Five-Axis and Clever Controls Support Medical Manufacturing
Kern’s Micro Vario and Heidenhain’s TNC 640 control give M5 the precision and accuracy it needs to successfully micromachine medical parts.
Share




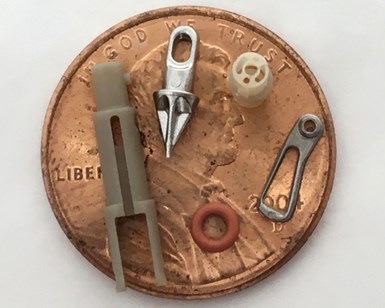
Although 80% of M5’s work during the pandemic has been for the medical industry, the company’s micromachining experience spans multiple industries. These five micromachined parts are made of varying materials, such as PEEK, rubber and cobalt chrome. Photos courtesy of M5.
In early 2020, small Minnesota-based shop M5 expanded its micromachining capabilities by purchasing a five-axis Kern Micro Vario machine tool. Soon after, it bought another.
These purchases pushed M5’s accuracy and tolerance limits and led to M5 becoming a critical vendor for many essential medical equipment businesses. Now, the four-person shop creates everything from micro-fluidics molds for vaccines to brain surgery tool components to micro-molds of pacemaker prototype pieces. “Two of the best investment decisions we’ve ever made,” declares owner Jon Baklund.
Micromachining Tools
The pacemaker parts required eight 0.005" holes, and sterility requirements meant the parts could not be touched by human hands. Baklund stressed the importance of mechanical automation and machine accuracy in meeting these requirements.
“Not only does it result in cost savings,” Baklund says. “It also gives us the ability to do many more critical processes and achieve finer surface finishes, which brings profitability.”
Meeting this accuracy was especially difficult as thermal expansion can cause machining issues at these micro-levels — but the Kern machine tool bypassed these concerns due to a configuration that pumps cold water throughout the structure to make it more temperature-stable than its outside environment. “This often results in a huge cost savings for manufacturers, who no longer need to acquire giant AC units and more to stabilize their rooms,” Kern president Toni Mangold says.
M5 lead tool maker and designer Alex Madsen notes other process improvements: “I’m regularly using end mills of 0.003" diameter on hardened steels with these machines, often resulting in surface finishes like mirrors. Also, the fifth axis helps with tool life. Being able to machine five sides of a part at one time eliminates having to fixture second clamping.”
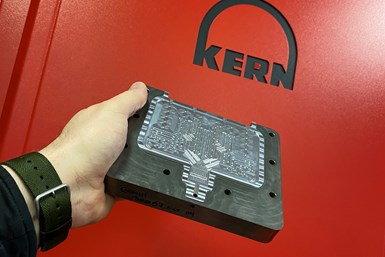
This micro-fluidics mold for vaccine production includes almost 30 0.010”-wide channels. M5’s staff had to machine the entire bottom of the mold with a single 0.008”-diameter end-mill so it would have a near-perfect flat surface with no steps or individual facets.
Dynamic, Accessible Controls
Despite having no prior experience with five-axis machining or the Micro Vario’s Heidenhain 640 TNC control, Madsen was completing jobs within a week and a half from when M5 received its first Micro Vario.
“The first thing I noticed about the Heidenhain control was that it uses a more verbal language for tool changes and things like that,” Madsen says. “Even if I am manually typing in some G code, the programming screen provides a description as to what it is and what I should look for. The tool table is nice, and the probing cycles are also easy to follow.”
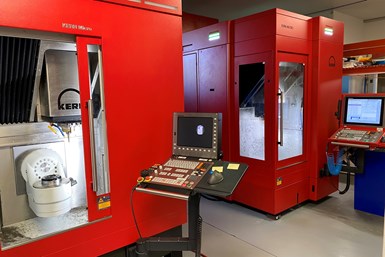
Even with the Heidenhain TNC 640 control’s remote desktop manager enabling the shop to program jobs at home during the night, M5 soon hit the capacity limits of its first Micro Vario. Only four months after buying the first machine, it added a second Kern machine with an identical Heidenhain control.
The controls also feature a remote desktop manager, enabling M5’s employees to work remotely and set up jobs at night. Between this capability and Madsen’s tendency to work on five or six different types of parts every day on two machines running simultaneously, the shop requires accurate simulation work. With features such as optional Dynamic Collision Monitoring, which helps prevent spindle crashes, Madsen says the control delivers: “I basically do a full render of my part on the control, and there have been times where it shows a half-a-thousandth step off that was in the G code. So, on these really tiny parts where I need super-fine surface finishes, I can prove it out on the control and trust what I see.”
Related Content
A History of Precision: The Invention and Evolution of Swiss-Style Machining
In the late 1800s, a new technology — Swiss-type machines — emerged to serve Switzerland’s growing watchmaking industry. Today, Swiss-machined parts are ubiquitous, and there’s a good reason for that: No other machining technology can produce tiny, complex components more efficiently or at higher quality.
Read More3 Tips to Accelerate Production on Swiss Lathes with Micro Tools
Low RPM lathes can cause tool breakage and prevent you from achieving proper SFM, but live tooling can provide an economical solution for these problems that can accelerate production.
Read MoreWhere Micro-Laser Machining Is the Focus
A company that was once a consulting firm has become a successful micro-laser machine shop producing complex parts and features that most traditional CNC shops cannot machine.
Read MoreRead Next
Holding Submicron Part Tolerances
Sunlight-Tech Inc. has used GF Machining Solutions’ Microlution laser micromachining and micro-milling centers to produce parts with tolerances tighter than 1 micron.
Read MoreWhat Should You Consider When Turning Micro Parts on a Lathe?
Various factors, including the machine, cutting tools and operator, must be taken into consideration to turn very small parts.
Read More5 Tips for Making the Switch to Micromachining
Working at the micro-level requires changing the way you approach machining parts, and these tips can help you avoid pitfalls.
Read More