Schunk's Tendo Slim 4ax Now Available with Coolant-Through
Schunk now offers a version of its Tendo Slim 4ax with Cool-Flow coolant-through technology.
Share




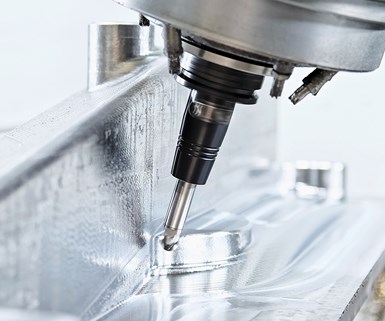
Schunk now offers a version of its Tendo Slim 4ax with Cool-Flow coolant-through technology. The Tendo Slim 4ax Cool-Flow toolholder offers various advantages when it comes to machining of steel, aluminum and plastic, the company says. The coolant or water jet does not depend on the unclamped length and adapts to the metalcutting process. In contrast to heat-shrinking mountings, the Tendo’s coolant jet does not bounce back along the whole unclamped length of the tool shank, but instead fully surrounds the tool shank up to the cutting edge. This is a benefit for cooling the cutting edge, improving chip removal and increasing efficiency of the overall process.
The hydraulic-expansion toolholder offers precise runout accuracy of under 0.003 mm at an unclamped length of 2.5×D and a balancing grade of G 2.5 at 25,000 rpm. Shape and positional tolerances can be met precisely, the company says. Schunk adds that the Tendo Slim 4ax can replace heat-shrinking toolholders without having to reprogram the outside contour.
For HSK-A63 interfaces between 6 and 32 mm in diameter, the toolholder is available in lengths ranging from 90 to 120 mm. Toolholders for SK 40 interfaces between 6 and 32 mm in diameter will be available later in 2020, with other interfaces and length variants being planned.
Related Content
-
T.J. Davies Retention Knobs Maximize Cutting Tool Life
Custom-made retention knobs are sized to fit the machine tool and spindle or toolholder to extend the life of existing machine tool assets.
-
Jergens Pull Studs Enable Quick Changeovers
SP140 and K02 pull studs offer quick-change solutions for vise or gripper jaws, electronic component manufacturing, packaging machines, medical technology and automation.
-
Lyndex-Nikken Toolholders Offer Stable, Versatile Machining
Polygonal shank toolholders provide a rigid connection between the tool and machine — ideal for all processes both in turning and milling.