Additive Advances Highlighted at Grand Opening
GF Machining Solutions put its technology on display for its North American customers, highlighting advances in EDM spark monitoring and support for additive manufacturing technology.
Earlier this month, GF Machining Solutions (GFMS) provided some of its North American customers with tours of its facilities in Europe, including its EDM factory in Losone, Switzerland, and the brand new milling factory in Biel, Switzerland. Guests were present for the grand opening of the Biel facility, in addition to enjoying talks on the new technologies that are being explored at both facilities.
Controlling Sparks to Improve EDM Wire Life
One of the major developments that the company displayed at its Losone facility was its new Spark Track monitoring system. By adjusting the the rate and intensity of sparks, the software is able to prevent heavy wear from concentrating at any one point along the wire, extending the life of the wire and preventing breaks. To accomplish this, the company designed Spark Track with the Intelligent Spark Protection System (ISPS) to more accurately identify the intensity and location of sparks along the wire. This enables it to adjust current and voltage to prevent the concentration of wear on the wire.
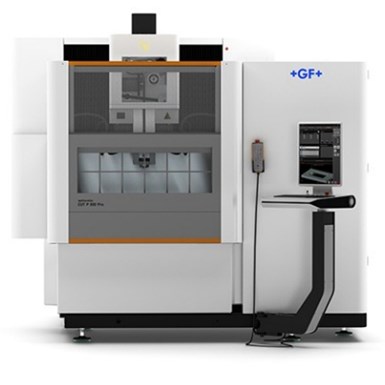
GF Machining Solutions has updated its EDM offerings to improve wire life and cutting speed. The company’s Spark Track technology improves wire life by regulating the strength and location of sparks along the wire, preventing breakages.
According to the company, ISPS prevents wire breaks, eliminating time-intensive resets and reducing the amount of time an operator has to dedicate to a given job. This not only frees the operator to work on other jobs, but also provides cost savings to the shop. On top of that, the extended wire life provides even more savings.
Another step the company took to better regulate the spark output of its machines was to standardize the generators for all its EDMs. The company also redesigned its machines to place the generator as close to the wire as possible. Doing this makes the machine as reactive to input from the control as possible by reducing the distance computer signals and sparks need to travel.
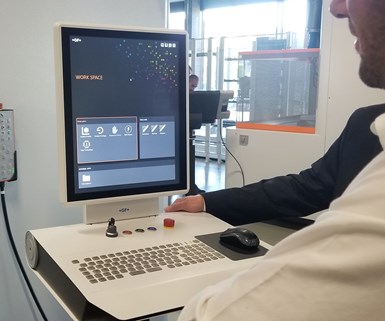
The Uniqua control is designed to have an user-friendly graphical interface that makes multiple features available from a single menu screen. It uses Spark Track and ISPS to protect the wire and improve wire cutting speeds by 14-to-28%.
To further take advantage of the increased monitoring capabilities, the company also developed a controller capable of using the data to improve outcomes. The Uniqua control not only uses the improved monitoring to protect the wire, but also uses it to maximize the speed of erosion from the wire. According to the company, it improves wire cutting speeds by 14-28% in the Cut P series of wire EDMs.
Additionally, the control is designed to have a user-friendly graphical interface. The design enables users to access multiple features from a single menu screen, which GFMS says provides easier navigation and improves the user experience.
Leaning Into Additive Manufacturing
Another highlight of the event was GFMS’s pivot toward additive manufacturing (AM). The company has partnered with 3D Systems to provide the DMP Flex/Factory 350, a modular powder-bed fusion (PBF) system capable of printing metal parts in a variety of materials including steels as well as alloys of nickel and titanium. The DMP Flex 350 is designed for producing small batches for R&D, while the DMP Factory 350 is suitable for full-scale production.
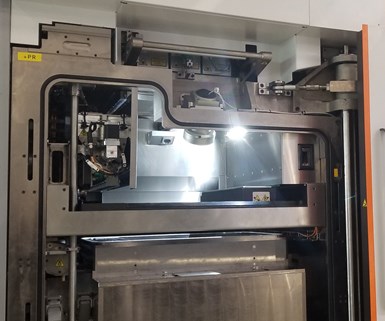
GF Machining Solutions and 3D Systems partnered to develop the DMP Flex/Factory 350 — a modular machine that uses powder-bed fusion and is capable of printing metal parts in a variety of materials, including steels as well as alloys of nickel and titanium. The modular base plates enable users to print multiple batches without slowing to clean the work area.
Both versions of the company’s flagship AM solution make use of base plates that function as removable powder beds. Before each build, the user inserts a base plate loaded with the appropriate material into the machine and begins the PBF process. Once it is finished, the user removes that base plate to clean off loose material and cut the parts off of it, inserting the next base plate for the next batch of parts. This enables the user to maintain a constant stream of parts moving through the process, side-stepping the need to clean the work area and improving the rate of production.
Another entry point into the AM world is the Cut P Pro, a horizontal wire EDM the company designed to quickly and easily cut 3D-printed metal parts away from their base plates. The machine takes full advantage of Uniqua and the Spark Track monitoring technology, providing reliable, efficient cutting. Additionally, the machine is designed to make it easy to load a base plate into the work area, minimizing setup.
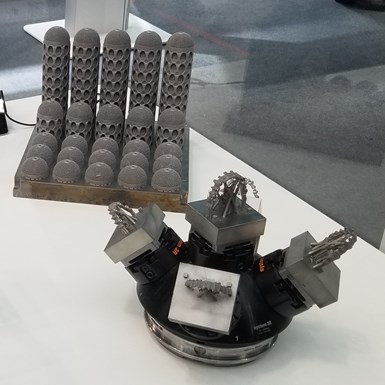
At EMO this year, GF Machining Solutions displayed examples of how AM enables approaches to part manufacturing that would be unthinkable any other way. Pictured, the top left example shows how densely packed a build can be, stacking 50 medical implants in a small area. In the bottom-right, complex parts were printed on a base plate, which can be transferred to a five-axis machining center for finishing.
This pivot toward AM demonstrates that the technology is moving far beyond jigs and fixtures. As a growing presence in the realm of full-scale part production, OEMs like GFMS are recognizing the need to provide meaningful improvements for AM applications. The focus of the Cut P Pro is complementary to AM production because AM production is no longer a possibility, but rather a reality — one that manufacturers must contend with.
Related Content
How to Mitigate Chatter to Boost Machining Rates
There are usually better solutions to chatter than just reducing the feed rate. Through vibration analysis, the chatter problem can be solved, enabling much higher metal removal rates, better quality and longer tool life.
Read MoreQuick-Change Tool Heads Reduce Setup on Swiss-Type Turning Centers
This new quick-change tooling system enables shops to get more production from their Swiss turning centers through reduced tool setup time and matches the performance of a solid tool.
Read MoreInside the Premium Machine Shop Making Fasteners
AMPG can’t help but take risks — its management doesn’t know how to run machines. But these risks have enabled it to become a runaway success in its market.
Read MoreThe Future of High Feed Milling in Modern Manufacturing
Achieve higher metal removal rates and enhanced predictability with ISCAR’s advanced high-feed milling tools — optimized for today’s competitive global market.
Read MoreRead Next
Talk About 5G Is No Idle Chatter
Near-real-time machining vibration compensation is just one advantage of the latest networking technology.
Read MoreCAM Simulation Gets Toolmaker up to Speed with B-Axis EDM
Software simulation helped this machine shop learn how to program its new advanced, high-tolerance wire EDM. The software also helped the shop turn job quotes around quickly.
Read MoreA Machine Shop Poised for Additive Production
By laying the groundwork now, Able Tool will be prepared for the day when machine shops are commonly called to produce metal parts via additive manufacturing.
Read More