Dollars and Sense
Not every streamlining project requires huge modifications to your production line. Sometimes taking a close look at how basic tasks are currently being performed can lead to simple, cost-effective improvements.
Share







ECi Software Solutions, Inc.
Featured Content
View More
One way to save money on the shop floor is simply to use common sense. You may not realize it, but all the tiny delays add up to a ton of lost time, as do habits formed over the years that have gone unquestioned.
Allan Arch, president of Southern Gear & Machine in Miami, Florida, began looking more closely at his own operations recently. Here are just a few of the changes he’s made:
- After cutting his own barstock for years, Mr. Arch mentioned to his supplier what a time-consuming process it was. “Even though we had two saws running, it was basically a non-stop operation to get all of the barstock cut,” he says. His supplier offered to deliver the materials pre-cut. “They have saws that can handle a job that would take us all day in a matter of minutes. We’d just gotten used to the way things were and had never thought to ask if there were a better way.”

Southern Gear’s supplier can pre-cut barstock for a fraction of the cost, and in minutes rather than the hours required by the company’s own saws.
- Despite efforts to keep it orderly, the company’s tool crib had gotten messy over the years, so Mr. Arch and his colleagues developed an assignment for two of their summer interns. “As soon as they arrived they had a project to tackle,” he explains. “We showed them what we had, told them what we wanted and gave them all the resources they needed.” The result is a neat, color-coded storage area where it’s not only easy for workers to find the supplies they need, but it doesn’t take a lot of effort to keep straight. “We literally saved months of lost time in the first few weeks that we had this new system in place,” Mr. Arch says.

Assigning interns to tackle revamping the company’s tool crib resulted in great experience for the students and an orderly system for the company.
- Even better than an organized tool crib is a management system that makes tooling available to machine operators on the shop floor. New models do not require access cards, instead allowing users to obtain the tools they need by entering a password on a removable touchscreen. Southern Gear chose two Matrix Series 5 units—a “mini” and a “maxi”—from Ingersoll Cutting Tools for different areas of operation. “These devices bring the tools to the manufacturing area where workers can get to them easily while at the same time helping us monitor our stock levels, calculate CPU and estimate tool life.”
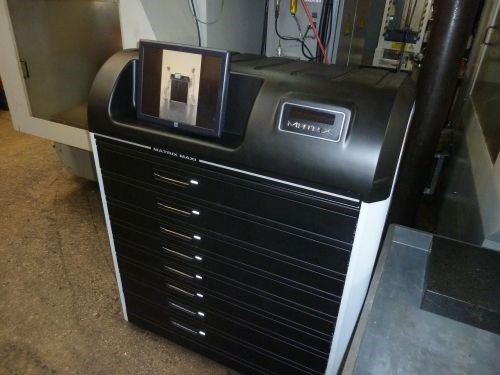
Tool management systems such as this provide much more than storage and convenience, also tracking stock levels and even tool wear.
Read more about Southern Gear’s approach to streamlining operations in the August issue of Gear Production, a supplement to Modern Machine Shop magazine.
Related Content
-
Can AI Replace Programmers? Writers Face a Similar Question
The answer is the same in both cases. Artificial intelligence performs sophisticated tasks, but falls short of delivering on the fullness of what the work entails.
-
Orthopedic Event Discusses Manufacturing Strategies
At the seminar, representatives from multiple companies discussed strategies for making orthopedic devices accurately and efficiently.
-
6 Machine Shop Essentials to Stay Competitive
If you want to streamline production and be competitive in the industry, you will need far more than a standard three-axis CNC mill or two-axis CNC lathe and a few measuring tools.