Portable Surface Gaging in a Production Environment
Handheld portable surface gages are easy to use. But that doesn’t mean there aren’t challenges when scanning hundreds or even thousands of parts.
Share




We have discussed making surface finish measurements at the point of manufacture several times in this column. The reasons for making surface finish measurements are numerous. Surface finish is becoming a bigger component of shrinking tolerances as it will affect the function and appearance of manufactured parts. For example, as machine tooling wears, surface finish will be affected and thus it becomes critical to measure a part’s surface finish regularly, or in the manufacture of very critical components, for every part.
Handheld portable surface gages are extremely easy to use — often with single-button and error-free operation through automatic cutoff selection that ensures the correct measurement results, even for non-measurement technicians. However, despite its portability and ease of use, having the operator position the surface finish gage on hundreds, or even thousands, of parts during the day at the precise location of the required measurement can be challenging, even for the most skilled users. This is where custom fixturing for the surface finish probe and easy interfacing between the portable surface finish control unit and automation controllers are making productive advancements.
When designing gages for surface finish measurements in a production environment, speed and high precision are important considerations. Just as an air plug is made close to the measuring size, a portable surface finish plug can also be made to nearly the size of the hole to be measured. Instead of an air orifice being the measuring source, a surface finish probe can be built into the plug for performing the surface finish check at a specific location. For different size bores, the plug holding the surface finish probe can be made to expand using an air cylinder. This essentially locks the plug into position to enable hands-free operation.
Mounting the probe in special fixturing is a good designer challenge. Once the gage is designed, there are other challenges to face. You have to collect the data, determine when to collect it, and decide whether the custom fixture needs to be designed into a human-free automated system, controlling functions and part programs to be shared between the surface finish gage and the automation system. Because of this need for automation, there are new features implemented in surface systems to make the execution easier.
One of the industry trends is to ensure that the proper measuring system actually did the measurement. The International Automotive Task Force (IATF) recommends traceability of products and assignment of measuring equipment to the production parts. Mobile surface gages (along with micrometers, calipers and digital indicators) are starting to include the ability to send a gage identifier along with the measured data. This ensures the device performing the measurement is documented with the parts and can be verified for capability and calibration.
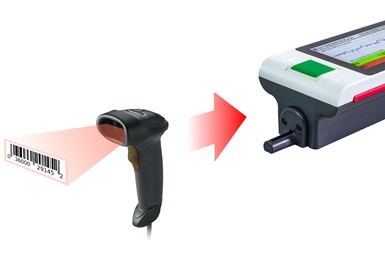
Some surface finishing gages systems allow handheld scanners to be connected so that all the setup parameters can be placed in a scan code on the batch of parts being measured.
There are more than 30 different roughness parameters, which can be selected with stroke and cutoff length to achieve certain blueprint callouts. Though many surface finish gages are as easy to use as cell phones, setting up the gage can take time and is subject to user error. Today, these systems allow handheld scanners to be connected so that all the setup parameters can be placed in a scan code on the batch of parts being measured. The operator then scans the code and the system is ready to measure those parts with the proper settings automatically loaded.
For truly automated surface finish applications, where the portable surface is part of a machine-controlled measuring process, the surface gage must have the capability of communicating and taking commands from the automation system. More and more surface systems are now capable of taking ASCII commands to control the measuring part process or inquire about measured results. Should the controller sense wrong or out-of-control conditions, text instruction can be sent to the device for a user to read and take action on the process.
Finally, once the surface finish measurement is made, there is a lot of data to be stored — not only the parameter results, but the actual part traces. These are all accessible through easy communication requests to the surface device to take their stored information and pass it to long-term documentation of the parts should it be needed in the future.
In summary, today’s portable surface gages have mostly kept their simplicity of operation to the minimum for use at the point of manufacture. However, there is nevertheless a lot of information available and potential for making these systems part of an automated process. Today, these systems are getting the capabilities to make surface measurement part of every manufacturing process.
Related Content
The Link Between CNC Process Control and Powertrain Warranties
Ever since inventing the touch-trigger probe in 1972, Sir David McMurtry and his company Renishaw have been focused on achieving process control over its own manufacturing operations. That journey has had sweeping consequences for manufacturing at large.
Read MoreParts and Programs: Setup for Success
Tips for program and work setups that can simplify adjustments and troubleshooting.
Read MoreBallbar Testing Benefits Low-Volume Manufacturing
Thanks to ballbar testing with a Renishaw QC20-W, the Autodesk Technology Centers now have more confidence in their machine tools.
Read More6 Machine Shop Essentials to Stay Competitive
If you want to streamline production and be competitive in the industry, you will need far more than a standard three-axis CNC mill or two-axis CNC lathe and a few measuring tools.
Read MoreRead Next
5 Rules of Thumb for Buying CNC Machine Tools
Use these tips to carefully plan your machine tool purchases and to avoid regretting your decision later.
Read MoreBuilding Out a Foundation for Student Machinists
Autodesk and Haas have teamed up to produce an introductory course for students that covers the basics of CAD, CAM and CNC while providing them with a portfolio part.
Read More