Automation Plus Capabilities Beyond Machining Featured at Mazak Event
Friction stir welding is one example of a capability for emerging applications that changes the scope of the machine tool. Here are observations from Mazak’s Discover 2023 event.
Share



The auto industry’s ongoing shift to electric vehicles is seen as a positive advance in many areas, but not for the business prospects of machining providers. EVs do not have the mechanical powertrain of an internal combustion vehicle, so manufacturing them does not involve the amount of machining of conventional cars. I raised this subject with Dan Janka, president of machine tool maker Mazak Corporation during a conversation at the company’s Discover 2023 event at Mazak’s North American headquarters in Florence, Kentucky.
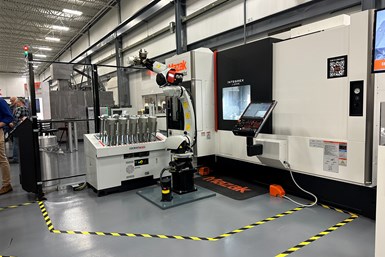
Mazak's showroom at its Discover 2023 event prominently featured automated machining solutions leveraging both multitasking and part handling automation.
Janka noted that, for his company, electrification is apt to be a net win.
He explained: Powertrain production is not a major application area for the company’s machines. Other machine tool makers have offerings specifically tailored to this need.
Meanwhile, for EVs, a joining technology — friction stir welding — holds significant promise. Welding without heat potentially provides a less costly way to seal battery housings. And Mazak offers technology for integrating friction stir welding into its CNC machining centers.
As a result, he says the company is now in active conversations with various auto OEMs evaluating integrated friction stir welding for EV production. The capability closes parts — and it opens doors.
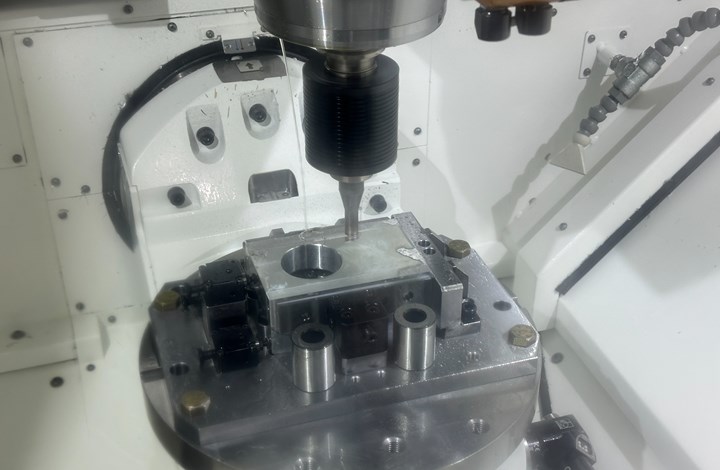
Friction stir welding is a capability Mazak is able to integrated into its machining centers. The process, seen in action here, joins abutting components without melting the metal.
Mazak’s Discover is a regular open house event for the company, and it therefore offers a regular opportunity to take the measure of the current moment that machining providers and the machining industry is experiencing. The item about electrification and its effect on machine tool use is one detail of this current time. Other details I noted from conversation with Janka, from his presentation and from other experiences of the event include the following:
Good Times? Hard Times? Challenges Balance Opportunities
President Dan Janka painted a picture of the challenges and opportunities currently facing machining providers.
Janka characterized the headwinds and tailwinds of the current moment in a presentation he gave to media members. The headwinds: Machine shops face rising costs on various fronts. Some of these costs have been building over time and others are newer.
For example, higher energy costs and interest rates affect the daily cost of operation. So do rising wages — though many shops wish they could pay them. More expensive than employment costs are the costs of having needed positions going unfilled because there is a lack of qualified applicants.
But despite it all, this a time of promise, he notes. “Reshoring and increased foreign investment are bringing opportunities for North American manufacturers,” he says. For the sake of stronger and shorter supply chains, there is greater interest in developing North American production than there has been at any time in recent memory.
Now Is the Post-COVID Age of Machining
Many manufacturers changed course or accelerated anticipated evolution during the pandemic. Today the pandemic as a daily reality is well past, and these companies are living out the results. Rather than returning to normal, affected businesses have been transformed.
The point came out during a panel discussion among job shop owners that was part of the event. HM Manufacturing president and CEO Nicole Wolter, one of the panelists, noted how “COVID really spurred our need to automate.”
Automation would have happened anyway for the company, albeit years later — incremental adoption was underway. But then the disruptions of the pandemic and what it revealed about both the value of skilled labor and the vulnerability of operations dependent on labor urged the company toward an embrace of automation that was more systematic and comprehensive, and faster in its advance.
Mazak proceeded through something similar, says Janka, and for an ironic reason. While the pandemic meant a shift to remote work for many people, it meant something like the opposite for the machine tool builder’s corporate and technical leadership. Travel was not possible.
Senior employees who might otherwise have been distracted with travel were in town, and were onsite to the extent that the protocols of the time permitted. The result was an opportunity to drive product development and corresponding organizational change that otherwise would have been slower in coming. “We used the pandemic,” Janka says.
Automation Demand Is at an All-Time High
Both points above explain this corollary point: Manufacturers of all sizes are now more interested than ever in investing in more unattended and less labor-dependent machining systems. For Mazak, this potentially means many things.
The company’s multitasking machine tools are inherently automated in that they permit more of the part’s machining to be performed in a single cycle with a single handling of the part. But automation also means integration with part handling such as robots, and the company is seeing more demand for machine tools sold as part of unattended systems in this way.
The need to embrace automation in part as a response to skilled labor shortages figures into Mazak's own processes as well. Its factory has come to increasingly rely on robotic welding, as seen here, due to a difficulty hiring personnel with this skill.
This demand to some extent changes the math of machine tool sales and purchasing. A more automated machine that can to some extent run unattended delivers more productive output per 24-hour day, so the number of machine tools purchased by a given shop may be lower while the average price of each machine is higher than it once might have been.
Manufacturers today are notably less focused on the number of machines or their pricetag compared to investing for the assurance of being able to expand productive capacity without needing to add employees.
Is a Machine Tool for Machining? Rethinking Part Making
Another member of the panel discussion, Faxon Machining CEO Bob Faxon, described a significant manufacturing improvement for a customer’s part his shop is pursuing, involving the redesign of housing to rely on welding via additive manufacturing along with CNC machining within a single uninterrupted cycle on a hybrid machine tool.
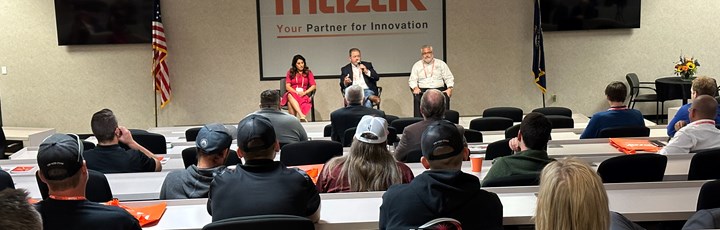
A job shop panel discussion at the event featured (left to right) Nicole Wolter of HM Manufacturing, Bob Faxon of Faxon Machining and Eric Metcalfe of RPM Carbide Die.
“Disruptive change is what we want,” Faxon said. “Process improvement on the order of 3 to 5 percent does not interest us as much. We can get 40 percent.”
Thinking such as this comes back to the case of friction stir welding cited above, and why this is a door-opener to the EV makers. CNC machine tools are already fast, precise and capable — they have been for years. Therefore, dramatic improvement does not come from simply going faster on these advanced machines.
Mazak’s hybrid machine tools incorporate hot wire deposition, additive manufacturing via powder metal deposition, friction stir welding and gear cutting. Next-level process improvement on the order of Faxon’s 40 percent comes from something like this: added capabilities beyond milling, drilling and turning that significantly expand the scope of what a single unattended cycle on the machine tool is able to accomplish.
Related Content
Investing in Automation, Five-Axis to Increase Production Capacity
To meet an increase in demand, this shop invested heavily in automation solutions and five-axis machines to ramp up its production capabilities.
Read MoreCutting Part Programming Times Through AI
CAM Assist cuts repetition from part programming — early users say it cuts tribal knowledge and could be a useful tool for training new programmers.
Read MoreWhich Approach to Automation Fits Your CNC Machine Tool?
Choosing the right automation to pair with a CNC machine tool cell means weighing various factors, as this fabrication business has learned well.
Read MoreUsing the Toolchanger to Automate Production
Taking advantage of a feature that’s already on the machine tool, Lang’s Haubex system uses the toolchanger to move and store parts, making it an easy-to-use and cost-effective automation solution.
Read MoreRead Next
Registration Now Open for the Precision Machining Technology Show (PMTS) 2025
The precision machining industry’s premier event returns to Cleveland, OH, April 1-3.
Read More5 Rules of Thumb for Buying CNC Machine Tools
Use these tips to carefully plan your machine tool purchases and to avoid regretting your decision later.
Read MoreSetting Up the Building Blocks for a Digital Factory
Woodward Inc. spent over a year developing an API to connect machines to its digital factory. Caron Engineering’s MiConnect has cut most of this process while also granting the shop greater access to machine information.
Read More