New Business Plan Enables Shop to Increase Ventilator Part Production
KrisDee and Associates was able to increase production of a ventilator manifold from 90 parts per week to 780 parts per week thanks to changes the company started making months earlier.
Share
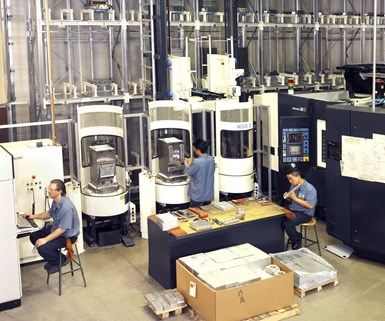
Due to the coronavirus pandemic, KrisDee and Associates has increased the number of ventilator manifolds it makes from 90 per week to 780 per week. These are complex parts with a number of grooves with tight tolerances and critical surface finishes.
KrisDee and Associates in South Elgin, Illinois has been producing ventilator manifolds for a large healthcare company for more than 10 years. Until recently, these parts were produced at a rate of 90 per week. So, when Jeff Majewski, the company’s general manager, first heard that the shop needed to increase production of the manifold to 780 per week to meet the demand driven by the coronavirus pandemic, he was in disbelief. “‘Are you serious?’ was the first reaction,” he says. When the shock wore off, he and the rest of the KrisDee team got together to figure out what changes the company needed to make to accommodate this increase. Within six weeks, the shop was meeting the demand, largely thanks to changes the company had started making months earlier.
KrisDee produces parts for a wide range of end markets, including aerospace, defense, automotive, hydraulics, healthcare and heavy industry. Mr. Majewski says this is a very intentional business strategy the company implemented after 2008, when one of its customers exited a market and KrisDee lost $10 million in sales overnight. “It just turned off on us,” he says. “And from that point forward, we made a decision to be very diverse in our customer mix and our market segments that we do work in.” Since then, the shop doesn’t allow any single customer or industry to account for more than 25% of its business. “We're trying to get that down even lower, to as low as 15% of our overall business in order to keep ourselves diversified for situations like this,” he adds.
One of the many parts KrisDee produces for its customers is the ventilator manifold. Mr. Majewski says it’s about the size of an 8.5- by 11-inch sheet of paper and is 5/8 of an inch thick. The manifold and its mating part, which KrisDee also makes, are both made of cast aluminum Mic 6 tooling plate. It’s a complex part for several reasons. “There's a lot of very critical grooves in there for gaskets on the backside, which have extremely tight tolerances usually within plus or minus a thou on the groove width,” he explains. “And then the surface finish of all the grooves are critical as well because it's used for sealing, and it's going to hold in the gas and help regulate the gas.”
Machines at the Ready
KrisDee was originally running the manifolds on its 2004 Makino A51 horizontal machining center. But when demand increased for the parts, the shop needed to start using its other machines as well. Ordinarily, finding the capacity to do this might have been a challenge, but a few months ago, KrisDee started making some changes that gave the shop the flexibility it needed. At the end of last year, Mr. Majewski says the company realized it wasn’t getting the uptime it was expecting from its flexible machining center. “We started moving some of those lower-volume parts back to that flexible machining center,” he says. “That actually helped us because that freed up a lot of capacity in our other machines in our facility where they were actually sitting idle.” KrisDee’s business plan allows for machines to sit idle, so when the order for ventilator parts came in, the shop had available capacity on four 2015 Makino A51NXs and two 1995 LaBlond Makino A55s. “It just happened to work where we had the capacity to do it,” he adds. “If we didn't start that process back in December, we would not have been able to handle this influx of work.”
KrisDee had also recently reprogrammed some of its parts to increase throughput by performing deburring in the machine. “We're willing to accept longer cycle times in order to have the machines do deburring,” Mr. Majewski explains. The ventilator manifold, for example, takes a while to deburr because it has a lot of holes and grooves that can’t have any sharp edges. Performing this operation on the machine adds to the cycle time but increases the throughput of the part. “The cycle time has gone up about 5 to 10%,” he says. “But now because we've added the deburring and things like that, we get more unmanned running.”
Ramping up Production
Increasing production wasn’t as simple as recreating the production process on the six additional machines. Mr. Majewski, along with the company’s owner and lead programmer had to figure out what they needed to do and come up with a timeline for how fast the company could get the additional machines up and running. Over the course of the next five to six weeks, KrisDee designed and built a universal pallet system and additional tombstones that worked on all the machines. Once the pallets and tombstones were built, the shop put them in the machines and ran through the program to test them. Then KrisDee had to do first article inspections and documentation to get everything approved. Mr. Majewski says the process of inspecting one of these manifolds can be time-consuming — it has so many features that it requires nearly a full day to inspect. The shop recently received approval on its final machine and 12 employees are now working to produce the manifolds.
Fortunately, KrisDee has not had issues obtaining the additional material required for this increase in production. The shop informed its supplier, Howard Precision Metals, that the material was for ventilator parts, and Mr. Majewski says Howard has been very helpful in getting material on the shop floor. “It's really helpful to have good partners in order to get all this stuff,” he says. “Without them we wouldn't be able to do it.”
Keeping Employees Safe
Because KrisDee is producing such critical parts, it’s critical that the company take extra precautions to keep its workers safe and healthy. If someone were to spread the virus through the facility, the shop could be forced to close, impacting the thousands of people who will need the ventilators it’s helping make. To prevent this, KrisDee has instituted extra cleaning procedures, which include spraying bleach on anything people touch. The company has also added lunch shifts so employees can take staggered breaks. Only one employee is allowed per table, and an appointed employee helps enforce social distancing guidelines.
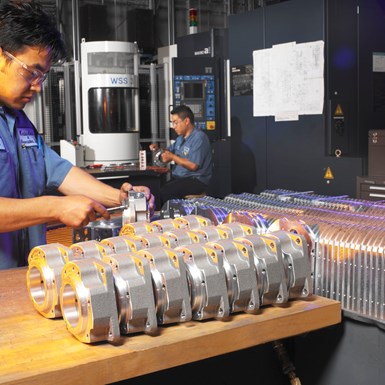
Because KrisDee is producing such critical parts, the company is taking extra precautions to keep its workers safe and healthy. The company is keeping employees apart at work, adding extra cleaning procedures, and frequently reminding staff to observe social distancing and quarantine guidelines at home.
The company also frequently reminds staff to observe social distancing and quarantine guidelines while at home and to not come in if they could be sick. “We're also reminding what the consequences are if we don't do it,” Mr. Majewski says. “We’re making parts that are for the healthcare industry, so if we have to shut, it could cause a lot of issues for other people as well.”
Looking Ahead
For now, KrisDee hasn’t had to make any staffing changes. “We have 55 employees, and we still have 55 working right now,” Mr. Majewski says. “We haven't had to make any cuts, luckily.” However, he does think staffing could become an issue down the line as other customers’ work picks back up.
Mr. Majewski says that despite the difficult situation, he’s grateful for the work. KrisDee’s automotive production has come to a standstill, and without the additional ventilator work, the company’s sales would be down 25%. He’s even more thankful to his employees for stepping up under the circumstances. “It's just a testament to our company and the kind of people that we have working here,” he says. “We couldn't do what we’re doing without them and their dedication and their families' understanding.”
Related Content
-
Shop Replaces Two Verticals With One Horizontal
By trading two VMCs in to help finance the purchase of a new HMC, this shop was able to significantly increase production and move to lights-out machining.
-
Horizontal High-Speed Machining Saves Hundreds of Work Hours
High-speed machining is the latest change at Blair-HSM South, helping this once old-fashioned shop improve productivity and morale while enabling new work.
-
Four-Axis Horizontal Machining Doubles Shop’s Productivity
Horizontal four-axis machining enabled McKenzie CNC to cut operations and cycle times for its high-mix, high-repeat work — more than doubling its throughput.
Related Content
Shop Replaces Two Verticals With One Horizontal
By trading two VMCs in to help finance the purchase of a new HMC, this shop was able to significantly increase production and move to lights-out machining.
Read MoreHorizontal High-Speed Machining Saves Hundreds of Work Hours
High-speed machining is the latest change at Blair-HSM South, helping this once old-fashioned shop improve productivity and morale while enabling new work.
Read MoreFour-Axis Horizontal Machining Doubles Shop’s Productivity
Horizontal four-axis machining enabled McKenzie CNC to cut operations and cycle times for its high-mix, high-repeat work — more than doubling its throughput.
Read MoreWeingärtner Maschinenbau HMC Provides Stable Machining
The MPMC features a wide base, optimized guide ratio and configuration of the guideways to provide stability and prevent vibration during operation, even under extreme cutting conditions.
Read MoreRead Next
Team Thinking Helps Donson Machine with Nickel Alloy Ventilator Part Production
This shop has taken unusual steps to draw on its strengths as a well-equipped machining facility with a skilled workforce to match.
Read MoreAerospace Supplier Shifts to Tight-Tolerance Ventilator Parts: "We Weren't in This Business Two Weeks Ago"
Skilled Manufacturing Inc. is running seven days a week to produce ventilator parts that will help healthcare workers battle the coronavirus.
Read MoreManufacturing Association Aids Shop’s Pivot to Ventilator Parts
After reaching out to the Austin Regional Manufacturers Association, a shop that typically serves oil and gas and heavy industry was able to quickly fill an order for ventilator parts.
Read More