5 Big Themes in Additive Manufacturing at Formnext Forum: Austin
Formnext Forum: Austin, a two-day event at the end of August focused on additive manufacturing for production, includes a conference exploring important ideas in AM related to supply chains, bridge production, enterprise transformation and more.
Share




The central, major theme in additive manufacturing (AM) is its ongoing advance into production. Industrial 3D printing encompasses a broad range of part-making technologies (binder jetting, directed energy deposition, powder bed fusion and more), but as these technologies advance, their numbers improve — numbers related to speed, repeatability and cost. Each incremental improvement of these numbers opens wider the potential applications for additive as an option specifically for batch or scale production. As this advance rolls on, it raises up themes specific to AM for production that are worth seeing and exploring.
At the end of August, I will be part of the team hosting a new event exploring these themes. Formnext Forum — Austin, Texas, August 28-30 — is a two-day conference and expo event (starting with an evening reception on the 28th) focused on AM for production. The event’s co-organizers include the hosts of Formnext, the world’s biggest additive manufacturing trade show; AMT — The Association For Manufacturing Technology (organizers of IMTS); and Gardner Business Media, the publisher of this magazine. The event is not just for current users of additive manufacturing, but rather for those expecting to advance with it — including manufacturing leaders who sense or know that additive manufacturing is likely to be a part of their production in the future. If that’s you, please join us.
And further, when you register for Formnext Forum, consider joining us at the “All Access” level. Attendees at this level will enjoy the entire span of our conference sessions. Formnext Forum’s conference is where we will explore these big ideas in additive, and how manufacturing organizations are engaging with them.
Here are the themes I mean — what I see as I look to the most prominent successes and changes 3D printing is bringing to production. As manufacturing advances with additive, the advance increasingly emphasizes all of the following:
1. Bridge Production
Additive does not need to take on all the production in order to transform it. The most lucrative win from additive is often in the chance to begin producing right now, while some other process waits to come online. “Bridge production” is the term for this. In a notable recent success, GM employed this approach for a Chevy Tahoe component resulting from a late redesign. Weeks would pass before GM could obtain the needed injection mold tooling, so the company mass-produced the component by the thousands through 3D printing. Additive manufacturing may offer a lower production speed than molding, but it also offers a lower wait time, so why not use them in tandem? Many manufacturers are seeing the value of AM as a bridge.
Formnext Forum speaker: Andrew Roderick, additive senior applications engineer with Extol, “Understanding the Value of AM’s Bridge Production Opportunity.”
2. Supply Chain Reinvention
The chance to produce low-quantity parts with little prep time or setup, as they are needed, potentially reduces the number of parts that need to be made in a faraway location and shipped to wait in warehouses. One potentially big winner of a change like this is the oil and gas industry, whose drilling operations go through many hardware components that begin as forgings, and therefore involve long lead times. If much of this hardware can be made via AM instead, it could save a billion dollars or more for this sector in inventory costs. I will have a conversation on-stage with a representative of one major producer aiming to build an additive manufacturing supply chain for oil and gas.
Formnext Forum speaker: Carlo De Bernardi, AM lead with ConocoPhillips, “Current and Future State of AM in the Oil & Gas Industry.”
3. The New AM Factories
One of the most fundamental disruptions playing out in additive manufacturing involves the question of what kind of organization and facility is best suited to carry AM ahead into production. A new category of manufacturer includes companies founded and organized primarily around additive manufacturing, some of which are companies using their own proprietary AM processes for production. An example of a company like this is one of Formnext Forum’s sponsors, Seurat Technologies — the inventor and provider of a new, accelerated method of laser powder bed fusion delivering low part production costs. I will be joining this company’s co-founder for an on-stage conversation as well.
Formnext Forum speaker: James DeMuth, CEO and co-founder of Seurat Technologies, “How to Manufacture 25 Tons of Metal Per Year, Sustainably.”
4. Enterprise Transformation
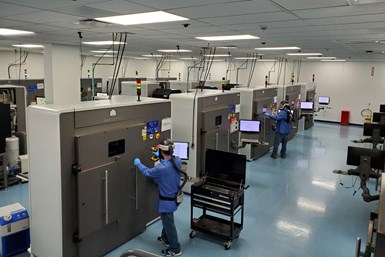
RMS is in full production of medical implants made through laser powder bed fusion, but getting to this also involved establishing a separate machining department for additive. Troy Olson of RMS will discuss the company’s additive journey at Formnext Forum: Austin. Photo: RMS
Additive manufacturing is more than 3D printing, which means it involves more than buying a 3D printer and making parts on it. AM necessarily involves realizing the full design freedom of additive by more closely connecting design and manufacturing, and realizing the full process streamlining of additive by consolidating adjacent parts and downstream steps into one additive build. Additive manufacturing thus touches and affects the departments and operations all around it. RMS discovered this — the medical device maker is very successful producing implants through machining, but realized it needed to organize machining a different way once it began to also succeed with additive.
Formnext Forum speaker: Troy Olson, director of operations for the Additive Manufacturing Division of RMS, “Powder to Package: RMS’s Journey Into Additive Manufacturing for Medical Devices.”
5. Enterprise Adoption
In part due to the way the transformations of additive reach throughout the enterprise, the most universal theme in AM for production is probably the ongoing effort by manufacturers to win through to increasingly successful adoption. Success with additive is a matter of technology, procedure and process, to be sure — it is every bit as much a matter of culture, organization and vision as well. Major manufacturer Eaton now has a South Carolina additive manufacturing facility producing aerospace components for customers, with many of those parts having been converted to additive from casting — but the company didn’t arrive at this success quickly. Eaton stayed true to a path of consistently building on its additive wins and learning over time.
Formnext Forum speaker: Mike York, director of additive manufacturing for Eaton Aerospace, “Eaton’s Additive Journey: Leveraging AM to Produce Superior Products and Solutions.”
I hope you join us. One other benefit: Formnext Forum is as much a networking event as it is a conference and expo. Experts including all the speakers above and about 40 others will be present throughout the event, and accessible. Other attendees will also have their own experiences of the themes above. As a result, I expect attendees will learn a great deal from the conference we have organized, but then I expect they will also learn a considerable amount through the contacts and conversations they engage in on their own. Come be part of this event. Registration information for Formnext Forum can be found at https://www.formnextforum.com/.
Related Content
6 Trends in Additive Manufacturing Technology
IMTS 2024 features a larger Additive Manufacturing Pavilion than ever before, with veteran suppliers alongside startups and newcomers at the front of the West Building. As you browse these exhibitors, as well as booths found elsewhere at the show, keep an eye out for these trends in AM.
Read MoreA Fond Farewell to My Additive Friends
In his final “Additive Insights” column, Tim Simpson reflects on how additive manufacturing has progressed in the last six years. Standards and software are two examples.
Read MoreDigital Thread Enables First-Time-Right 3D Printing
Connecting all stages of manufacturing, from design to postprocessing, helps break down barriers to industrializing additive manufacturing.
Read MoreHow to Meet Aerospace’s Material Challenges and More at IMTS
Succeeding in aerospace manufacturing requires high-performing processes paired with high-performance machine tools. IMTS can help you find both.
Read MoreRead Next
Setting Up the Building Blocks for a Digital Factory
Woodward Inc. spent over a year developing an API to connect machines to its digital factory. Caron Engineering’s MiConnect has cut most of this process while also granting the shop greater access to machine information.
Read MoreBuilding Out a Foundation for Student Machinists
Autodesk and Haas have teamed up to produce an introductory course for students that covers the basics of CAD, CAM and CNC while providing them with a portfolio part.
Read More5 Rules of Thumb for Buying CNC Machine Tools
Use these tips to carefully plan your machine tool purchases and to avoid regretting your decision later.
Read More