Share


Hwacheon Machinery America, Inc.
Featured Content
View More

ECi Software Solutions, Inc.
Featured Content
View More.png;maxWidth=45)
DMG MORI - Cincinnati
Featured Content
View More

Takumi USA
Featured Content
View More
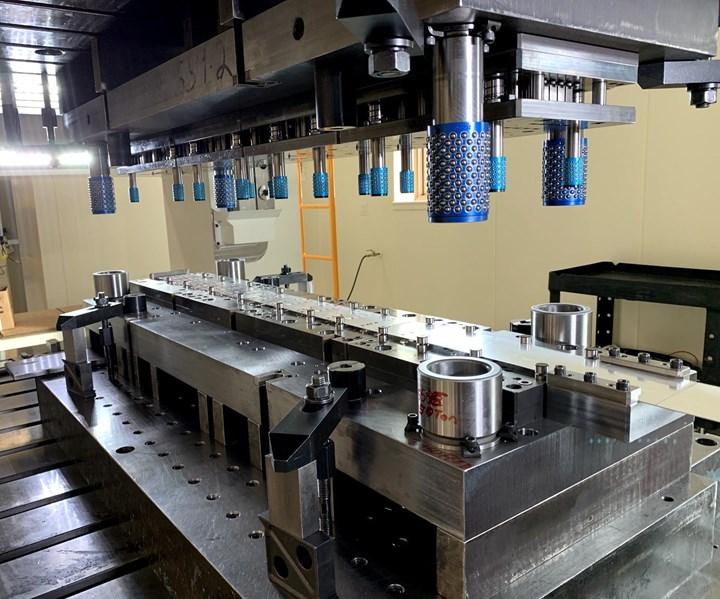
Otto Engineering makes both compound and progressive dies, like the one here. The coil of metal advances from the right to the left in this photo. Each time the press closes, the metal progressively makes its way through the die in a sequence of manipulations at various stations until a complete part is ejected at the end. Each time the press closes, a complete part is ejected.
“Becoming a tool and die maker is like driving a car — you don’t start out as a racecar driver. It takes awhile to get there,” says Neil Dohe. “You have to get a feel for what you’re doing, and that only comes with years of experience.”
In making this analogy, Mr. Dohe, who is the operations and sales manager at Dies Plus, a division of Otto Engineering, does not mean to imply a hierarchy between machinists and tool and die makers. Instead, his point is that a tool and die maker usually has a very specific skillset — one that includes the experience necessary to understand the “why” behind every cut that is made and how it translates to fitting the die components together during final assembly.
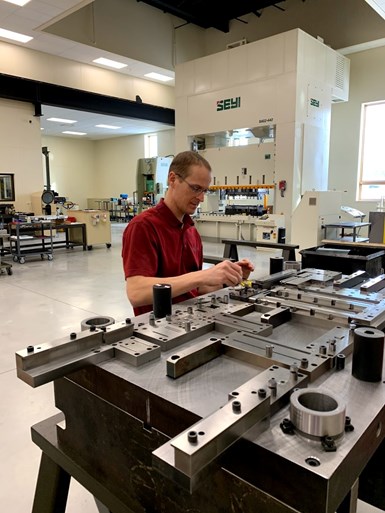
Craig Dohe, Neil’s brother, also works at Dies Plus as a tool and die maker. Here, he works on the final fitting of die components. A new Seyi press and overhead crane also occupy the toolroom.
Finding people with this particular skillset can be challenging. Adding to the complexity is the fact that a significant portion of tool and die production is currently done overseas. The trickle-down effect from this offshoring is that even fewer people are becoming tool and die makers, making this highly skilled position ever harder to fill.
But Otto Engineering has found a solution. “Our philosophy is to always do the work with the least-skilled person that you can, because if you use someone who's more skilled, you're just under-utilizing your capacity,” says Tom Roeser, president of Otto Engineering. Under this philosophy, only the final fitting and assembly is done by the company’s tool and die makers. The company has been fortunate enough that machinists have been relatively easier to find. These skilled professionals have less expertise specific to tool and die work, but Otto has now systemized this work to make CNC machining of die components by machinists part of the solution.
Making Use of Extra Capacity
“Hope is not a strategy,” Mr. Roeser says. Through the years, he has made a series of strategic decisions to get his business to where it is today. The most recent of these was to merge Otto Engineering with Dies Plus at Otto’s new technical center in Carpentersville, Illinois. For almost 60 years, Otto Engineering has developed and manufactured control products (switches, joysticks and grips) and two-way radio communication accessories, making small volumes of parts for demanding applications, and for 31 years, Dies Plus (which was founded by Jerry Dohe, Neil’s father) has made tools and dies, mostly for the automotive industry.
Both Mr. Roeser and Mr. Dohe saw growth opportunities in this merge, which occurred about three years ago. Given that Otto Engineering’s new tech center was a second location for the company and that machinists were already in place doing production and machining work, the company had extra capacity. Mr. Roeser saw diemaking as the greatest opportunity to fill this capacity but was having trouble finding tool and die makers to replace his rapidly retiring staff. Enter Dies Plus. Before the companies merged, Otto Engineering only had three tool and die makers. Now, there are 11 between both divisions, with eight apprentices in the pipeline. Meanwhile, Mr. Dohe also saw growth opportunities for Dies Plus. As a division of Otto, his company would have the chance to diversify into new industries like aerospace and military. It would also be a way to gain the additional resources necessary to purchase new equipment, including a Seyi press and several Mitsubishi EDMs from MC Machinery Systems Inc.
Today, Otto’s diversity means that the company can focus on tool making rather than stamping parts. Otto can provide tooling to OEMs and stampers since it does not compete with either type of company.
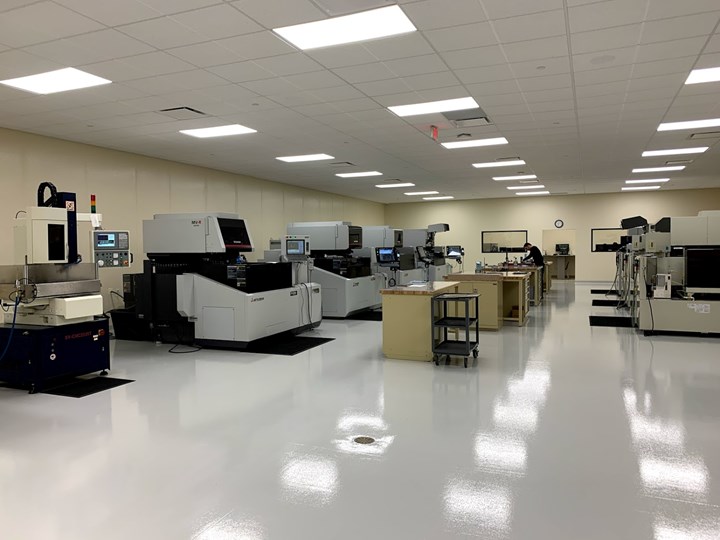
All the Mitsubishi EDMs are plugged into the walls to keep the EDM area cleaner. The company worked with MC Machinery to equip each machine with heat exchangers so they could be vented into the central chilling system. At the back of this room is a small control room with screens to view the Remote360 program. The goal is to hang a large screen here so it can be viewed from the shop floor.
Otto Engineering employs 51 people at the new tech center and 550 people total. Mr. Roeser credits some of his luck finding skilled workers with being a member of the Illinois Tooling and Machining Association (TMA). Out of the 50 people going through TMA training this year, he says, 14 work for Otto Engineering.
With people in place, the next challenge was to grow the die making side of the business.
Systemization of Die Making
Otto Engineering makes progressive and compound dies. In progressive dies, a coil of metal is fed through the various stages of a die set so that each time the press closes, a complete part is ejected from the end. In a compound die, a workpiece is formed, holes are punched, and the workpiece is shaped each time the press closes, creating a complete stamping.

Toolmakers are still important and necessary at Otto Engineering. After the machinists produce die components, the toolmakers use their skill in the fine detail grinding during final assembly.
Dies are made from components that are mounted on top and bottom die plates. The final assembly of these die sets is done by a tool and die maker who knows how to precisely fit the components together in order for the die to function properly in the press. During final assembly, the tool and die maker will often take individual die components to a manual grinder and finesse them until they achieve the desired fit.
However, leading up to the final assembly, the components typically are milled, EDMed and ground to specific tolerances. That is, they are produced as precision-machined parts, through setups and operations that fall squarely into a CNC machinist’s wheelhouse. Recognizing this, die making leaders at Otto set about figuring out how to transform the die components (to be fitted later) into systematically repeatable parts for machinists to produce. In other words, the company had to make die making less of an art and more of a process.
In the past, a designer could give a half-designed part to a tool and die maker, and that person could fill in the missing information based on his or her experience. Now with machinists performing the bulk of the machining operations, designers would need to communicate more completely through fully designed prints.
Leading this effort was designer Chad Coates. He implemented a “machine by color” technique, which is a visual way to communicate the tolerancing information toolmakers inherently know. In this system, machinists can look at the 3D model and know that a red feature means to EDM a hole, a blue feature should be ground/machined and a green feature should be hard milled.
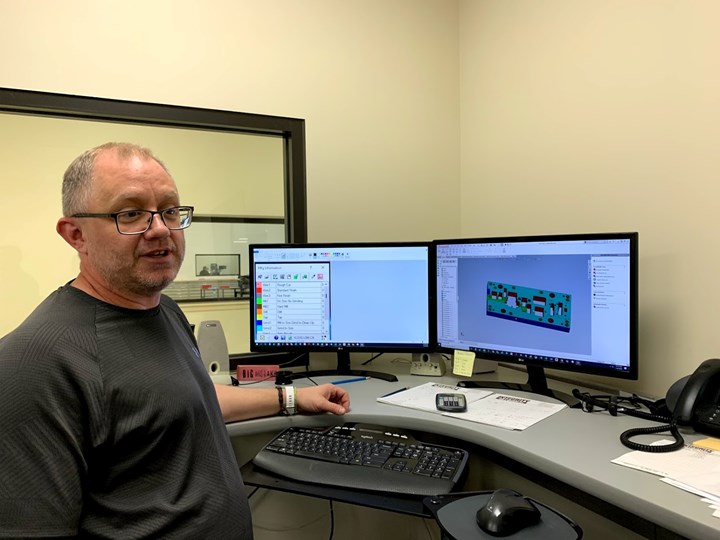
Chad Coates implemented an intricate system that employees at Otto Engineering call “machining by color.” For instance, a feature that is a specific dark color on the 3D model must be milled to size and then ground to clean up. A light version of that color means the feature is strictly ground to size. With this new system, Otto Engineering officially moved from being toolmaker dependent to being designer dependent.
While the capability to color-code features has been part of design software for years, it is up to individual companies to refine the color variations for their specific uses. Mr. Coates, who is also an experienced toolmaker, implemented a machine-by-color system at Otto that he learned while working at a previous employer. He has built on this background and adapted it to Otto’s particular needs. For instance, one color could indicate to the machinist not only to EDM a hole, but to keep it undersize, leaving a certain amount of material for the toolmaker to remove manually in the final fitting. A dark version of another color could mean to finish in the mill and a light version could indicate to finish on a grinder. Eventually, Mr. Coates was able to implement and build a robust library of color-coded features specific to the machinists’ informational needs. Every job has a chart meaningful to that particular job.
“Machining by color has simplified insight that otherwise can be overwhelming to communicate,” he says.
To implement machining by color, the company uses the software programs 3DQuickPress and Logopress, which are die design add-ins for SolidWorks. The software keeps the designers from needing to manually add color to each feature — feature definitions lead to automatic application of the right color. On its Mitsubishi EDMs, the company uses Esprit CAM software from DP Technology Corp.
Machine Monitoring System for Wire EDM
Using machinists to make die components and integrating two separate companies into one have been major shifts for Otto’s business and employees. And these shifts are still ongoing. For example, the Otto’s new tech center has two toolrooms — one room supports large dies up to 440 tons and the other supports high speed, smaller presses.
The EDM area in the Dies Plus division is notable. Not only is it impeccably clean (as is the entire facility), but there are seven new Mitsubishi EDMs here — significant capacity. Moreover, a central chilling system keeps the room’s temperature consistent and the keeps the machines to a tight window of precision. The company worked with Mitsubishi to customize a heat exchanger on each machine, so all cooling now goes through the walls to the central chilling system.
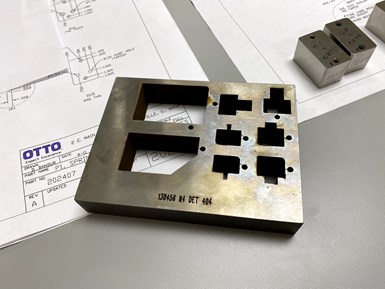
Communicating instructions through engraving is the next step in getting rid of job travelers and moving to a paperless system. The instructions on this burn block are only for this particular block.
In this EDM area, Dies Plus is taking the next steps in systemizing die making by moving toward a paperless process in which it gets rid of job travelers. Instead, information is engraved directly on each burn block — the nested set of EDMed components for a given die that gets machining such as holemaking before blocks are EDMed out (see photo). According to Mr. Dohe, engraving each burn block with specific information to that part connects the nested set of components to digital information about that die, reducing paper.
The EDM process for these burn blocks is monitored remotely using MC Machinery’s remote360. Using this production monitoring and support system, employees can be away from the machines yet still see how the EDMs are progressing with green, yellow and red charts. The web-based application provides real-time data that enables employees to see uptimes/downtimes and when each machine has open capacity for a new job. One of the dashboards enables Mr. Dohe to see percentage of job completion, the amount of wire remaining, the program number, the runtime and the material being cut on each EDM. Remote360 gives him the extra information necessary to keep the machines running longer. It even lets him see when machine maintenance will be needed in the future. “We can see ahead with remote360 and plan things out instead of waiting until something is finished, or when an immediate action needs to occur,” he says. In the EDM area, two preset stations in combination with machine monitoring have helped improve uptime by roughly 25%, he says.
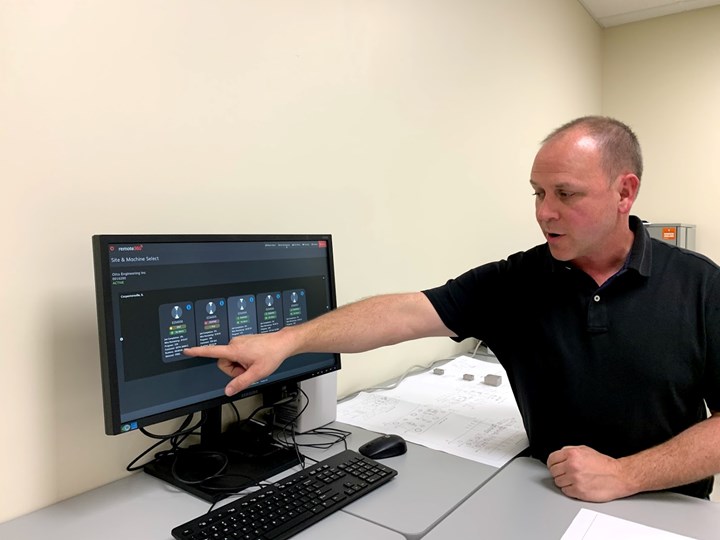
Neil Dohe shows how this dashboard of MC Machinery’s remote360 monitoring system enables him to see percentage of job completion, the amount of wire remaining, the program number, the runtime and the material being cut on each EDM.
Achieving the Final Fit
The promise of all of this will be much greater die making capacity, and the ability to leverage tool and die professionals who will continue to be in short supply. It is a work in progress, as all the leaders involved with it note. Although the key concepts are in place and working well — using machinists for die making, standardizing the process, working toward a paperless system and remotely monitoring machines — Otto Engineering and the Dies Plus division are still in a state of transition. Like the final assembly of the dies themselves, the companies are now to the point of making small adjustments here and there, as they become skilled at fitting all these new components together.
Related Content
How to Achieve Unmatched Accuracy in Very Large Workpieces
Dynamic Tool Corp. purchases two bridge-style double-column CNCs to increase the cutting envelope and maintain 5-micron cutting accuracy in the long term.
Read MoreLyndex-Nikken Collets Enable Accurate Small-Diameter Cutting
The MMC Mini-Mini collet chuck is well suited for high-speed machining applications where clearance is needed, such as die mold, aerospace and medical parts.
Read MoreIn Moldmaking, Mantle Process Addresses Lead Time and Talent Pool
A new process delivered through what looks like a standard machining center promises to streamline machining of injection mold cores and cavities and even answer the declining availability of toolmakers.
Read MoreGrob Systems Inc. to Host Tech Event With Industry Partners
The 5-Axis Live technology event will highlight new machining strategies for optimizing the production of complex medical, aerospace and mold/die parts.
Read MoreRead Next
Anti-Electrolysis Is Pro EDM
A new breed of power generators for wire EDMs has options for reducing, even eliminating, one of the unwanted side effects of this very versatile metalcutting process.
Read More5 Rules of Thumb for Buying CNC Machine Tools
Use these tips to carefully plan your machine tool purchases and to avoid regretting your decision later.
Read More