A Dramatic Debut and Key Collaborations at the Paris Air Show
News announcements by aerospace manufacturers and suppliers flew fast and furious throughout the Paris Air Show, but — at least for this writer — the long-awaited debut of the world’s largest engine and a series of announcements by Oerlikon took center stage.
Share






Takumi USA
Featured Content
View More.png;maxWidth=45)
DMG MORI - Cincinnati
Featured Content
View More
ECi Software Solutions, Inc.
Featured Content
View More
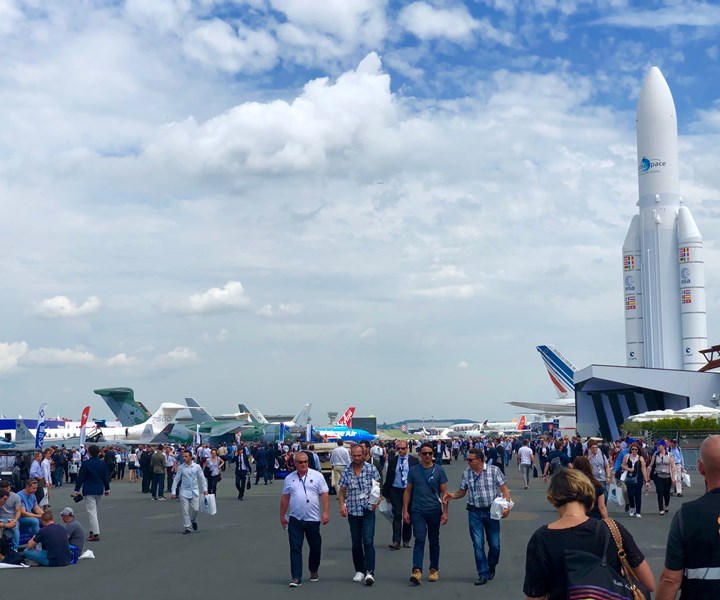
The biennial Paris Air Show is the aviation world’s signature event. This year, 315,000 visitors — including 276 official delegates from 98 countries — took in 2,453 exhibitions and signed roughly $140 billion worth of contracts and letters of intent.
Soaring aerobatics, multi-billion-dollar deals and extensive displays of aerospace technology make the biennial Paris Air Show the aviation world’s signature event. This year, 315,000 visitors — including 276 official delegates from 98 countries — took in 2,453 exhibitions and signed roughly $140 billion worth of contracts and letters of intent. While the rivalry between Boeing and Airbus typically dominates headlines at the show, that rivalry was clouded by recent headlines surrounding Boeing’s 737 MAX after two recent crashes grounded the aircraft worldwide. While the two largest aerospace manufacturing companies in the world ended up securing a healthy $78 billion in orders — $34 billion for Boeing and $44 billion for Airbus — each was eclipsed by a record haul for GE Aviation.
GE Aviation Announces GE9X
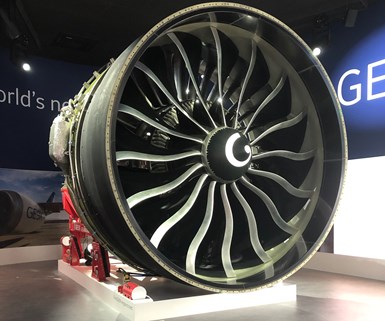
On the Paris Air Show’s opening day, David Joyce, GE Aviation’s president and CEO, debuted the GE9X engine to a packed room in the company’s pavilion near the Le Bourget airfield. The engine is a massive high-bypass turbofan that boasts 304 additively manufactured parts integrated into seven multi-part structures.
On the show’s opening day, David Joyce, GE Aviation’s president and CEO, debuted the company’s GE9X engine to a packed room in the company’s pavilion near the Le Bourget airfield. The engine, which served as the cover feature of our special edition publication about next-generation aerospace manufacturing (more on that below), is a massive high-bypass turbofan that boasts 304 additively manufactured parts integrated into seven multi-part structures. The GE9X — the largest, most fuel-efficient engine the company has ever produced — represents the first time the company has placed multiple additive manufacturing (AM) materials and modalities into production toward a single aviation application, creating what the company calls a first-of-its-kind industrialized aerospace supply chain for AM.
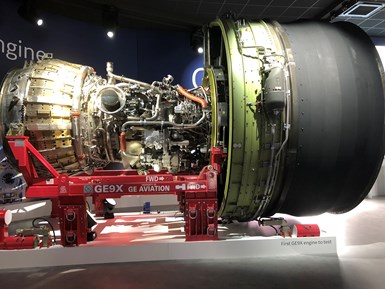
The GE9X is the largest, most fuel-efficient engine the company has ever produced.
As the GE9X awaits certification from the Federal Aviation Administration, GE Aviation’s record show sales stemmed from its 50-50 partnership with France’s Safran Aircraft Engines. This joint venture, called CFM International, secured most of its earnings from a low-cost Indian airline called IndiGo, which ordered 280 of GE’s Leading Edge Aviation Propulsion (LEAP) 1A engines, as well as AirAsia, which agreed to purchase 200 of the same model.
Oerlikon’s Two Announcements
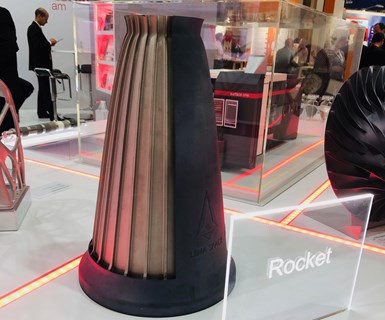
Oerlikon partnered with a small aerospace startup based out of UK called Lena Space to help the company use additive manufacturing to unlock new and efficient designs for key components of its systems, like this rocket nozzle. By 3D printing the nozzle, Lena was able to print the entire nozzle as one piece while introducing regenerative cooling channels that would traditionally be brazed or welded, adding additional weight to the part.
While the press releases and news announcements by aerospace manufacturers and suppliers flew fast and furious throughout the show, one company stood out for making two major announcements during the show’s first 48 hours. Oerlikon, a multinational technology group widely known throughout the aerospace sector for its surface solutions, advanced materials and materials processing, announced a partnership with MT Aerospace that is ultimately aimed at accelerating the adoption of metal 3D printing. The following day, Safran, Oerlikon, the French National Center for Scientific Research and the University of Limoges announced the creation in Limoges of a joint research laboratory, Protheis, and a technology platform, Safir — two complementary organizations specialized in surface treatments for aerospace applications.
Modern Machine Shop and Additive Manufacturing Media senior editor Brent Donaldson sits down with Oerlikon Chief Technology Officer Dan Johns to discuss the company’s newest partnerships, such as its new partnership with Lena Space. “To welcome disruptive innovation is one challenge. Achieving it is another,” Mr. Johns said. “This collaboration shows that we can do both.”
On the second day of the show I sat down with Dan Johns, Oerlikon AM’s chief technology officer, who talked about the value the company places on partnerships such as these, especially in the additive manufacturing arena. (Oerlikon AM is the additive manufacturing division of the company.) Mr. Johns said that Oerlikon seeks companies that inhabit cultures of innovation to bridge the gap between the aerospace industry’s needs and the technological realities of today. Case in point: Oerlikon’s partnership with a small aerospace startup based out of UK called Lena Space. Lena develops aerospace technology with an eye toward end-to-end rocket propulsion systems for launch vehicles that could bring satellites or other payloads into orbit. With Oerlikon AM’s assistance, the company used additive manufacturing to unlock new and efficient designs for key components of its systems, like its rocket nozzle. By 3D printing the nozzle, Lena was able to print the entire nozzle as one piece while introducing regenerative cooling channels that would traditionally be brazed or welded, adding additional weight to the part. Oerlikon assisted the company with rapid prototype construction of the nozzle as well as materials selection. The company also provided high-end thermal barrier coatings to the parts.
“Working with Lena Space gives us the opportunity to solve extremely hard technical challenges by bringing together Oerlikon AM, Oerlikon Metco and Oerlikon Balzers,” Mr. Johns said. The three brands work together to accelerate innovation. We learn faster and inspire each other to think in new and different ways. It is also a fantastic example of how our ‘open collaboration’ really works to break down conventional thinking. I haven’t heard anyone say, ‘We’ve tried that before and it didn’t work.’ To welcome disruptive innovation is one challenge. Achieving it is another. This collaboration shows that we can do both.”
The Next Generation of Aerospace Manufacturing

With the commercial aviation industry projected to double in the next 20 years, meeting the demand for passenger and freight aircraft will require new technologies and unprecedented manufacturing rates.
Learn more about the materials and processes that will shape next-generation aircraft in a collection of stories from Modern Machine Shop, Additive Manufacturing and CompositesWorld, available to read or download for free. Get it here.
Related Content
How to Meet Aerospace’s Material Challenges and More at IMTS
Succeeding in aerospace manufacturing requires high-performing processes paired with high-performance machine tools. IMTS can help you find both.
Read MoreSchwanog Custom Form Tools Reduce Cycle Times
IMTS 2024: Schwanog’s insertable form tool system supports the manufacture of precision parts for industries such as medical, automotive, aerospace and others.
Read MoreMachine Monitoring Boosts Aerospace Manufacturer's Utilization
Once it had a bird’s eye view of various data points across its shops, this aerospace manufacturer raised its utilization by 27% in nine months.
Read MoreHow a Custom ERP System Drives Automation in Large-Format Machining
Part of Major Tool’s 52,000 square-foot building expansion includes the installation of this new Waldrich Coburg Taurus 30 vertical machining center.
Read MoreRead Next
Mission critical: An additive manufacturing breakthrough in commercial aviation
The GE9X is the first commercial aircraft engine to reach production with significant additive content. The story of GE’s accomplishment and why it matters.
Read More5 Rules of Thumb for Buying CNC Machine Tools
Use these tips to carefully plan your machine tool purchases and to avoid regretting your decision later.
Read More