Choosing the Right Automation for Your Shop
Sponsored ContentThis robotic arm Is fully integrated into the machine tool, enabling machine tool operators with no previous robotics experience to operate it effectively.
Share
While most machine shops are investing in automation to some degree, it can be challenging to decide which form of automation is right for any given shop. While bar feeders are excellent for low-mix, high-production lathes, high-mix shops need to rely on more adaptable technology.
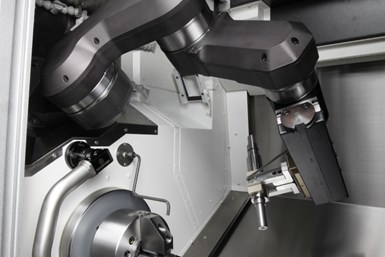
The ARMROID is a robotic arm that is installed inside an Okuma machine tool and integrated into the control. While its small footprint is desirable, the major benefit is the ability to program it using conversational controls and without needing a robotic specialist.
Robotic automation systems are frequently used in these scenarios, but they have two major drawbacks. First, the footprint of a robotic cell can often be enormous, sometimes as large as the machine tool it services. Second, robots often need dedicated personnel to program their movements, which not every job shop has access to.
Okuma has recently addressed these drawbacks with the ARMROID, a zero-footprint robotic arm that can be programmed by anyone experienced with the Okuma OSP control.
A Completely Integrated Robotic Arm
The Okuma ARMROID is a robotic arm that mounts inside a compatible machine tool and is integrated into the machine’s controller. According to Okuma Product Specialist Wade Anderson, the ARMROID is designed for shops that don’t have the staff needed to program a full robotic cell.
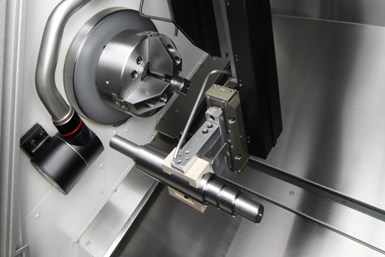
The ARMROID can be equipped with a parallel-jaw gripper (pictured) for moving parts. Additional options for end effectors include a coolant nozzle for carefully directing coolant and a dual-roller support system to improve the rigidity and damping of longer cylindrical parts.
Because the robot is integrated into the OSP machine control, any user familiar with using the machine tool is fully capable of programming the robot, and the robot and machine tool can be controlled using a single pendant. “There’s a conversational navigation window you use to tell the robot how to pick up a part,” Anderson says. “The user inputs the points the robot needs to reach, and the motion itself is generated automatically.” Additionally, during loading and unloading, the arm utilizes the machine’s own collision avoidance software to avoid damaging parts or equipment.
The ARMROID can be mounted inside both the Okuma LB3000EX II horizontal lathe and the MULTUS B250 II multitasking machine, where it is designed to be able to tuck itself out of the way during machining. Because it is designed only for use in these two machine tools, the company was able to integrate it more fully than most automation systems can achieve. In many ways, it functions as simply another part of the machine tool.
The gripper for the robot comes in a parallel-jaw formation for parts up to 5 kilograms (11 pounds), as well as in a three-jaw setup that can hold parts up to 10 kilograms (22 pounds). The latter jaw is available only for the MULTUS B250 II.
Not Just a Robot Arm

The ARMROID is not the only integrated automation option Okuma has on offer. The STANDROID is a robotic cell attached to the exterior of the machine tool, but it is still fully controlled through the machine controller.
In addition to moving and positioning parts, the ARMROID can use different end effectors to accomplish other tasks such as spraying coolant and providing a cylindrical part with support. As with other aspects of the ARMROID, the three end effectors (workpiece gripper, workpiece support and coolant wand) can be exchanged automatically using the machine tool’s controller.
The workpiece-support end effector uses a dual-roller system to improve the rigidity of the part, providing damping and reducing chatter. This effect is especially apparent with longer parts. Additionally, the coolant wand’s directed spray can clear chips that other systems can miss. Even when other coolant systems are already in use, it can clear chips that gather in crevices. “Being at the end of a robotic arm makes it much easier to get into nooks that can gather chips during machining,” Anderson says.
The end effectors are stored in a drawer system located in the machine tool wall. Without a programmer needing to input any precise coordinates, the system can exchange any end effector mid-process. When the correct end effector is equipped, the drawer safely stows itself out of the way. During a single machining cycle, the ARMROID is able to move parts into and out of the machine clamping system, exchange the gripper for a coolant wand or workpiece-support end effector, and assist in machining.
Machine Cell Setups
The ARMROID can work with many kinds of part stockers, and it is reliable enough for lights-out machining. Because the potential setups are so flexible, it can even be used as a cell for both attended and unattended machining. “For example, there are stocker options with wheels,” Anderson says. “You can slide it out of place for a shift with an operator attending the machine, then slide the stocker back in for a couple shifts lights-out.”
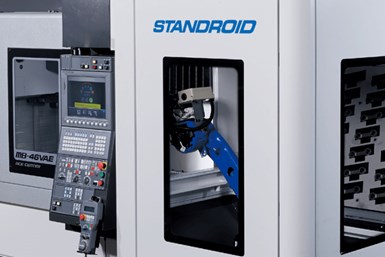
Both the ARMROID and STANDROID can be operated using the same pendant used to operate the machine tool. This integration enables them to use the machine’s collision avoidance software to prevent crashes.
Additionally, Okuma has released the STANDROID, a robotic arm that is attached externally, but still fully integrated into the OSP. This system can integrate into a wider range of machine tools, but still benefits from using the machine tool’s control and collision-avoidance systems. Like the ARMROID, it can use a variety of different stockers and bypasses the need for personnel with robotic programming experience.
For more information, visit Okuma.com/automation-systems.