are night and day,” Baker says, crediting the milling chucks with enabling his company to use the full nine-flute length. “Plus, because of the vibration damping, one mill is running 20 parts, where it was only running one before. At $400-$600 apiece, that’s an amazing cost savings.”
Related Content
Quick-Change Tool Heads Reduce Setup on Swiss-Type Turning Centers
This new quick-change tooling system enables shops to get more production from their Swiss turning centers through reduced tool setup time and matches the performance of a solid tool.
Read MoreThrough-Coolant System Cuts Nickel-Alloy Cycle Times by 70%
Decker Machine Works recently adopted Rego-Fix’s reCool through-coolant system for ER collets, reducing the cycle times on a nickel alloy job by 70%.
Read MoreRego-Fix’s Center for Machining Excellence Promotes Collaboration
The new space includes a showroom, office spaces and an auditorium that will enhance its work with its technical partners.
Read MoreHow to Mitigate Chatter to Boost Machining Rates
There are usually better solutions to chatter than just reducing the feed rate. Through vibration analysis, the chatter problem can be solved, enabling much higher metal removal rates, better quality and longer tool life.
Read MoreRead Next
Deciding to Specialize as an Aerospace Supplier
Formerly a job shop serving a diverse local customer base, IPG responded to industry changes by transitioning into becoming an aerospace supplier. Here are the steps the shop is taking to make that change, including adding equipment and implementing plans for quality and marketing.
Read MoreThe Benefits and Limitations of Machining With an Angle Head
Far from being outdated by the latest machine tool technology, angle heads often prove an ideal complement by pushing done-in-one capabilities even further. Proper application, however, requires attention to their limitations as well as their benefits.
Read MoreWhat To Consider When Adding Angle Heads
Angle heads can enable a three-axis machine tool to be more versatile. That said, this shop explains that there’s more to getting started using them than simply loading them into a machine’s spindle.
Read More