In the Supply Chain, Flexibility Equals Strength
Machining job shops offer lessons in supply chain resiliency. Also, goodbye and best wishes to a longtime teammate making a change.
Share




One of the odd things we all learned from the pandemic: There are two types of toilet paper.
There are the rolls and packages we are all familiar with from buying them at the supermarket. Harrowingly, this supply briefly ran thin last year. Then there are the big rolls shipped to workplaces and institutions. There were always plenty of these. So: Perfect — just repurpose one so it could answer the shortage of the other, right?
Actually, no; it was not that easy. Even for two products so similar, there was no easy path for redeploying one as a substitute for the other.
That small crisis quickly passed, but it illustrates a much larger point that has also been highlighted recently by store shortages and shipping delays for various other products, by bottlenecks at ports with container ships waiting to be unloaded and even by one such ship briefly blocking the Suez Canal. Namely: Our supply chains are arteries of vulnerability, and what makes them so vulnerable is the “efficiency” of specialized production and limited or singular lines of supply.
Thanks to the growing recognition of this, supply chains have been in the news. An order by the president directs federal agencies to discover potential supply-chain vulnerabilities. But when we talk about developing stronger supply chains, a big part of what we are really talking about is flexibility — that is, supply capacity that can nimbly pivot to other purposes as needed. For a model of this, for an example of how to make supply chains more resilient, I recommend the leaders of those federal agencies consider a type of manufacturing business that has remained flexible: the CNC machining job shop.
Lately, I have been encountering many cases of job shops pursuing AS9100 certification for aerospace machining. Reason: Many of those shops were serving the oil and gas industry, a sector in which activity has declined. This reminds me of the 2000s, when shops in the tool and die sector shifted to production work after U.S. toolmaking business dropped. Because small, independent machine shops cannot ever rely on any one source of business remaining steady, they have been forced to become good at pivoting.
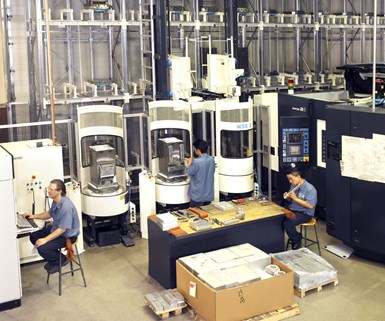
Many machine shops quickly shifted to ventilator production last year. KrisDee and Associates, pictured, rose to a different challenge. This shop was already making ventilator parts, but it was called to multiply its production by a factor of 9. Here is the story.
Last year, we saw this flexibility in action with the surge to increase ventilator capacity. Major OEMs such as automakers were recruited into the effort, but companies such as these cannot literally make the components of ventilators themselves on short notice. Within their supply chains, however, are companies that can. Metalworking job shops that had previously served different industries, where team members perhaps had never even seen a ventilator, pivoted in a matter of days to ventilator component production. In the supply chain, flexibility equals strength.
The one area of production where we are perhaps most in need of this strength, because we are most vulnerable due to “efficient” supply lines that are inflexible, is in our food supply. During the pandemic year, another public discovery was our revelation of just how few meat-packing plants there are. For example, just one plant in South Dakota accounts for 5% of all U.S. pork. Couple this with recent studies showing how vulnerable single-crop farms are to extreme weather, plus the sight of farmers last year destroying milk, carrots and potatoes simply because (similar to the toilet paper predicament) this supply was produced for restaurants and could not easily be redirected to supermarkets. (My source for all these points is this article from the Washington Post.) In response to weaknesses such as these, smaller farms and the move toward more locally sourced agriculture show a way, but on an even greater scale, the food supply needs resiliency. What can the world of CNC machining give to the world of farming?
What indeed.
With that last question, I want to make my own pivot, leaving the thread of this column there in order to share something personal. With this month’s issue of Modern Machine Shop, we say goodbye to senior editor Emily Probst. Emily and her husband, Jeff, own an independent farm market, Blooms and Berries, in Loveland, Ohio. For years, Jeff has led it while Emily worked in media. But that business is growing, and she now wants to devote herself to it — working alongside her husband, with and for her family. Who could argue with that choice?
Emily joined MMS as an intern in 2006. I have worked with her almost continuously since that time. To say we will miss her says too little. Emily has a mind for remaining attentive to all the details and a heart that is even more attentive to care and inclusion for those around her. Those attributes make her an invaluable member of any team she joins. This team on MMS will now change, but we are grateful for the many years through which she has shared this work with us. Thank you, Em.
For readers who are not far from Loveland, Ohio, Blooms and Berries’ “U-Pick” blueberry season typically begins in June.
Read Next
Has Lean Become Too Extreme?
Surges in demand reveal a weakness of just-in-time supply chains.
Read MoreDoes Asia's Low-Cost Manufacturing Option Still Make Sense?
As U.S.-based companies try to stay ahead of COVID-19, global supply chains are under renewed scrutiny. Are uncertainties and delays caused by global crises worth the short-term cost savings?
Read More5 Rules of Thumb for Buying CNC Machine Tools
Use these tips to carefully plan your machine tool purchases and to avoid regretting your decision later.
Read More