6 Factors Maximize Profitability in High-Precision Machining
Jon Iverson, CEO of Optis says it is important to take an integrated approach to improving manufacturing performance. Here are six key considerations that should form an integral part of the manufacturing strategy.
Share




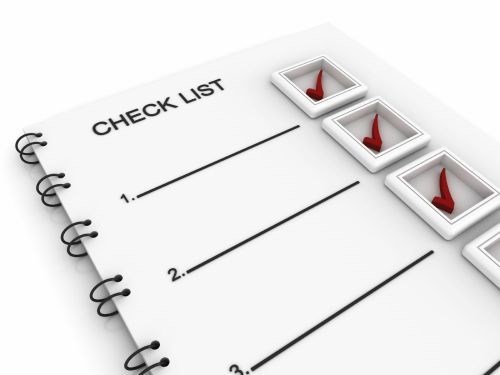
To remain competitive, manufacturers need to find ways to eliminate unplanned downtime, minimize scrap rates, ensure consistency and produce high-performance precision parts at a reasonable price. According to Optis, a joint venture that brings together the machining expertise, analytic tools and process improvements of TechSolve with the heritage of Castrol, OEMs currently demand between a 3 to 5 percent reduction in costs for their parts each year and they expect each supplier to achieve or exceed these targets.
Jon Iverson, CEO of Optis says it is important to take an integrated approach to improving manufacturing performance and lists six key considerations that should form an integral part of the manufacturing strategy. Those considerations include machine tools, cutting tools, work material, cutting fluid, machining accessories and machining parameters.
An integrated, holistic approach that considers and optimizes all six factors will lead the manufacturer to a more profitable state of operations, Mr. Iverson says. By thoroughly understanding and acting on these elements, he says manufactures can overcome many of the primary barriers to competitiveness and compliance.
Machine tools
This is the most significant factor in machining a part with high precision and consistent quality. Of today’s manufacturers, 8 percent actually under-utilize their current machine tools as they are lacking a scientific approach to optimization.
Cutting tools
Extending tool life should be a key consideration when selecting cutting tools. While cutting tool manufacturers continue to strive for better quality and consistency, the manufacturing industry at large can take advantage of advancements to look for solutions with tailored cutters, improved toughness, wear and thermal resistance.
Work material
The precision required to be maintained during machining is reliant upon the work material to be machined. The material’s mechanical and thermal properties play a critical role in the selection of the machine tool, cutting tool and establishing the optimum machining parameters. All must be considered holistically to achieve and consistently produce the best results.
For instance, while aluminium alloys can be machined at much higher speeds and feeds, materials such as titanium and nickel-based alloys have low thermal conductivity and high chemical affinity with tool material at higher temperatures. Therefore, they are machined at much lower cutting speeds and demand machine tools with high rigidity, horsepower and torque capabilities. The heat generated during cutting is proportional to cutting speed and does not dissipate quickly in machining such materials.
Cutting fluid
A key opportunity to reduce costs and improve performance lies in the utilization of the optimum cutting fluid. Many factors play into the proper selection of cutting fluid, which, done correctly, will achieve a better material removal rates and surface finish.
As environmental regulations get increasingly stringent, proper disposal methods are also critical. Even new technology such as minimum quantity lubrication (MQL) needs to be considered.
Machining accessories
An effective part process and workholding design can make the part-making process faster, more accurate and ultimately, more profitable. However, this relies on technology scouting and a culture of continuous improvement.
Machining parameters
The final major factor is the machining parameters. Speed, feed depth of cut and cutter path are all essential considerations to machining precision parts, and manufacturers should apply performance based optimization to continuously improve.
Read Next
5 Rules of Thumb for Buying CNC Machine Tools
Use these tips to carefully plan your machine tool purchases and to avoid regretting your decision later.
Read MoreRegistration Now Open for the Precision Machining Technology Show (PMTS) 2025
The precision machining industry’s premier event returns to Cleveland, OH, April 1-3.
Read MoreBuilding Out a Foundation for Student Machinists
Autodesk and Haas have teamed up to produce an introductory course for students that covers the basics of CAD, CAM and CNC while providing them with a portfolio part.
Read More