Share




Much of the advice for CNC machine shops or other established manufacturers looking to implement 3D printing recommends the same basic progression: Start with a polymer or composite printer and put it to use for tooling applications around the shop to learn about the technology and explore its possibilities, then move on to production additive manufacturing if and when it makes sense. But RPG Industries Inc., a machining job shop in Tipp City, Ohio, didn’t need to be convinced of the potential of additive manufacturing (AM) for production. “3D printing really intrigued me,” says the company’s president, Robert Ginsburg. “To me that was just one of the neatest things. You can design something on a computer, hit a button and the next day you had a functional part.” So when RPG had the chance to add production metal AM capabilities in the form of a Metal X system from Markforged, Ginsburg grabbed the opportunity. But although the shop was ready to start its additive manufacturing journey with production, it didn’t skip the tooling step entirely.
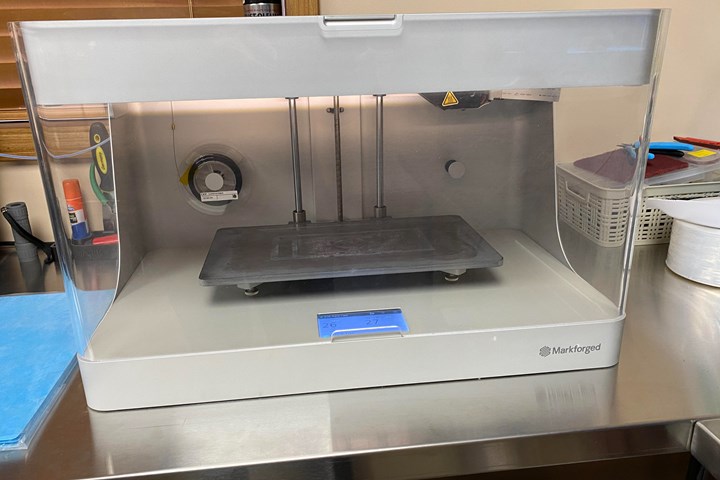
When RPG purchased its Metal X metal 3D printer from Markforged, it came in a package deal with a Mark Two composite printer. While the shop has used it for end-use parts and prototypes, its main use is to produce tooling for internal use.
When RPG purchased its Metal X, it was part of a package deal from Markforged that included a Mark Two composite printer. This machine prints parts in Onyx, which is Markforged’s composite base material consisting of nylon filled with micro carbon fiber. The Mark Two can also add layers of continuous carbon fiber for added strength. “With that continuous reinforcement, you can make some extremely strong parts,” Ginsburg says, including “parts that rival aluminum with less weight.”
While RPG has used the Mark Two to produce end-use parts (such as face shields during the beginning of the COVID-19 pandemic and brackets with carbon fiber reinforcement) and prototypes (including an initial version of a carburetor cap for a 1930s classic car that was used to test the fit before printing the final version of this replacement part on the Metal X), Ginsburg says its main use has been printing tooling for internal use. RPG thus reverses the job shop’s typical AM progression, starting with production but finding its way into tooling. Some of these tooling applications include:
- EDM Guides. Ginsburg says that in some wire EDM and EDM drilling applications
For some applications on its wire and EDM drilling machines, RPG will use the Mark Two to print a composite guide to help ensure precise, accurate machining.
- Jaws for Difficult-to-Hold Parts. RPG has also used the Mark Two to
RPG used these composite 3D printed jaws to hold long, extruded parts while holes were drilled into them.
- Organization Around the Shop. RPG has found many applications for
RPG designed and printed this stand that is mounted to a table near the sintering oven and holds a number of tools for it.
Learn much more about RPG Industries including the opportunities the company has found with its Metal X 3D printer in this feature article.
Related Content
Custom Workholding Principles to Live By
Workholding solutions can take on infinite forms and all would be correct to some degree. Follow these tips to help optimize custom workholding solutions.
Read MoreLean Approach to Automated Machine Tending Delivers Quicker Paths to Success
Almost any shop can automate at least some of its production, even in low-volume, high-mix applications. The key to getting started is finding the simplest solutions that fit your requirements. It helps to work with an automation partner that understands your needs.
Read MoreUsing Automation to Reduce COGS and Stay Globally Competitive
Decade-long, multiphase automation investments lower operating costs and maintain technology lead in an increasingly competitive global market.
Read MoreRail Manufacturer Moves Full Steam Ahead with Safe, Efficient Workholding Solution
All World Machinery Supply paired a hydraulic power unit with remote operating capabilities in a custom workholding system for Ahaus Tool & Engineering.
Read MoreRead Next
FFF 3D Printing for Metal: Sintering Can Wait
Separating 3D printing from high-temperature processing is part of how the Markforged Metal X realizes a price less than established metal AM equipment.
Read MorePVD Coatings Solve Common 3D-Printed Mold and Part Problems
The right surface modification solution can alleviate a few common additive manufacturing pain points that typically require creating new molds or parts.
Read More10 Examples of 3D Printed Tooling
Additive manufacturing can aid conventional manufacturing through the production of tooling. This article showcases 10 clever uses of 3D printed tooling.
Read More