Adjusting Supply Chains in U.S. Manufacturing
Sponsored ContentAs the novel coronavirus presents challenges for manufacturers and new opportunities for suppliers, manufacturers should not miss the chance to strengthen their supply chains.
Share
The COVID-19 pandemic has led to some heroic contributions from American manufacturers that have quickly pivoted to making necessary equipment and supplies to combat the virus. However, it has also revealed serious supply chain issues that must be addressed beyond the medical industry if we hope to protect our country and economy from future disruptions in parts and equipment supply. “This pandemic did not create the supply-chain problems people are experiencing,” says the President of AMT – The Association For Manufacturing Technology Douglas K. Woods. “It’s just exposing them.”
Perhaps for the first time since World War II, major television networks are routinely discussing America’s supply chain due to COVID-19. At AMT, however, advising industry on how to strengthen supply chains is part of its core mission. For example, AMT led an Advanced Manufacturing Workshop in January 2018 to support President Trump’s Executive Order 13806 (EO 13806), Assessing and Strengthening the Manufacturing and Defense Industrial Base and Supply Chain Resiliency of the United States. EO 13806 directed a whole-of-government approach, led by the Secretary of Defense, to asses and strengthen the industrial base. The workshop included a diverse group of AMT members (both U.S. and international companies with a large U.S. presence), AMT Staff and members of Gardner Business Media. The group identified challenges and made recommendations related to U.S. industrial base readiness and the country’s ability to produce machine tools, control systems and a skilled workforce.
“The workshop was noteworthy because we reiterated the need for an advanced manufacturing policy, with specific emphasis on innovation and leveraging transformative technologies,” explains Woods. “This focus guarantees that our government is targeting our resources and investment for the best long-term outcomes.”
The EO 13806 report makes it clear that the current state of manufacturing supply chains harm the country’s ability to maintain defense readiness and that the need for solidifying them is a matter of national importance. Simply put, improving manufacturing’s U.S. supply chains improves the industry’s ability to supply parts for every other industry in the case of sudden, urgent needs.
Thankfully, investing in strengthening the U.S. manufacturing infrastructure has bipartisan support, as it provides tremendous benefit to the economy. Every industry in the U.S. fundamentally relies on discrete parts that have been manufactured, which means that the health of the manufacturing industry directly relates to the health of the entire economy. As AMT Chief Knowledge Officer Patrick McGibbon puts it, “Every dollar invested in manufacturing generates $3.74 in total GDP. Its closest competitor is 20% less effective in multiplying value.”
But with manufacturing being so critical to our economy, to our health and safety, and to our national defense, how did our manufacturing infrastructure get to this point?
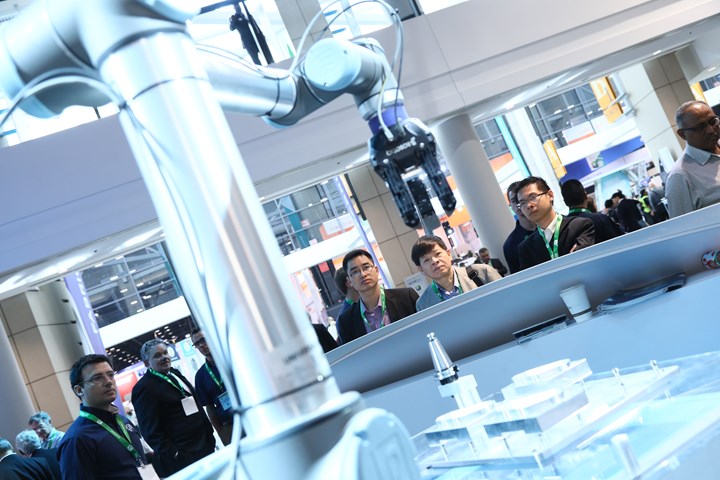
Automation, such as this demonstration of a robot changing tooling, is essential for increasing manufacturing competitiveness.
How We Got Here
According to Woods, the erosion of our manufacturing base can be traced back to the business practices of the 70s and 80s. During this period, there was a combination of large machine tool and manufacturing companies that went public to raise funds, as well as a lot of investment banking funding “roll-ups” and mergers. “The net result was a dramatic over emphasis on quarterly results and not enough focus on or investment in R&D and innovation,” says Woods.
In some cases, machine tool companies allowed their deliveries to go to over a year for standard machines, as they had little global competition and could drive up prices with limited supply and high demand. The combination of rising prices, longer deliveries and minimal investment in new technology opened the door for foreign manufacturers to grab market share.
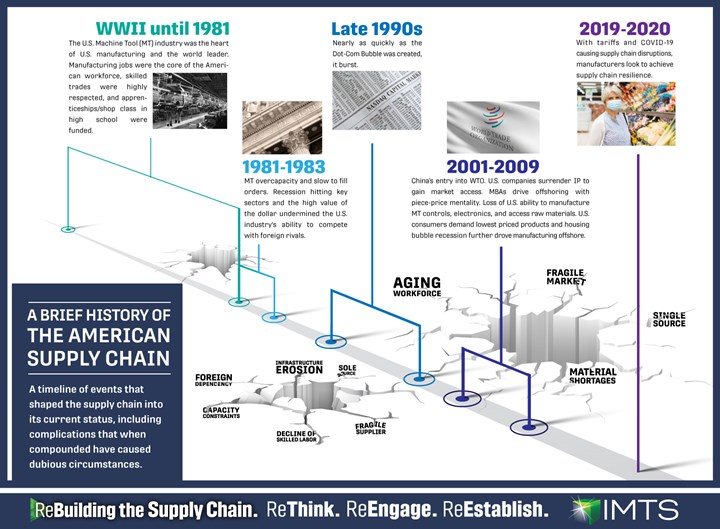
This is a timeline of the events that have shaped the current state of the supply chain in U.S. manufacturing. As it shows, numerous factors have eroded the supply chain’s ability to adapt to changes and disruptions in the market. Click to enlarge.
“This created a downward spiral of cost cutting, layoffs of veteran talent and erosion of the knowledge base. Eventually, many of the iconic U.S. machine tool companies were dramatically downsized, broken into small pieces and sold off or shuttered for good.”
During this period, other countries’ machine tool makers were continuing to improve their technology and ramp up volumes to break into the U.S. manufacturing market, which worked. “It was the distributors who maintained the relationships with customers,” says Woods. “When U.S. machine tool makers stopped being responsive to their customer’s production needs, the distributors found companies that could satisfy their capital needs.” The high value of the dollar and lack of a value-added tax put U.S. companies at an approximate 30 percent price disadvantage compared to Japan, further exacerbating the situation.
Additionally, the push toward quarterly profits incentivized OEMs to outsource production as a cost-cutting measure. “As OEMs chased low-cost labor, a huge chunk of American manufacturing followed,” says Woods. However, this strategy, in practice, does not work as well as the financials might suggest. “When you outsource your supply chain and all of those jobs to low-wage countries, eventually those ‘low cost’ wages will steadily rise,” says Woods. “At some point, you end up with not only much higher labor costs, but expensive shipping costs and inherent risks of global supply chains.”
The largest impact has been felt in the automotive sector, but aerospace, electronics, consumer goods and more have all been affected. With such widespread loss of manufacturing infrastructure, it can be daunting to think about strengthening it, but that is precisely the task that AMT has set for itself.
The Effects of Bolstering the Supply Chain
AMT has been working for years to advocate for manufacturing in the U.S. “The good news is that everyone finally seems on board with rethinking their supply chain strategy,” says AMT Vice President and Chief Exhibitions Officer Peter Eelman. “However, we cannot rebuild the supply chain by next Thursday, and we are never going to reclaim every job that has been offshored. What we’re advocating for is a rational approach to reshore work where it makes good business sense as a result of correctly calculating total costs and when it is of national interest to have the work done in the U.S.”
According to Harry Moser, president and founder of the Reshoring Initiative, companies that offshore are often failing to factor the costs of overseas production, including shipping times, inventory carrying cost, intellectual property protection, quality, warranty, service costs and environmental impact. “Often, it’s more profitable to produce in the local market than to ship to the market,” he says. “And it goes that way for other countries. If GM wants to build a plant in China to serve the Chinese market, I don’t even consider that offshoring.” With a market the size of the U.S., manufacturing can be highly profitable, in addition to being key to rebuilding important supply chains.
In addition to profitability, shoring up local supply chains in the U.S. provides flexibility. The U.S. is a big market, and major disruptions such as the COVID-19 pandemic can disrupt major industries, interrupting the flow of supplies and shortening the production process. “OEMS are finding their business disrupted in a major way,” says Eelman. “By securing local production, shortening shipping times, and eliminating borders and customs as barriers, OEMs can prevent major crises from halting production.” This relates closely to the concerns raised in the EO 13806 report, which notes the potential strains that global crises can create when supply lines stretch across the globe.
How the Government Can Help
But what does rebuilding the supply chain actually look like? For starters, a secure supply chain needs smart workers with the right skills using the right technologies to reduce the cost of production and improve competitiveness. Accordingly, education plays a prominent role.
“We need to convince the government to invest in manufacturing education and convince people that manufacturing can provide successful career opportunities, like we know it can,” says Eelman. Investments such as providing access to apprenticeship programs or funding manufacturing schools that emphasize new and digital technologies can go a long way toward improving the workforce.
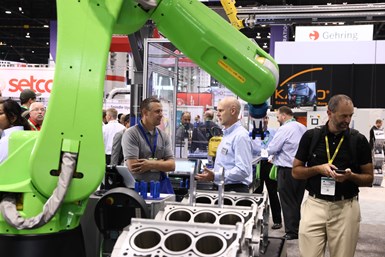
Cobots make manufacturing jobs more attractive by relieving workers from repetitive or stressful tasks. Improving the efficiency of U.S. manufacturing and attracting workers to manufacturing jobs are essential to improving the American supply chain.
Additionally, shoring up the supply chain will mean improving access to capital equipment, especially for small to midsize manufacturers. “The government must provide tax incentives for midsize firms to purchase equipment that ultimately makes them more productive and more profitable,” says Woods. He cites the need to make 100% bonus depreciation permanent. The provision, enacted as part of the Tax Cut And Jobs Act (TCJA) of 2017, is temporary and begins phasing out in 2023 until expires at the end of 2026.
By using tax incentives like bonus depreciation, Sec. 179 expensing, and the R&D tax credit to create opportunities for small and medium-sized manufacturers to invest in technology solutions, the government can encourage job creation and economic growth. Likewise, improving access to data-centered capital such as machine monitoring can greatly improve the profitability of U.S. manufacturing, further increasing the desirability of manufacturing around the country. Digital technology, in particular, promises to add to the flexibility of manufacturing by enabling shops to improve various aspects of their manufacturing process.
Finally, by providing additional R&D incentives, the government can encourage long-term investments in U.S. manufacturing. These investments pay dividends in helping manufacturers to stay competitive as technology grows and changes. Additionally, this approach to tax policy counters the short-term incentives that led to the greatly reduced manufacturing infrastructure of the past.
How AMT Can Help
Shoring up the U.S. manufacturing supply chain has been a focus of AMT for years. In addition to hosting events that address the issue, the association serves as a networking hub that connects manufacturers. “We want to connect part makers to part buyers,” says Eelman. “Both in our capacity as a trade association and through events like IMTS – The International Manufacturing Technology Show, we hope to provide opportunities for these groups to interact and do business.”
AMT has partnered with the Reshoring Initiative to help manufacturers looking to strengthen their supply chains. The association is providing manufacturers with resources and contacts to improve their local supply chains and recover from any disturbances caused by COVID-19. AMT also hosts educational seminars and provides consulting services to enable manufacturers to improve their businesses.
The association also aggressively pursues its Manufacturing Mandate, a group of policy recommendations designed to improve the manufacturing landscape of the U.S. This includes efforts to secure tax incentives for capital purchases and R&D, pursue educational and training services to build a manufacturing “Smartforce,” and improve global competitiveness through policies that level the playing field for American manufacturers. These policies are aimed at creating better connections between manufacturers and governments, encouraging a healthier manufacturing environment for suppliers and OEMs alike.
IMTS had already taken action to help manufacturers address supply chain issues created by COVID-19. The IMTS supply-chain microsite – ReBuilding the Supply Chain – shows OEMs how to rethink their current operations, how they can reengage with suppliers and secure trading partners and how they can reestablish connections for a more localized industrial base. It includes a brief history of why the supply chain disruption occurred, and IMTS has mapped out future content to show steps that can be taken to secure the supply chain moving forward.
Through these initiatives, AMT is working to support and improve manufacturing within the U.S. Learn more at IMTS.com/SupplyChain and AMTonline.org.