Aerospace Supplier Shifts to Tight-Tolerance Ventilator Parts: "We Weren't in This Business Two Weeks Ago"
Skilled Manufacturing Inc. is running seven days a week to produce ventilator parts that will help healthcare workers battle the coronavirus.
Share
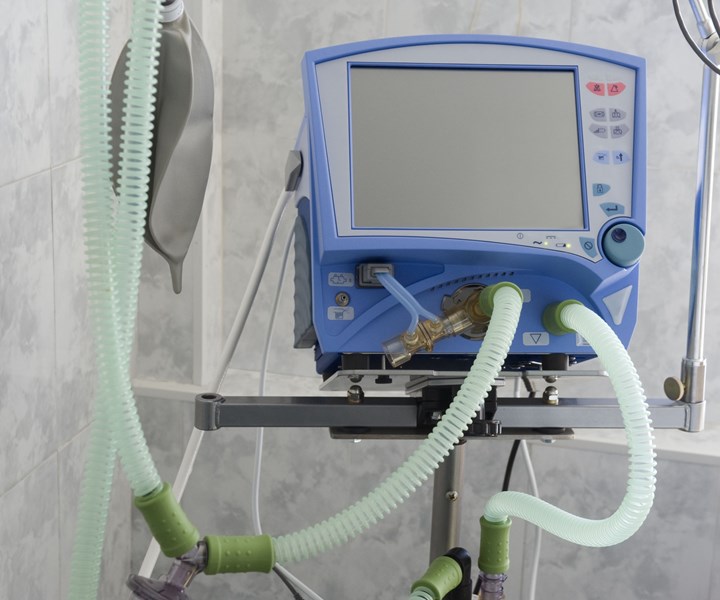
“We’re not doing this to make money, we’re doing this to save lives,” says Dodd Russell, CEO at Skilled Manufacturing Inc., a Tier 1 aerospace and automotive supplier located in Traverse City, Michigan.
Mr. Russell got the call from one of his major automotive customers on a Saturday morning asking if his company could help churn out 6061T aluminum parts destined for ventilators. Within an hour, he had 12 of his aerospace employees at the plant, ready to make it happen. After looking at the 2D blueprints of four parts, they went to work on the easiest one first, producing a prototype by Saturday night for submission. By Sunday, they had made a prototype of the second part, and by Monday, they had prototyped the third and fourth parts.
“At that point, I didn’t even have a purchase order. I told my customer that we would donate the parts if we were not chosen as a supplier. Luckily, our customer did choose us, but that’s not why we did it,” Mr. Russell says.
According to Mr. Russell, his entire supply chain has really “ponied up” to support them. For instance, the general manager of SMI’s aluminum supplier went in by himself Sunday morning to load the aluminum and deliver it to the plant. His tooling supplier sat in the parking lot calling suppliers Saturday night and was able to deliver tools by Sunday. There was a 72-hour turnaround time on all specials, Mr. Russell says.
“We weren’t in this business two weeks ago, but this is what Americans do when stuff like this goes on,” he says. “We didn’t plan on this. In fact, we just laid 150 people off in our automotive division the night before we got the call. Now, the 150 people in our aerospace division are working endlessly to support our main customers. This is our new reality.”
Mr. Russell commends job shops and certain other manufacturing facilities for wanting to do their part to make ventilator parts, but he can’t sugar-coat the reality that there is a certain baseline of tolerance requirements and cleanliness standards that must be achieved for some of these parts. SMI’s aerospace division is already perfectly set up to handle this new kind of work. The NADCAP certification, the clean room and the surface finishes that are standard for aerospace work made for a seamless transition for SMI to produce these medical parts. According to Mr. Russell, the ventilator parts are similar in surface finish and tolerance to the aerospace parts, which the company is accustomed to holding at 2 tenths. In some cases, the company even splits the tenths.
Even though his company went from running a 4/10 work schedule to seven days straight with two shifts running 10 hours each, Mr. Russell says his company is not at capacity. In fact, at the time of this writing, he had been approached by another organization and was in preliminary conversations about making parts for a different type of ventilator.
In the midst of this, SMI is also working to keep its employees safe. The plant is completely locked down — no outside visitors or suppliers can enter. Mr. Russell says they are following full CDC protocols using face masks, social distancing and thermal scanning. “It’s a Herculean effort for our employees just to get into the plant,” he says. He also has backups in place. “We have a plan for every person and every machine. There is no single-point failure.” These backup plans were already in place before the pandemic hit, as they are considered normal contingencies for aerospace work.
At the end of the day, Mr. Russell and the employees at SMI are just trying to do their part. “We live in a small town. We’ve known each other for a long time, and we all take a lot of pride in our work and workplace. This ventilator work is a testament for my employees. They want to stand up and be counted. We’re all just small-town folks who are working hard to save the lives of those in our town and our friends.”
Related Content
-
Supercritical Success for Medical Machining
High-pressure carbon dioxide coolant can dramatically improve the production rate of titanium parts while leaving no residue — an excellent fit for medical machining.
-
Ametek EMC Laser Cutting System Offers Through-Part Cooling
The new laser cutting system offers comprehensive Swiss machining capabilities, as well as through-part cooling and automatic part-handling options.
-
Grob Systems Inc. to Host Tech Event With Industry Partners
The 5-Axis Live technology event will highlight new machining strategies for optimizing the production of complex medical, aerospace and mold/die parts.
Related Content
Supercritical Success for Medical Machining
High-pressure carbon dioxide coolant can dramatically improve the production rate of titanium parts while leaving no residue — an excellent fit for medical machining.
Read MoreAmetek EMC Laser Cutting System Offers Through-Part Cooling
The new laser cutting system offers comprehensive Swiss machining capabilities, as well as through-part cooling and automatic part-handling options.
Read MoreGrob Systems Inc. to Host Tech Event With Industry Partners
The 5-Axis Live technology event will highlight new machining strategies for optimizing the production of complex medical, aerospace and mold/die parts.
Read MoreTungaloy-NTK PCD Grade Optimizes Dimensional Accuracy
The DX200 is an effective tool for machining application-specific components that demand high levels of material purity, such as metal medical implants and sputtering targets for semiconductor applications.
Read MoreRead Next
One Auto Parts Supplier's Shift to Ventilators: Now Making 1000s of Parts per Week on Die Delivered in Days
GM applying its supply chain expertise to enable successes such as aiding this ventilator maker to expand sourcing for 700 parts.
Read MoreBuilding Out a Foundation for Student Machinists
Autodesk and Haas have teamed up to produce an introductory course for students that covers the basics of CAD, CAM and CNC while providing them with a portfolio part.
Read MoreRegistration Now Open for the Precision Machining Technology Show (PMTS) 2025
The precision machining industry’s premier event returns to Cleveland, OH, April 1-3.
Read More