A Marked Part Is Never Lost
Laser engraving parts has become an essential process at MRS Machining. Marked parts mean that both the manufacturer and the customer are protected from misidentifying parts.
Share



Laser marking parts was not a standard practice for MRS Machining — that is, until a customer rejected a run of parts. This surprised shop owner, Matt Guse because the parts had passed quality control, the shop had done this job before. Further investigation revealed the true nature of the problem: a case of misidentification. These parts had not, in fact, been produced by MRS Machining, and those that did come from the shop were well within specification. After some investigation, Guse discovered the rejected parts were not produced by MRS Machining and his parts were in spec and on time. As a quick solution to this problem, the shop engraved a small “M” on a non-critical part face to differentiate its work from alternative suppliers. The success of this trial led to Guse to believe that part marking would become standard practice for the shop.
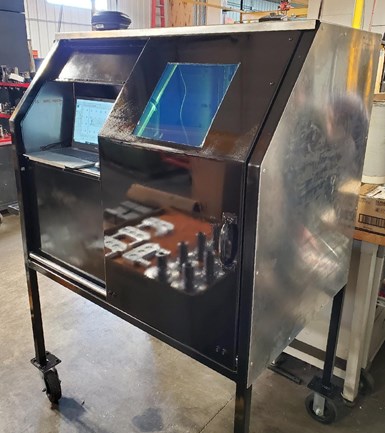
The mobile laser engraving station at MRS Manufacturing has become an essential component of its manufacturing process. Keeping the unit on wheels enables moving the machine to the parts, rather than carting parts across the shop.
Photo Credit: MRS Machining
Marking Becomes a Standard Practice
The decision to mark parts is often driven by one of two forces — an internal or external demand. Buyers who are seeking a machine quickly to fill a demand from a customer are less likely to scrutinize the capabilities and specifications of a laser engraver. On the other hand, a shop like MRS Machining that is seeking a laser engraving machine on its own accord — an internal demand — tends to shop around and engage in a longer purchasing process. In fact, MRS sent personnel to the International Manufacturing Technology Show (IMTS) with the express purpose of getting a handle on the who’s who of laser engraving machines.
“Our only concern with the laser engraver is that we want another one. The demand is so high for engraving that the machine can’t go down without creating a backlog.”
After meeting with several vendors, Guse settled on a eCobalt Class IV fiber laser. The machine is a 20-watt, two-axis laser with a manually adjustable Z-axis. These specs represent a modest investment when looking at the spectrum of available models from eCobalt and other companies. After all, Guse was not prepared for how integral the machine would become to the shop. After taking delivery of the machine, the speed in which the shop was able to integrate the new hardware into its workflow surprised everyone. The laser dramatically reduced the time spent engraving parts and produced higher-quality marks than the shop’s CNC machines.
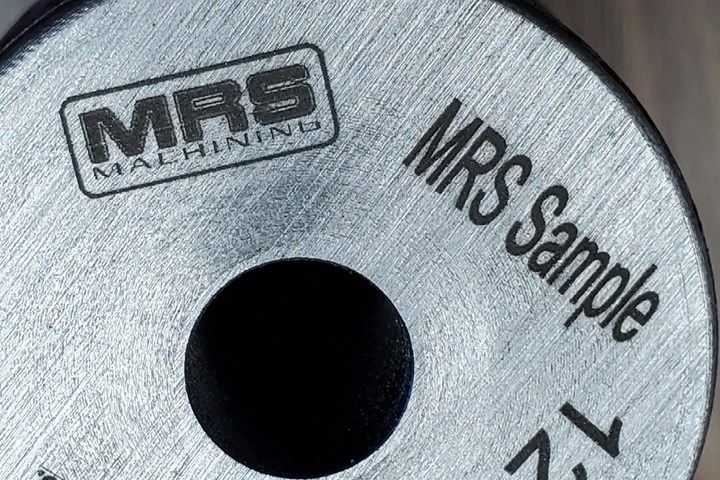
Matt Guse, CEO of MRS Machining, leverages laser engraving as a sales tool. The process is fast enough to engrave a prospective customer’s name and logo on a part in the middle of a meeting.
Photo Credit: MRS Machining
As an example, Guse cites a job in which per-part engraving time dropped from 2 minutes and 10 seconds to 7 seconds. With 1,000 parts to engrave for that job alone, these time savings add up, and the machine paid for itself in two months. “Our only concern with the laser engraver is that we want another one,” Guse says. “The demand is so high for engraving that the machine can’t go down without creating a backlog.”
Beyond a Logo
Capability to quickly tag a part with a logo or customer name. Laser engraving has set MRS Machining apart from its competitors, Guse says. More than one visiting customer has been surprised by the prospect of having parts engraved for little or no additional cost.
In fact, customers and prospects are so enthused by the service that Guse uses it as a sales tool. One customer who visited the shop had never used laser engraving on its parts before, so Guse decided to demonstrate how fast process is. Within minutes, he had created a program on the mobile engraving station and handed the customer a business card with their name on it. This sparked a new conversation about what could be engraved on the customer’s part and ultimately led to the decision to place several additional orders.
Marking attributes like product numbers, purchase orders and lot numbers offers can serve the customer and their production process, not just the manufacturing process at MRS Machining. Guse says that customers will often run with the idea that they are not constrained by the number of characters, resolution of the engraving or other factors that are more typical of CNC engraving.
Future Considerations
Once a shop has brought a laser engraving machine into the production process, the investment becomes an afterthought because of fast the ROI is. At MRS Machining, their investment in a two-axis machine has proven adequate for the time and was critical to get move the shop into laser engraving, but the shop anticipates moving to a three-axis engraving machine to further increase its capacity. MRS is now considering more advanced laser engraving capability. With a three-axis machine, the operator is not required to manually set the Z-axis, further reducing setup time.
For some customers, the engraving on a part has its own specifications. Guse has received orders for engravings that are .010 inch deep, just outside the range that the 20-watt fiber laser is able to obtain. In these situations, MRS Machining has been able to provide feedback to the customer and settled on a more obtainable depth, between .007 to .008 inch deep, or they can tap into a separate vendor that is able to provide the engraving that the customer needs.
Related Content
5 Tips for Running a Profitable Aerospace Shop
Aerospace machining is a demanding and competitive sector of manufacturing, but this shop demonstrates five ways to find aerospace success.
Read MoreHow to Mitigate Chatter to Boost Machining Rates
There are usually better solutions to chatter than just reducing the feed rate. Through vibration analysis, the chatter problem can be solved, enabling much higher metal removal rates, better quality and longer tool life.
Read MoreHow to Determine the Currently Active Work Offset Number
Determining the currently active work offset number is practical when the program zero point is changing between workpieces in a production run.
Read MoreHigh RPM Spindles: 5 Advantages for 5-axis CNC Machines
Explore five crucial ways equipping 5-axis CNC machines with Air Turbine Spindles® can achieve the speeds necessary to overcome manufacturing challenges.
Read MoreRead Next
Building Out a Foundation for Student Machinists
Autodesk and Haas have teamed up to produce an introductory course for students that covers the basics of CAD, CAM and CNC while providing them with a portfolio part.
Read More5 Rules of Thumb for Buying CNC Machine Tools
Use these tips to carefully plan your machine tool purchases and to avoid regretting your decision later.
Read MoreSetting Up the Building Blocks for a Digital Factory
Woodward Inc. spent over a year developing an API to connect machines to its digital factory. Caron Engineering’s MiConnect has cut most of this process while also granting the shop greater access to machine information.
Read More