Adaptive Robotics for Improving Productivity
Stäubli’s robotic machine tending and collaborative mobile robotics are designed to optimize process efficiency and boost productivity.
Share
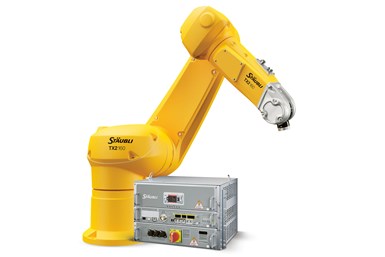
The TX2-160L HDP with CS9 controller. Photo Credit: Stäubli
Stäubli’s stationary TX2-60 Humid Environment (HE) robot and TX2-160L High Dynamic Precision (HDP) robot are machine tending technologies designed to be adaptable for a variety of industries.
The TX2-60 HE robot is capable of washing parts and tools, working in tandem with a HelMo mobile robot. It can load and unload products before inspecting and marking them. As it carries out these tasks, the HelMo robot glides along autonomously, loading and unloading pallets of finished parts with accuracy in the range of tenths of a millimeter, the company says. With a CS9 controller, three laser scanners, a tactile enclosure and optional safe skin, it is said HelMo is capable of working safely alongside humans while relieving them of repetitive and dangerous tasks.
The company says the TX2-160L HDP robot is capable of performing high-precision laser cutting processes with good path accuracy at various cutting speeds, high rigidity and the ability to access complex parts. It is designed to be repeatable across all trajectories and orientations, accommodating different shapes, contours, thicknesses and other parameters. A versatile toolchanger is said to enable it to switch from cutting to inspection.
It is said the TX2 range of six-axis industrial robots are suitable for applications in many manufacturing environments because of special features such as a compact design, floor and ceiling mounting options, resistance to harsh environments with a fully enclosed IP65 and IP67 wrist, repeatability and simple integration into existing production cells and lines with various control options. The industrial robots also feature a reach of 1,710 mm, load capacities ranging from 2.3 kg to 40 kg, and Industry 4.0 compatibility with the CS9 controller.
TX2 robots all operate on the same smart CS9 control technology, making it easier to implement multirobot solutions in digitally networked production environments.
Related Content
-
3 Ways Artificial Intelligence Will Revolutionize Machine Shops
AI will become a tool to increase productivity in the same way that robotics has.
-
Increasing Productivity with Digitalization and AI
Job shops are implementing automation and digitalization into workflows to eliminate set up time and increase repeatability in production.
-
Which Approach to Automation Fits Your CNC Machine Tool?
Choosing the right automation to pair with a CNC machine tool cell means weighing various factors, as this fabrication business has learned well.