Cutting Tool Maker Succeeding With 3D Printed Carbide for Oil/Gas and Other Applications
Powders, parts and products are different ways the company is advancing with AM. Carbide and tools are separate areas of success.
Share



This article originally appeared on our sister site, Additive Manufacturing. Explore more AM topics at additivemanufacturing.media.
Could additive manufacturing be used to produce a tungsten carbide cutting tool for use in CNC machining?
In principle, yes, says cutting tool maker Kennametal. Tungsten carbide, the principal material used in high-performance cutting tools for machining, is a material the company is already applying through AM. However, tools for metal cutting are not the current opportunity the company has found for 3D printed carbide. Instead, it delivers 3D printed carbide wear parts for applications in oil and gas, power generation and defense, among others — and material development efforts have focused on these applications as well.
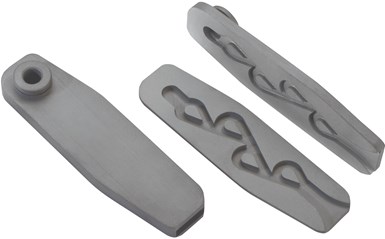
Much of Kennametal’s additive manufacturing work in wear-resistant materials such as tungsten carbide focuses on producing wear parts, such as this component for an energy-industry application. Photo: Kennametal.
During a recent visit to the company’s Latrobe, Pennsylvania, technology center, I spoke with two members of the AM team: Kennametal Additive Manufacturing General Manager Jay Verellen and Director of Advanced Machining and Additive Solutions Ed Rusnica. The different ways the company is advancing AM illustrate the various channels by which additive is finding opportunities in and around conventional manufacturing.
For Kennametal, they say, efforts in AM can be characterized as “powder, printed parts and [the company’s own] products.” These are three different pursuits, not all of them necessarily related to one another. Taking each on in turn:
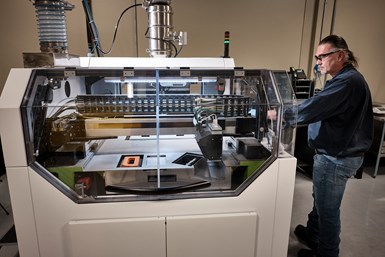
Tungsten carbide and Stellite powders have been adapted to binder jetting. The company has binder jetting capacity in Latrobe, Pennsylvania, devoted to contract production. Photo: Kennametal.
•Powder. The company develops tungsten carbide and Stellite powders adapted to 3D printing via binder jetting for its own part production efforts. An example is the company’s newly introduced KAR85-AM-K carbide grade. Targeted for wear parts in uses such as downhole oil and gas applications, this grade emphasizes corrosion resistance — particularly valuable for the downhole applications.
•Parts. For industries that can benefit from new design options in carbide hardware thanks to material such as the new grade, Kennametal also offers part engineering and production services on its array of binder jetting machines (from various providers) in Latrobe. Wear parts are a great application, as they are made in low quantities and subject to redesign according to the specific uses. By contrast, carbide cutting tools do not have this same suitability to 3D printing; they are frequently made in high volumes through molding and grinding, processes that remain unchallenged.
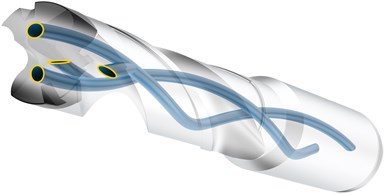
Additive manufacturing provides the way for the cutting tool maker to produce very small drill bodies with coolant passages through the tool. Photo: Kennametal.
•Products. Within Kennametal’s own cutting tool product line, the opportunity for AM is instead found in the tool bodies. 3D printing allows for precise curving and branching channels for cutting fluid inside of tool bodies that in some cases could not be achieved any other way. The company’s KenTIP FS line of modular drills, for example, includes tools 10 mm in diameter and smaller that employ through-tool coolant passages despite the small cross-sectional area of the tool, thanks to AM’s ability to economically create the small tool body with these passages inside. Notably, though, these tool bodies are made with a different process — powder bed fusion rather than binder jetting — and they are produced in Kennametal’s facility in Germany, not Latrobe. That is, Kennametal’s own AM production is an effort distinct from the AM opportunities it is realizing for other industries.
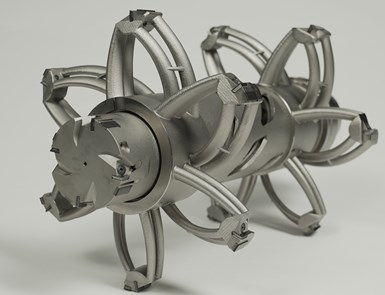
This 3D printed boring tool used to machine parts for electric vehicles was the subject of an episode of The Cool Parts Show.
Another, very different example of success in 3D printing a tool body involved a very large tool rather than a small one. A boring tool used to produce electric vehicle components was made 15 to 20 pounds lighter than it would otherwise need to be, in addition to accommodating branching internal coolant passages, all thanks to AM. We covered this development on The Cool Parts Show — see our episode on the Kennametal stator bore tool.
Read Next
3D Printed Tool for Machining Electric Vehicle Motors: The Cool Parts Show #39
Additive manufacturing achieves a large-diameter cutting tool light enough for fast, precise machining of the motor housing’s stator bore.
Read MoreKennametal KAR85-AM-K is Corrosion-Resistant Tungsten Carbide for Additive Manufacturing
KAR85-AM-K is said to combine the wear performance of conventional tungsten carbide with the design flexibility of 3D printing to produce high-performance parts for oil and gas, power generation and more.
Read MoreEstablishing a Process for 3D Printing Carbide
Using its experience making pressed and sintered carbide parts, Hyperion Materials & Technologies developed a new material, printing processes and sintering cycles for 3D printed carbide.
Read More