Siemens and Ingersoll Expand Digital Enterprise Partnership
Siemens and Ingersoll are expanding their digital partnership to enable create digital twins of Ingersoll’s tools and further advance robotics and CNC.
Share




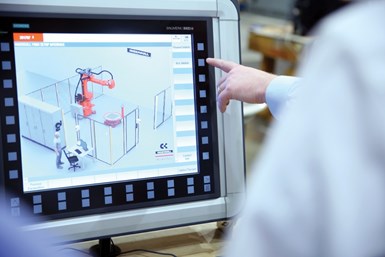
Siemens and Ingersoll Machine Tools are expanding their decade-long partnership to create digital twins of Ingersoll’s products and expand into new markets. Siemens’ cutting-edge technologies in hardware complement Ingersoll Machine Tools’ successful journey into additive manufacturing and push into industrial robots for the aerospace market with the entry-level robotic platforms MasterPrint Robotic and MasterPrint Continuous Filament.
For example, Ingersoll developed the MasterPrint 3D printer, the world’s largest device to print with thermoplastics. The MasterPrint at the University of Maine is able to 3D print objects up to 100 feet long, 20 feet wide and 10 feet tall. It primarily makes tools for the aerospace, space and marine industries, cutting costs and streamlining the manufacturing process: by printing large parts and machining them to their final shape with the same machine, manufacturing costs fall by 75% and lead times shorten from months to days.
“Ingersoll has strategic technology goals that push CNC products’ capabilities and performance beyond their OEMs’ intentions, conception and scope in term of accuracy, reliability, ease of integration and seamless programming experience,” says Piergiorgio Assandri, Ingersoll Machine Tools’ business director.
Ingersoll Machine Tools is using cutting-edge CNC automation hardware and software from Siemens to transform their business for the digital age. With the Siemens Virtual NC Kernel (VNCK), the company was able to embed the real CNC kernel into a virtual machine, allowing it to completely emulate real machine tool control and directly import the commissioning archive of the actual machine. This capability helped Ingersoll Machine Tools save time with faster commissioning and get machines to their customers faster. From an end-customer perspective, users will be able to simulate the manufacturing of their product and shorten their time-to-market while increasing their production quality.
Related Content
-
How this Job Shop Grew Capacity Without Expanding Footprint
This shop relies on digital solutions to grow their manufacturing business. With this approach, W.A. Pfeiffer has achieved seamless end-to-end connectivity, shorter lead times and increased throughput.
-
Swiss-Type Control Uses CNC Data to Improve Efficiency
Advanced controls for Swiss-type CNC lathes uses machine data to prevent tool collisions, saving setup time and scrap costs.
-
From Tradition to Transformation: Century-Old Manual Machine Shop Adds CNCs
After 122 years of working with manual mills and lathes, this fifth-generation shop acquired assets of a local CNC machining business and hired the owner. Here’s how it’s going a year later.