Rotary Grinders Leave Cleaner Build Plates
While metal 3D printing saves on tools, build plate resurfacing is a bottleneck. The latest rotary grinders can provide an efficient, high-quality alternative to bandsaws or wire EDM.
Share








ECi Software Solutions, Inc.
Featured Content
View More
Hwacheon Machinery America, Inc.
Featured Content
View More
Takumi USA
Featured Content
View More
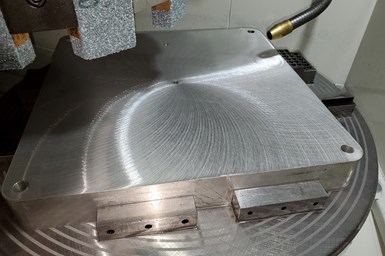
DCM Tech’s IG series rotary grinders include sensors for determining when the grinder finishes clearing residue and meets the build plate surface. It can then change its grinding strategy to one suitable for the build plate. All images courtesy of DCM Tech, Inc.
Metal additive manufacturing removes many bottlenecks from the manufacturing process, but it also introduces a notable new one: users must remove all residual metal from build plates before reusing them. The latest rotary grinders can provide an efficient alternative to wire EDM or bandsaws for removing this material while also ensuring flatness and levelness. These machines put the tight tolerances, quality surface finish and automation-driven efficiency that build plate grinding demands well within reach.
Automate Inconsistencies Away
“Unlike older-style machines, advanced rotary grinders do not need constant operator input or oversight,” says Doug Hedges, chief technology officer of AM contract manufacturer Beehive3D, Inc. “This allows the operator to multitask and minimizes the risk of error.”
For example, high-end rotary surface grinders can control the initial contact between the abrasive wheel and the build plate instead of leaving it to the operator. They use vibration feedback from sensors to automatically fine-tune not only the pressure of the spindle motor, but also how quickly it moves the wheel down onto the build plate. The grind cycle begins when the machine senses that the abrasive wheel has contacted the build plate.
“Different grind recipes can be set for different customers, material types or construction builds so complex programming or data does not need to be entered at the start of each job,” explains Erik Lawson, engineering manager at DCM Tech.
Also important is the ability to alter grinding parameters through the grind cycle. The material characteristics of the printed part residue and the build plate may be very different, and the grinding abrasive must work differently on both surfaces. Modern rotary grinders automatically make that transition. Newer equipment also tends to include built-in load monitoring, reducing the necessary amount of operator oversight.
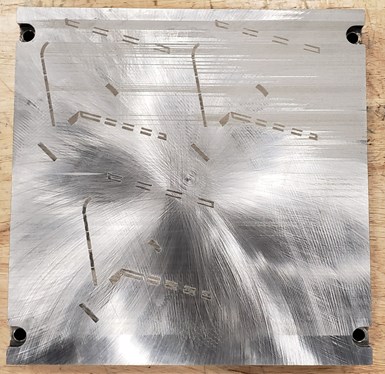
Not only do remnants of metal persist on the build plate after AM parts are removed, but portions of the build plate can become bowed or distorted. Thus, it is critical to resurface the build plate to precise process tolerances after each use.
Automatic wheel dressing is another example of grinding automation. Manual dressing is a labor-intensive process that typically requires holding a tool against the wheel to knock off used or clogged abrasive. Hard part materials like Inconel can require dressing wheels as often as every 10 minutes — Hedges particularly recommends automatic wheel dressing for applications using these materials.
Simple Controls and Recipes
Some high-end rotary grinders, such as DCM Tech’s IG series, offer simple controls such as a touchscreen Human Machine Interface (HMI) that operators can use to enter requirements or necessary adjustments without programming. This capability supports processing flexibility by making it easy to adjust grinding factors to prevent issues from reoccurring.
For routine processes, the IG series can use grind “recipes” with sets of parameters for different AM construction builds to further speed production, enhance quality and aid in quick changeover.
“Different grind recipes can be set for different customers, material types or construction builds so complex programming or data does not need to be entered at the start of each job,” explains Erik Lawson, engineering manager at DCM Tech. “A new recipe can be created for job variations, such as a different finish for a specific AM material.”
These recipes can accommodate build plate texture requirements, eliminating the need to “roughen up” a build plate in a separate process so the AM part will properly adhere to the surface during buildout. Instead, Hedges says, operators will only need to wipe down the build plate with alcohol or another solvent and let it dry before using it again.
Related Content
How to Mitigate Chatter to Boost Machining Rates
There are usually better solutions to chatter than just reducing the feed rate. Through vibration analysis, the chatter problem can be solved, enabling much higher metal removal rates, better quality and longer tool life.
Read MoreOrthopedic Event Discusses Manufacturing Strategies
At the seminar, representatives from multiple companies discussed strategies for making orthopedic devices accurately and efficiently.
Read MoreHigh RPM Spindles: 5 Advantages for 5-axis CNC Machines
Explore five crucial ways equipping 5-axis CNC machines with Air Turbine Spindles® can achieve the speeds necessary to overcome manufacturing challenges.
Read MoreQuick-Change Tool Heads Reduce Setup on Swiss-Type Turning Centers
This new quick-change tooling system enables shops to get more production from their Swiss turning centers through reduced tool setup time and matches the performance of a solid tool.
Read MoreRead Next
7 Key Factors in Choosing a Grinding Wheel
The grinding wheel market is wide, but seven application factors can help users narrow the market to the wheels they need.
Read More4 Ways Robots and 3D Printing Intersect
Four examples of how robotic automation and additive manufacturing both help and are helped by each other.
Read MoreOne Small Step for Metals, One Giant Leap for AM
Eliminating support structures for metal parts expands pathways to profitable AM.
Read More